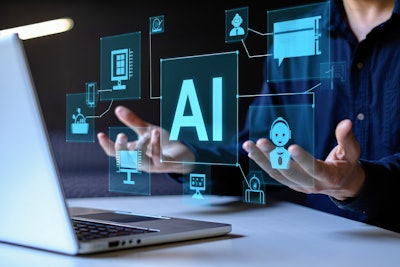
While consumer spending and employment data don’t yet show that the economy is taking a downward turn, some economic experts such as the Federal Reserve are nevertheless concerned. In a statement issued in May, the Fed says, “Uncertainty about the economic outlook has increased further. The Committee is attentive to the risks to both sides of its dual mandate and judges that the risks of higher unemployment and higher inflation have risen.”
Of course, economic predictions are always uncertain, but the wisest course for manufacturers is to take measures that provide them the agility they need to chart their way through difficult economic times and potential Black Swan events. Even if a recession does not occur — something every manufacturer is hoping for — all organizations will benefit from greater agility, especially in an uncertain environment with rapidly changing tariff policies and a volatile supply chain.
Artificial intelligence (AI) can be a key enabler of advanced capabilities that enable agility, and in most cases, these capabilities don’t require deployment of a bigger than life large language model (LLM). Generative AI (the kind that requires an LLM) gets most of the attention these days, but other forms of AI are initially more useful to manufacturers and often more readily available, because they are either already included in - or easily integrated with - an ERP platform.
Common types of AI and their applications for agility
Here's a brief primer on common types of AI other than generative.
Traditional AI is rules-based, and while it can improve over time at the task for which it is designed, it can’t do the same for other tasks. In logistics, this type of AI is often used for route optimization.
Cognitive AI uses natural language processing and machine learning (ML) to power machine vision in use cases such as quality control, and it also has applications for speech recognition.
Predictive AI crunches historical and current data to unearth patterns that help it forecast events and trends. This type of AI powers inventory and sales projections, and can also analyze supplier patterns to predict the timing of deliveries.
Here’s how these different types of AI can be applied in manufacturing to gain agility.
Multi-sourcing is a key capability that provides manufacturers with alternatives to find the best availability and pricing on raw materials and components amid rapidly changing conditions outside of their traditional supply chain, and managing multi-sourcing manually is not realistic, as it can become very complex very quickly. Traditional and predicative AI can simplify multi-sourcing management, and often these capabilities are already present or can be easily integrated into the ERP platform.
Related to multi-sourcing, just-in-time inventory and supply chain management enables management to adapt quickly, no matter what comes their way. By analyzing historical inventory data, predictive AI can assess current conditions and recommend actions to ensure that inventory is kept at an optimal level, even during sudden changes. In combination with multi-sourcing, this capability enables manufacturers to reduce costs without worrying that they’ll be caught short in the event of supply chain disruption.
Predictive AI isn’t limited to inventory and supply chain use cases. It’s commonly used to power predictive maintenance, which enables manufacturers to take action before critical equipment goes down, which lowers costs and increases productivity. In fact, predictive AI can be applied to nearly any business problem, analyzing internal and external data to provide real-time, actionable insights that enable smarter, faster, more accurate decisions.
Simpler solutions to increase nimbleness
As useful as AI can be to enable agility, manufacturers don’t need to adopt advanced technologies to increase their nimbleness. For example, four simple strategies can significantly improve warehouse productivity and efficiency without requiring a large time or financial investment:
Optimize the physical layout: Engage warehouse staff for improvement ideas, implement clear labeling systems for bins and aisles, and arrange inventory based on picking frequency. Some manufacturers increase their useable floor space by one-third just by reorganizing the layout.
Streamline picking processes: Sort packing slips by bin location to reduce picker travel time, consolidate multiple orders into single pick lists, and enable suggested picks for practices like first-expire-first-out (FEFO), if using a warehouse management system.
Upgrade barcode scanning technology: Modern handheld devices load pick lists in seconds versus minutes with older equipment. Even a 30-second improvement per scan can save many hours weekly across multiple pickers and shifts.
Implement real-time pallet tracking: RFID tags or IoT sensors integrated with ERP systems enable employees to quickly locate items, which is especially useful for warehouses with many SKUs but low volume per item.
These cost-effective solutions can typically be implemented within one to two months and help manufacturers and distributors reduce costs and increase efficiency, all of which lays the foundation for greater agility.
Though there are signs the economy could experience a downturn, it’s impossible to know exactly what course the economy will take in the coming months. One thing, however, is certain: manufacturers will benefit from additional agility no matter what the future brings — especially if it brings a recession.