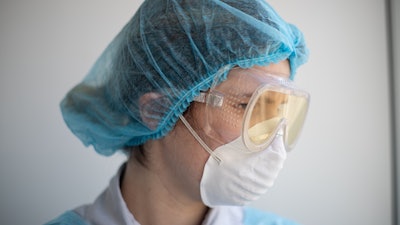
Organizations across all industries are being forced to shift their strategic focus, internal operations and external output as a result of the ongoing Coronavirus disease (COVID-19) crisis. In particular, manufacturers see significant shifts in demand, as well as challenges to their fulfillment capabilities as their supply chains and workforce are stressed by this pandemic. As manufacturers reorganize operations to meet the new requirements, they also need to manage the financial and operational disruption that comes with the current global crisis. For manufacturers whose goods and services are non-essential to the international COVID-19 response, the crisis is an existential threat. For manufacturers engaged in the production of critical supplies such as personal protective equipment (PPE), the challenges are different, but also daunting.
Minimizing negative impact
The crisis has driven dramatic shifts in demand patterns, and manufacturers must adjust to protect themselves. Some are splitting shifts and cleaning all equipment between shifts to lower the possibility of a COVID-19 infection completely shutting down their operations. All are reorganizing shop floor operations to protect employees and proactively respond to the virus. For manufacturers not making essential supplies, managing the financial impact of the crisis is most critical. Many manufacturers will be facing loan and credit payments that may put them at risk of bankruptcy. Companies will need to restructure cost priorities to make these payments — whether they are shifts in budgets, salary adjustments, R&D or other moves. With the financial impact comes the necessity for layoffs and furloughs for the shop floor staff and management. As manufacturers look to create a profitable remote-work infrastructure, prioritizing employee skills development initiatives for these impacted workers is crucial to maintaining a productive workforce, while adapting to the potential long-term impacts that the crisis will have on the industry overall. Manufacturers pivoting to produce COVID-19 relief supplies have proven to be at least somewhat effective in keeping a workforce engaged while addressing the country’s PPE shortfall. Unfortunately, these financial and operational issues tend to cause disruption across the entire supply chain. The industry will start seeing material shortages, impacting distribution and logistics at each point of the value chain. In response, we’ll begin to see a restructure of materials sourcing to become hyper-localized. Manufacturing operations will become increasingly agile, investing significantly in new and emerging manufacturing processes (e.g. additive manufacturing). New business and employment models (e.g. contract staffing) will also be adopted to help cut operational costs wherever possible.
Navigating the short term
Now that we are moving past the initial shock, there are two phases of impact that manufacturers must endure — each with its own set of challenges and desired outcomes. In the upfront, manufacturers must do everything they can to keep operations up and running. In order to do this, there must be a streamlined flow of information and communication with employees, customers and third-party partners to respond to any operational issues in real-time. New digital technologies are critical to make this possible. Investments in collaboration suites, chatbots, visibility into transportation and logistics, and other digital tools will allow for preventative and proactive communication to all relevant parties in order to respond to operational crises immediately — or even get ahead of issues before they arise. It is critical that manufacturers understand employee, partner and customer feedback and demand amidst the crisis, and real-time analytics make this possible for those managing supply chain operations. Besides providing insights into stakeholder sentiment, analytics can help minimize unnecessary costs, optimize energy savings, aid inventory turns and visibility across the entire value chain. Manufacturers will also need to invest heavily in a remote-work infrastructure that inspires collaboration and productivity across the entire workforce. This is vital in maintaining operational efficiency and shop floor optimizations — ultimately meeting customer demands from afar. For companies that rely heavily on field sales teams, enabling your talent to convert to inside at-home sales roles is critical to stabilizing your company, understanding current demand, and when the time is right, preparing for the pivot from crisis to growth.
The road to recovery and growth
As the dust begins to settle, manufacturers are already looking for ways to rebound and transition back to “business as usual” even though the New Normal will not be reflective of pre-COVID-19 behavior. Manufacturers will need to closely evaluate customer needs and adjust operations accordingly. While the task may seem daunting, there is hope. Manufacturers have access to technology to assess, understand and respond to shifts in demand and operational disruption. How manufacturers make decisions, work, engage their customers and collaborate with their supply chain and partners has forever been changed. It will be where and how manufacturers choose to invest that will decide their fate on the tail end of this specific crisis and possibly prepare them for the “next COVID-19.” Companies that invest strategically in a deeper digital experience along with agile business and operational processes, real-time customer and operational data analytics, and long-term restructuring of shop floor operations will ultimately find success in the economy that emerges following this pandemic. Organizations that use this opportunity to plan a new future by focusing on improving their customers’ experience and investing in and leveraging digital technology to be more flexible and agile will put themselves in the best possible position for the coming years.