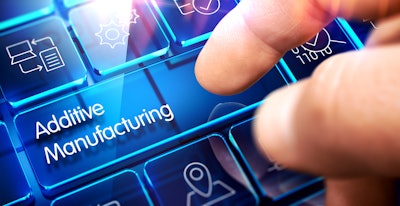
In a July 2022 Summit about building multilateral supply chain resilience, U.S. Treasury Secretary Janet Yellen drew direct parallels between the current state of the world and the manufacturing problems that could persist into the future.
“The necessity of [supply chain resilience] has been illustrated clearly by the events of the past two years, first by COVID-19 and our efforts to fight the pandemic and now by Russia’s brutal war of aggression in Ukraine,” Yellen said. “Together, they have redrawn the contours of global supply chains and trade.”
Her speech indicated various solutions to help the country, including onshoring initiatives meant to shift the production operations of American companies stateside. One technology that should be top of mind for decision-makers seeking to produce locally and as-needed is additive manufacturing (AM).
Sometimes referred to as industrial 3D printing, AM is positioned to help U.S. manufacturers offset the negative effects of the current economic turbulence. The global AM market is set to grow to more than $50 billion by 2030 and is an opportune, scalable method for manufacturers to produce plastic, metal or rare precious metals on an as-needed basis from computer-aided design (CAD) models.
As we emerge from persistent pandemic lockdowns and labor challenges, efforts to rethink manufacturing centers have accelerated. Yet to-date, the United States continues to struggle with creating economic priorities that favor its businesses and bring manufacturing back onshore. The understanding and overall acceptance of AM is one of the struggles, and the time for AM is now.
The current state of the AM industry
AM is something that can bring advantages at the beginning of the value chain. Speed to market, freedom of design, the ability to combine functionality and light-weighting are all benefits organizations latched on to when additively manufactured parts became a reality. What else has become evident over time is the added downstream advantages of AM.
For thousands of years, humans have chipped, drilled, bent and assembled components. More recently, this is done cheaply overseas in places with little to no regulations. Sounds fine until war or viruses step in and all items – from medical equipment to applications related to national security – cannot be produced or delivered quickly enough to meet demand. Many production steps are eliminated with AM, components can be produced locally or regionally when needed, and the net parts created many times have superior characteristics and performance. The knowledge needed to be successful in AM has also accelerated during the past decade, or so, and the technology has become more attainable, yet AM has not come close to mass adoption
Given the current economic climate, the imperative has grown to reduce the distance between where organizations produce parts and finished goods, and where they are marketing or selling the finished product. For example, if a hospital system in Oklahoma needs medical components or protective gear (PPE), rather than wait for a ship from Asia, what if they could produce what is needed on-site? Or at least in the same ZIP code? It is happening now, and all manufacturers can gain the same supply chain benefits.
Organizations are now leveraging AM to create a distribute production model, close to their customers. Result: no warehousing, less shipping and more sustainable parts being delivered on-time. Inventory can now be digital, and digital twin means the same part can be produced the same where, whenever their AM capabilities exist.
Because 3D printing produces net or near-net parts, AM also makes the production process less labor-intensive. Perhaps the primary reason that products are made elsewhere, like Asia and Latin America, is that companies had access to lower-cost labor. With AM, labor costs related to production and assembly steps are minimized or eliminated.
Industries like aerospace, power and energy generation and healthcare were all early AM adopters. In fact, aerospace was a driving force of how AM was able to revolutionize production. These days, the automotive industry, long regarded as an unlikely market for AM due to the typical high production volumes are also beginning to take AM seriously, particularly with the advent of clean sheet designed electric vehicles.
But all this begs the question: Why hasn’t the United States already shifted its focus on AM as a key piece of the onshoring puzzle?
Demonstrating AM demand for supply chains
In May, President Biden recently announced the Additive Manufacturing Forward (AM Forward) compact. Convened by defense ASTRO America, AM Forward is an official agreement that brings together some of the country's largest manufacturers to spark AM support and adoption across their U.S.-based suppliers with a specific eye toward small-to-medium-sized business (SMB) operations. To promote AM investments in their respective supply chains, the agreement states that larger OEMs will purchase up to 50% of sourced parts from producers leveraging AM. These AM produced parts will then find their way into the machinery or the production line of bigger companies as a sort of on-ramp for investments in domestic AM to build additive ecosystems for the future.
By encouraging AM production, there are several benefits AM Forward is seeking. First, a new generation of AM-trained workers are strengthening the workforce and adding new job opportunities in the United States. Second, the risk of interrupted supply chains is minimized, and parts can be produced in an entirely new way and onshore. Lastly, the parts/applications being produced are of superior quality, do not require warehousing, and can eliminate most of logistics associated with far-flung operations.
Full AM adoption and what that will mean for U.S. manufacturing will come down to metrics, specifically the primary governing factor of cost per part. At lower volumes, AM cost per part is very competitive (many times superior) when compared to traditional manufacturing. But that balance drops when higher order volumes are involved, which is obviously a fundamental component of manufacturing. That means there is less motivation for organizations to make an AM change. This is a bit shortsighted as AM provides cost efficiencies across the entire business that must be taken into account, so “thinking AM” requires more than simple cost per part analysis and must viewed through the lens of the complete product lifecycle of designing, producing, and servicing products.
Organizations that have successfully implemented their AM programs are many, but a majority of manufactures are working from a business-model playbook written in the 1980s and 1990s hyper-focused on cheap overseas sourcing. As we have so clearly witnessed in the past couple of years, this model is risky, and the time is ripe to rethink how and where we manufacture what we care about most. As AM is accepted and becomes an integral part of manufacturing operations during the next decade, localized manufacturing will return to our shores and play a significant role in reducing our reliance on global supply chains.