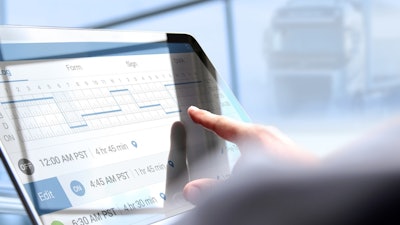
Systematic advances in technology spawn new problems in greater numbers in virtually every sector of the economy. But, supply chain problems are uniquely complex due to the fact that there are so many dependencies in the chain. A broken upstream link can impact every other downstream link. Often, these links are geographically diverse, crossing borders and oceans. This makes them subject to systematic geopolitical and weather-related risks, not to mention the risks associated with a global pandemic. So, when a problem presents, it may be exceedingly difficult to trace its origins. But, it’s also increasingly important that we do so.
Complicated problems are best solved using a structured problem-solving method. The one thing all problems have in common is the fact that they are subject to cause and effect. This commonality allows us to analyze a problem in terms of its causes, and more importantly, how those causes relate to each other. Once we understand the causal connections, we can clearly explain how the problem happened. And, we can leverage that understanding to develop solutions that prevent the problem from happening again in the future or at least mitigate any negative impacts.
How does it work? Let’s look at the bicycle industry for an example. The Coronavirus disease (COVID-19) has upended the bicycle industry in ways no one would have anticipated. Already on the upswing, especially in the e-bike segment (thanks technology), the COVID-19 pandemic caused market dynamics to change overnight. Entire families were now staying home and staying separate from others. And, while that might work for a few days, it didn’t take long for bicycling to emerge as a safe, healthy way to spend time together. Bike shops were deemed “essential” businesses and therefore allowed to remain open. The combination of new demand with access to supply led to a boom in bike sales. So, what’s the problem?
Well, the new demand has completely overwhelmed capacity all along the chain. As shops sell out various models, they replenish inventories by placing new orders. A mid-sized bike company may supply a few dozen to a few hundred bike shops around the United States and Canada. And, in a normal year, the bike company would have inventory on-hand to fill additional orders. This year, the tide rose everywhere all at once. Bike company inventories quickly depleted. So, the problem now is that bike shops have to tell their customers that, while they can place an order, they have no idea when that order might be filled.
But, can’t the bike company just make more bikes? Sure, but this is where the brittleness of the global bicycle supply chain really starts to become apparent. Bike companies rarely own their own manufacturing facilities. U.S. and Canadian bike companies order from larger manufacturers, mostly based in Asia. The same factory builds bikes for multiple companies, all of whom are now reacting to the fact that they underestimated demand by perhaps 150% in 2020-2021. A bicycle factory normally operates at 85-90% capacity, with the remainder left available for spot orders and demand fluctuations. This left the manufacturers with an approximately 60% capacity deficit.
So, just add capacity. Well, like all fixed capital investments, the lead time to increase capacity is many months – not to mention the fact that the supply chain for the materials and machinery required for expansion is also taxed and even if they could add capacity overnight, how much should they add? Will the increased demand hold as a permanent shift in the demand curve? Or will it fall back to Earth? Since all factories are essentially sold out into 2022, in the near-term demand will persist. But, what about 2023 and beyond? That’s anyone’s guess at this point.
When a supply chain problem presents at one link in the chain, some causes of the problem invariably reside at that link. For instance, the local bike shop is missing out on sales because bikes aren’t available. This is because they didn’t order enough bikes (of a particular model). But, why didn’t they order enough bikes? Because their forecasting model was off. Why was this? Well, COVID-19 tossed everyone’s forecasting model out the window, but still, is there a better way to forecast in the future? And, if the shop’s forecast is off again, is there any sort of action that can be taken to help mitigate this? These are local causes that a shop can understand and control on their own. And preferably, a risk analysis would take place with the goal of anticipating potential problems and their causes ahead of time, so that preventive measures can be put in place before the problem actually happens.
But, the shop shouldn’t stop there. They need to consider the more “global” factors that exist in the chain. Their suppliers cannot fulfill orders in a timely manner. That is a direct cause of why the shop can’t fill their customer’s order, but it’s also one step removed from the shop. Why should the shop care about this? Because they need a global understanding of what is causing the problem, even if it’s outside of their direct control. Just because they can’t control a cause doesn’t mean they can’t guard against it. You can’t fix what you don’t understand.
The shop owner should continue up the chain to find out why their suppliers can’t fill their order. For instance, the bike factory gets paid for complete bikes in boxes. But, their suppliers get paid upon delivery of the components that make up the bike. What happens if the bike is 98% complete but is still missing a saddle and the lead time for saddles is now 180 days? The factory still has bills to pay, but they can’t collect from the bike company until the bike is 100% complete. Will the suppliers wait for their money? Will the bike companies pay for bikes that aren’t complete? The cash and credit risks of a factory in Vietnam may not be something that keeps a bike shop owner in Seattle up at night, but they are intimately related.
No matter where you are in the supply chain, problems are going to be present, and when they are, they are likely to be more complicated than they first appear. A structured problem-solving method helps manage this complexity. You can’t fix what you don’t understand, but if you know the causes and how those causes relate to one another, you’ll be better able to solve the problem and hedge against future risks – no matter where they present in the chain.