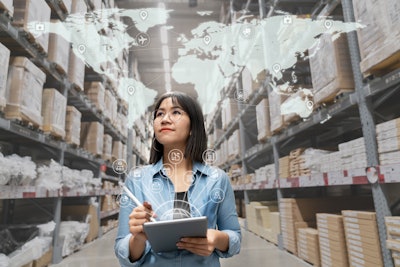
Supply chain management (SCM) connects the entire manufacturing process, from sourcing and procurement of raw materials, through efficient production, delivery mechanisms to move products to distributors and customers and even the systems for returning unwanted or defective products. Getting this right is make or break for any business.
This highly complex ecosystem of processes is influenced by external factors beyond the control of the manufacturing business. It is essential to understand that customers see the supply chain and the manufacturer as one and the same. Failure to deliver the right goods on time will be perceived as your responsibility. Customers generally won’t care if the problem originated with your supplier, or in the transportation mechanisms. If you can’t fulfill their order when they want it, you may lose their business for good.
Marketplaces and supply chains are global. Brexit has highlighted the issues of UK manufacturers relying upon external suppliers when circumstances change. Previously harmonious relationships between suppliers and manufacturers have been tested by the change in rules following Brexit. In one case, a UK-based chemicals company found themselves unable to ship their own orders, not because they couldn’t produce the chemical, or even bottle it, but because the bottle tops were held up in transit from the supplier in Germany. Another UK producer who had previously always sourced their main raw material from Europe is now encountering problems with receiving it, as haulers were reluctant to take the job and risk-bearing the costs of significant border delays. Eventually, the service was secured at double the usual shipping rate but unfortunately, the goods are now stuck in queues with no arrival information available. In both cases, these UK manufacturers’ production lines are stalled and their customers may well be looking to take their future business elsewhere.
Consumers are increasingly aware of ethical, environmental and sustainability issues, highlighting the need for traceability and transparency around the source and sourcing processes of components and raw materials. A well-managed supply chain allows easy traceability with evidence data immediately available if required. Traceability is also important in maintaining efficient quality control. If defective goods are produced, quickly identifying and rectifying the problem can save the manufacturer substantial financial and reputational costs. Whether the problem lies with a faulty component or sub-standard raw material; a malfunctioning machine or inexperienced machine operator; even careless storage and handling issues in the warehouse or in transit; a digital cloud-based SCM solution connects all of the processes and can quickly identify where problems occur. Customer confidence can be managed more effectively if occasional faults are seen to be dealt with immediately and decisively.
Begin with establishing good relationships with key suppliers, treating it as a two-way street. Their business relies on satisfying their customers, so even if you’re not their biggest customer at the moment, you should still be very important to them. Communicate, give feedback and keep them updated with changes in your business needs so they can continue to meet them. Tell your suppliers if a particular market is growing, or if you are starting a new production line that will need additional supply. It’s important to carry out due diligence when identifying prospective suppliers, for example finding out who else they supply to and if possible, what their experience is. If your supplier fails to deliver on time, you will fail to deliver on time. Throughout the relationship, it pays to be mindful of potential issues that could also impact your business. A change such as reducing credit terms may indicate cash flow problems that might cause problems for you down the line.
Efficient SCM is also reliant on your delivery mechanisms where again, it pays to research and identify the most reliable and suitable services for your own business and product. Price isn’t always the main consideration here, particularly if your product has a short shelf life or specific storage requirements. As next-day delivery becomes ever-more common, getting goods to the customer quickly is an increasingly competitive business, so the location of the hauler or delivery service and the speed at which it can get goods from A to B might be worth paying more for. A digital SCM solution can help by modelling different scenarios depending on the data input, so you can make fully informed decisions.
Digital SCM software helps with managing materials in the warehouse and facilitates cost and time-saving processes, including just-in-time ordering and first-in/first-out inventory management. These are critical in helping eliminate problems with out-of-date stock or obsolete components and to maintain cash flow. The entire supply chain can be automated end-to-end. Traditional spreadsheets are difficult to update or use to pinpoint specific information quickly. Cloud-based solutions allow multiple users across the supply chain process to have visibility up and down the chain and model different scenarios and outcomes according to small changes.
Another growing field in the supply chain is returns management and how to absorb the costs of returned goods. The restrictions created by the Coronavirus disease (COVID-19) pandemic have driven an increase in online retail, and a subsequent increase in unwanted, defective or damaged in transit goods returned. An efficient and easy returns process has a significant influence on customer satisfaction and loyalty. Businesses using designed-for-purpose SCM software can reduce the time and cost impact of returns, making the most of in-built workflows to simplify the process.
Even small and medium-sized businesses should choose digital solutions that can grow with evolving needs, integrating automated systems for material requirements planning (MRP); inventory management and stock control; management and distribution; together with the accounts department; order fulfillment; customer relationship management (CRM); and HR to optimize staffing levels in line with production. Seamless solutions that are designed to complement and work together provide intuitive and uncomplicated workflows and systems for speed and efficiency. Optimized SCM means processes are managed at every step, resulting in reduced costs and risks and increased profits, reputation and competitive advantage.