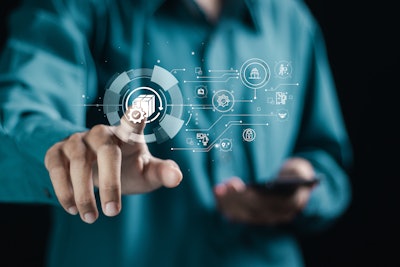
In a fast-paced business environment, it is easy to overlook the importance of robust inventory management. Neglecting this critical link in the supply chain can lead to significant disruptions, increased costs, and lost revenue opportunities. Ensuring accurate inventory data, understanding what variables impact inventory, and applying metrics drive decision making, are key to mitigating risk and ensuring client satisfaction and providing the flexibility to implement predictive technology within a company.
What is ideal?
An ideal inventory level is calculated at the SKU/stock location and aligned to shipment fulfillment targets (OTIF). This allows for inventory that meets customer order demands without tying up excess working capital. As a first step, the company must align with a high-level vision for service and operations target. Utilize the following drivers of inventory needs via an SIOP process.
• Service level targets
• Inventory drivers such as customer order and supply variability
• Scenario models that illustrate how inventory models impact inventory
Once this is complete, the team can work toward inventory goals with tracking metrics.
Metrics for inventory
If supply and demand were 100% predictable, inventory could be planned to match shipments perfectly, eliminating the need for metrics or inventory buffers. However, inventory buffers are necessary, and it is important to calculate and document these buffers using data, rather than institutional knowledge.
When considering inventory metrics, utilize the inventory drivers that have been determined and consider how external forces may affect inventory requirements. Review these areas frequently to ensure continued alignment with company goals and real-world scenarios. If accurate data is available in ERP, the system can alert the planners to inventory levels outside a desired range. When well-designed, these systems can be an invaluable tool in determining buffer stock levels and mitigating risk.
Measuring and trending over time will provide the most beneficial metrics. Here are some metric trends to help clients and employers gain better control over their inventory.
Days of supply: Current inventory position divided by the number of anticipated units of sales or consumption. This provides a volumetric view of inventory relative to needs, which is not affected by product cost. Calculated at SKU/location level.
Materials in-range [percentage]: Define minimum and maximum stocking positions and take a snapshot of how many materials are between those two limits.
Inventory at-risk [percentage]: Inventory in hold status, off-spec, or approaching the end of its shelf life. Reviewed by individual batch of inventory.
Slow moving inventory [percentage]: Inventory that is significantly over the target range for extended periods of time (also generally have high DOS and aging).
Inventory stocked-out [percentage]: Ideally, no more than the tolerance set by the cycle service level (CSL). If the CSL is 95%, no more than 5% of materials should be “stocked out” at any time.
Inventory accuracy: Inventory adjustments (in the system) as a percentage of total inventory for a given period.
Metric trends over time provide deep insights to how inventory needs change as drivers change and provide planners with a direction to focus improvement efforts. Industry-wide benchmarks for inventory performance are largely unavailable and can be misleading due to the unique nature of inventory needs within a business
The most common improvements are the result of adjustments to business processes and decision-making. This enables the team to focus on rightsizing and data-driven decisions to ensure the optimal inventory level and mitigate risks.
Data analytics
Data analytics and visualization tools are another useful tool in inventory planning and decision making. In this method, the planner uses the data analysis to create a story of the part or product. These stories help communicate complex trends, patterns, and areas of improvement to stakeholders. Effective inventory storytelling aids in better decision-making and fosters a culture of continuous improvement within the organization.
Collect and integrate data: Gather data from various sources such as enterprise resource planning (ERP) systems, inventory management software, and supply chain analytics tools. Integrating this data provides a holistic view of your inventory.
Identify trends and patterns: Analyze the data to uncover trends, patterns, and areas for improvement. Understanding these elements is crucial for making informed decisions.
This is also the point where data can be used in further AI capacities, such as predictive analytics, machine learning, and robotic process assistance (RPA).
Analyze and visualize data: Use data analytics and visualization tools to create interactive dashboards and reports. These tools help in making sense of complex data and provide clear insights into inventory performance.
Drive decisions: By following these steps, businesses can effectively implement inventory storytelling, leading to more informed decision-making and enhanced supply chain capabilities. Adding an additional layer of scenario analysis to show how requirements change as operating parameters change also allows decision-makers to explore and proactively understand the results of an improvement investment.
AI, predictive analytics and machine learning
Imagine your system could identify trends in your operations and correlate it to external data such as consumer trends, weather, sporting events, and news to make predictions on what you’re going to need for inventory. This technology exists today and is growing in use through AI systems integrations. Finding the correct data points and system use are key to creating an AI integration that can be leveraged for specific markets.
It the simplest form, AI and predictive analytics can be used as a continuous inventory optimization tool that measures supplier and production lead times and customer demand against a target service level and is continuously improving target inventory levels to right size for changes in demand and supply.
However, buyer beware, AI implementations require a strong, preexisting process that can weather fluctuations in demand and supply (such as a SIOP process). Without a strong, preexisting process, implementing AI tools can create new challenges and cause surprising reverberations in your supply chain execution.
Conclusion
Inventory management is a multi-faceted approach to ensuring that the goals of a company are implemented in a process driven way to ensure that raw materials are available in ideal quantities to fulfill customer orders. Investing in inventory management processes, clarifying roles, responsibilities, and decision-makers enables companies to proactively address potential supply chain disruptions, optimize their operations, and ultimately improve their bottom line. Don't overlook the importance of inventory management, it's an essential component of a successful supply chain strategy.