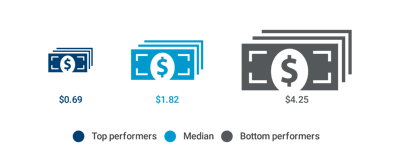
Financial measures are often the first indicators of process performance that executives examine. A key performance indicator for procurement looks at the total cost to order materials and services, the most transactional process within procurement. The total cost to perform the process “Order materials and services” per $1,000 in revenue is comprised of relevant personnel, related systems, allocated overhead, outsourced functions, and other costs for that process.
As shown in Figure 1, APQC’s Open Standards Benchmarking data in procurement reveals that there is a sizable difference between top performers and bottom performers with respect to the total cost to order materials and services. Top performers spend $3.56 less per $1,000 in revenue for this process than bottom performers. For an organization with $1 billion in annual revenue, this is a difference of more than $3.6 million in costs associated with ordering materials and services. Given that a significant focus for the procurement function is reducing costs, this is an important improvement opportunity.
As part of procurement, ordering materials and services may seem straightforward, but this is where many organizations incur much of their procurement costs. Figure 2 shows where the money goes within this process: 42 percent of the cost to order materials and services is personnel cost.
Performance drivers to examine when seeking to reduce the cost of ordering materials and services include:
- organizational structure (e.g., the financial impact of centralization versus decentralization or removing redundancies),
- technology (e.g., how to leverage technology and automation to reduce costs and shift labor costs to more value-added processes within procurement such as managing supplier relationships),
- strategic outsourcing of non-core tasks, and
- key practices related to the process (people practices, increasing role clarity or accountability, procedures, protocols, etc.).
Costs can also be reduced through process mapping to identify opportunities for improvements to the process and barriers to remove such as bottlenecks, unnecessary handoffs, lack of important process documentation, and other blockages preventing streamlined activities.