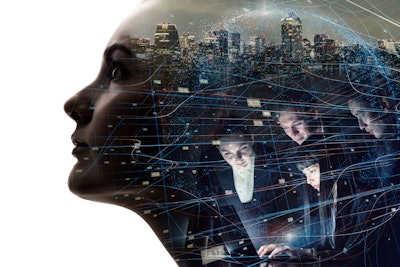
Since the dawn of the Industrial Revolution, manufacturers have relied on linear-type supply chains where materials are delivered to a plant and then assembled and shipped to a customer. With the rise of globalization, manufacturing in lower cost regions became more popular, and the idea of non-linear supply chains began to take hold. In the non-linear supply chain, materials are instead shipped from second-party suppliers to third-party manufacturers where they are assembled and sent down the demand chain through networks for distribution.
Today, something radically different is happening. We have entered a new era; let’s call it the Innovation Economy. The Innovation Economy is characterized by unprecedented competition, with shorter and more exaggerated product life cycles. Supply chains are global and matrixed, and manufacturing can occur anywhere in a network of locations based on ever-changing market demand.
Nowhere is the burden of supporting such a manufacturing paradigm shift greater than in supply chain management. Long considered a cost center, supply chains had been rigidly designed for high speed and low cost. But today, they are viewed as a corporation’s circulatory system, enabling the dizzying pace of product introductions, enhancements and mass customization. Change used to be managed by exception. Now, change is the norm, and adapting to continually changing requirements is a critical success factor. To support change and succeed in the innovation supply chain requires three competencies: enabling agility, running lean and reducing cycle time.
Enabling Agility
Today’s continuous innovation focus is no longer about shipping the same materials to the same plant faster and cheaper. In the Innovation Economy, planning and rescheduling cycles have shortened from weeks and months to hours, and in some cases, mere minutes. When assembly locations, or product line schedules change, set-up times, capital equipment and materials-in-transit must adapt quickly. More rapid product innovations mean constant sourcing. New product designs mean new parts, which also mean new vendors. The winners will identify, onboard and transact faster than the competition.
Running Lean
Historically, “Buy more, it’s cheaper and we’ll use it eventually” was the mantra of the day. The notion of increasing production economies by overproducing no longer exists. Buying, producing and holding materials ties up working capital, and employs unneeded production capacity and warehousing. In many cases, materials also get written off from obsolescence.
In the Innovation Economy, it’s all about planning for salable production quantities, then superseding the products before price erosion occurs. Running a leaner supply chain means no excesses free working capital that used to wait on the shelf, or worse, get reworked or written off because it won’t sell.
Reducing Cycle Times
The Journal of Production Economics claims that "cycle time reduction is the prerequisite of business flexibility." Thriving companies learn to compress the processing time of their internal operations to capture windows of market opportunities before the competition. Most of this time compression battle is played out across the supply chain.
In addition to traditional metrics like the procure-to-pay focus on cash flow, new metrics that measure supply chain adaptiveness are gaining importance. Measuring the ability to support change and adherence to plan change are critical to success. It’s now about sensing and responding to changes in demand as much as it is about days payable outstanding. By taking out excess over production, manufacturers can stop and pivot to the next more profitable build requirements. Thus, driving corporate flexibility and profitability.
Technology-Driven Innovation
Today, supply chain management continues to rely on electronic data interchange (EDI) for collaborating across trading partners. Piloted during the Berlin Airlift in 1948, it was a breakthrough in its day. By today’s requirements, however, it is slow, one directional and error prone. When manufacturers used to plan in extended monthly time increments, EDI worked. Today, scheduling changes are made hours in advance. EDI cannot support the speed of today’s economy. Collaborating by batching and sending is obstructing the speed of innovation, and this requires real-time, agile platforms like business networks.
To innovate effectively and maximize profits with shorter and more extreme lifecycles, industry requires a platform to collaborate across trading partners including contract manufacturers, materials suppliers and logistics intermediaries. But, it is not enough to just transmit data back and forth. Smart systems are needed to interpret this data and alert when needed, to prescribe optimal supply chain decisions.
Making it All Work
Companies continually fine tune their internal systems that improve key business operations like new product introductions, sales and operations planning, and financials. Yet, they spend little time communicating and collaborating with the partners who drive them to share designs, forecasts or cash flow strategies. Some communication may occur with top tiered suppliers, but typically it’s through a patchwork of faxes, EDI and emails, and long tail suppliers rarely receive any outreach. But, networks are changing this.
Supplier hubs are typically just one-to-many EDI networks. Newly designed networks, on the other hand, connect internal systems with entire networks of suppliers, and each supplier can have its own buyer and seller community within that same network. This networked connectivity brings the supplier community into planning and transactional systems, enabling companies to drive better control, visibility and supply chain responsiveness and take out days of inventory and millions of dollars of working capital from their supply chain.
Today, there are two key operational categories within supply chains that require a digital transformation. The first focuses on compressing sourcing capabilities. The second concentrates on transacting collaboratively and digitally with suppliers.
Materials Sourcing
As manufacturers increase their rate of innovation, category managers have a growing burden to keep up. This requires accelerating sourcing functions that have traditionally been paper-based and understaffed. The need is growing to eliminate the reluctance to conduct sourcing events, and increase performance in this strategically important sourcing role. Until now, category managers have struggled through events with incomplete product information, component history and sourcing requirements. Digital solutions are changing this.
Cloud-based applications for direct spend sourcing, for instance, leverage existing information in product and lifecycle management systems to automate the entire process. And the best make it possible to:
- Upload multi-tiered BOMs from ERP systems
- Identify new potential vendors
- Monitor vendor risk potential based on public records and internal performance history
- Develop RFP questionnaires from an ongoing library of selection criteria
- Broadcast RFPs electronically to selected vendors
- Guide vendor selection based on supplier optimization tools
- Negotiate terms and conditions within the syste.
- Formalize and electronically store contracts
- Upload new BOMs into transaction systems
With the right solutions in place, companies can:
- Increase business agility by responding to business sourcing requirements faster.
- Reduce the cycle time required to run sourcing events, providing faster response for new product development and transacting with new suppliers.
- Run leaner by automating cumbersome and labor-intensive sourcing-to-contacting activities.
- Take out hard dollar cost from better informed and more frequent sourcing events.
- Mitigate risk in supplier selection.
Supply Chain Collaboration
At one point, the manufacturing plant was across the street and planners could walk over, and work on schedule changes directly with the plant manager. Today, the contracted plants that a growing number of company’s use are 13 time zones away, and require rigid scheduling along with local support to manage language and cultural barriers. Leveraging business networks and the cloud-based applications delivered on them, companies can collaborate across global supply chains anywhere, anytime using any device and, among other things:
- Forecast collaboratively with entire supply base and receive commitments back as schedules change.
- Manage complex multi-tiered supplier orders.
- Synchronize inventory and backflush information with contract manufacturers and other remote locations.
- Monitor and exchange product quality information.
- Score card supplier performance.
- Receive, audit and process supplier invoices.
- Track and trace order status.
- Enable supplier managed inventory to monitor and initiate replenishment orders.
Today’s supply chains are more global and complex than ever. The key to successfully managing them lies in collaboration. And companies that embrace this notion can deliver significant results The supply chain drives performance and enables businesses to run leaner and more efficiently. Specifically, this collaboration empowers companies to:
- Gain control of inventory and manufacturing operations of outsourced providers to make unplanned changes to schedules.
- Reduce working capital and excess inventory in the supply chain.
- Eliminate obsolete materials that were not easily visible.
- Increase business agility by responding to business sourcing requirements faster.
- Reduce cycle time required to run sourcing events, providing faster response for new product development and transacting with new suppliers.
- Reduce staffing time required to monitor outsourced operations.
A New Way Forward
The manufacturing world has undergone massive transformation over the last several decades, and another big paradigm shift is on the horizon. With the help of digital technologies, manufacturing will move from build-for-scale to build-for-more frequent, extreme and shorter product lifecycles. In doing so, it will aid in transforming companies into leaner, meaner and more agile machines that fuel innovation across the economy.