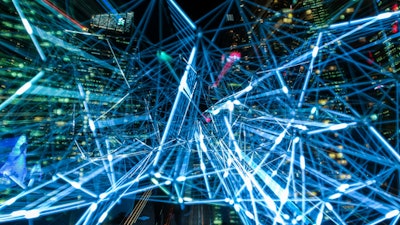
It is widely accepted that the worldwide supply chains are going to look different after the Coronavirus disease (COVID-19). And, it won’t be much of a surprise if there are already vast numbers of companies planning the changes they are going to make.
It makes sense. However, why is there a need to make a “new” plan? Why isn’t it possible to review and strengthen an already available Plan B? Perhaps in many cases, the reason is that there wasn’t a Plan B.
Supply chain and procurement executives, in general, had the opportunity to be better prepared for the COVID-19 pandemic, or any other supply chain-disrupting event.
Being a worldwide phenomenon affecting both sides of supply and demand, the experience will look very differently for each company. There will be however one factor that will arise constantly in the post-mortem review—offshoring, most commonly with China.
Permanently, supply chains have something in common—they have to become more cost efficient to deliver savings, with variations here and there, but “everybody doing the same.” Perhaps it became a “rule of thumb” to select the “best strategy,” and without paying too much attention, the system became at risk by concentrating much of the manufacturing for the world in a single location. By some estimates, China doubled its share of trade with the rest of the world from the early 2000s to today, quadrupling its contribution to world’s gross domestic product. Dun & Brandstreet estimates that 51,000 companies in the World had direct suppliers in Wuhan, and at least 5 million companies had upper stream suppliers located in the Wuhan area.
Granted that it is easier to do a post-mortem than to future-proof, but it has been the one with the largest impact and fastest spread experienced in the history of humanity. No one can cope with that easily. The point is, that for making the decisions for shaping the future supply chains, there is a need to look closer and learn more from the past.
Here are the learnings and acknowledgements needed to assimilate from this experience:
· Transformational, deep and true innovation in the supply chain has been scarce. Results across companies and industries were delivered with only one tool—sustainability. There is a corollary to this, or perhaps a cause, depending how it is seen. Basically, we stopped learning. We thought the work was done when selecting a cost-effective supplier. But, the work wasn’t done.
· How many of those 5 million companies were aware that they were connected to Wuhan? In the bigger picture is, how many companies have actually properly mapped their supply/value chain? Some consciously made the choice to manufacture as much as possible abroad, while others didn’t know how things actually looked like. The fast speed of today’s business environment and the scarce abundance of resources has distracted companies from understanding the details of their supply chain. But, we now have learned that is needed, and will be needed to be done again. Make sure that this time it doesn’t collect much dust.
· How many companies truly knew what their sourcing strategy actually was? Organizations are dynamic as they have ever been, with mergers and acquisitions activity, evolution and changes in supply chain technology, geopolitical changes and mobility of the people causes that knowledge is diluted, or even lost. Why are we working with this supplier for the past three years? Why did it make sense to select it at that time? Are those reasons still valid? Is such a supplier having the same profile now? Do we need the same?
For the sake of communication and time availability, we ask communication to be short and concise. But, a supply chain or sourcing strategy is so complex and with so many variables that few slides are not enough to communicate it properly. When somebody new is in charge, most of the accumulated knowledge is gone with the person that left. Leaders not only challenge people with tough questions, but also make sure it is possible to access their answers afterwards. Ask people to spend time describing and explaining all their thoughts in prose. Write down a “crash course” in their strategy, so when the next time somebody needs to take over, they are properly in context and they can think “aha.”
· COVID-19 is a first for humanity, but disruptions to the supply chain are more common. Think Ebola, Swine flu, SARS, MERS. Disruptions are not only to be caused by a disease; natural causes such as earthquakes and hurricanes have happened too. Man-made disruptions also exist, such as the 2008 financial crisis, Brexit. There have been opportunities to learn enough to have a playbook or business continuity plan ready. A “Plan B” for what can be done in case of emergency—fast track approval of suppliers and materials, previously approved suppliers and materials, substitute materials and alternate bill of materials, supplier relief program, etc. During the COVID-19 pandemic, how many companies were able to base their decisions in past experiences?
Let’s be conscious that doing all of the above has a bonus. In past years, surveys have shown leaders express concern of the talent available at present and future to manage their supply chains. The good news is that if people resources are dedicated to execute the activities described above, talent is being nurtured. If an intern or management trainee is involved in mapping the supply chain, and is able to quickly access to the knowledge of the supply chain decisions made prior, it can readily offer a baggage of few years work experience, but with more years knowledge of procurement and supply chain management.
The ideas shared here are also an opportunity to strengthen the talent pipeline by helping people develop, while by the same token making the organization more robust and resilient over time.
Let the COVID-19 pandemic help educate us that true supply chain resilience and significant part of future proofing doesn’t only reside in objects and third parties, but it also resides on the capacity of the people to learn and in the capacity of the organization to access what people have learned.