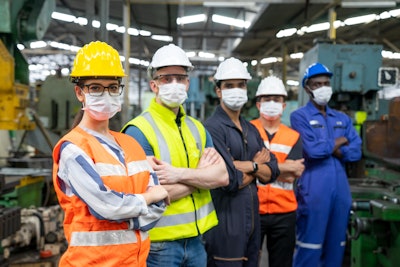
The Coronavirus disease (COVID-19) put millions of people out of work. But, the jobs that emerge on the other side of the pandemic will differ from those lost. Automation, robotics and artificial intelligence (AI) are filling administrative roles, freeing up employees to focus on more complex and meaningful work.
Although there are always concerns that digital transformation will replace humans, the current shift toward automation offers many benefits for the workforce. Emerging technologies create more jobs than they eliminate, reduce the need for humans to perform menial tasks and improve overall business outcomes.
But, organizations need to consider the widening skills gap caused by these new types of work. If you fail to educate your employees on how to work alongside this technology, you risk a costly mismatch between the skills your employees have and the skills your business requires.
From the 1760 Industrial Revolution to Industry 4.0
The digitalization of work is causing a fourth Industrial Revolution known as “Industry 4.0.” It’s valuable to look to our past to gain perspective on how technology has altered work over the ages:
● The introduction of water and steam power ushered in the First Industrial Revolution. Machine-powered production, as opposed to manual production, fueled unprecedented growth.
● The Second Industrial Revolution, known as the Technological Revolution, resulted from the introduction of electricity. Electric-powered machinery enabled mass production and the movement of people and ideas.
● Electronic computing and information technology triggered the Digital Revolution. These technologies enabled greater connectedness, driving innovation that improved global quality of life and organizational productivity.
Industry 4.0 builds on the Digital Revolution by further integrating technology into all aspects of life. Automation, robotics and AI are creating a new division of labor shared between humans, machines and algorithms. The pandemic fueled technology adoption and simply accelerated changes already in motion.
Workers feel threatened by automation
Similar to what occurred in previous “revolutions,” your workers likely fear the effects of new technologies. In fact, one study found 37% of all workers worry automation will render them useless.
It's true that automation will change the job landscape. Consider this: In 1850, agricultural jobs made up 60% of total employment in the United States, but declined to less than 5% by 1970. Manufacturing fell from 26% of total U.S. employment in 1960 to below 10% today.
But, there’s a silver lining. Despite the reduction of farming and manufacturing jobs, new jobs arose that workers could never have foreseen. Each year, about 0.56% of new jobs in the United States are in new occupations. For context, this means just under a quarter of the workforce is employed in a role that didn’t exist in 1980.
The bottom line: New technologies spur the creation of more jobs than they destroy — automation included. But, you need to ensure your workforce is prepared for this transition.
Skills the workforce and workplace need
Industry 4.0 promises benefits like higher productivity, GDP growth and improved quality of life. Yet by 2025, 85 million jobs may be displaced and replaced by 97 million new ones. By 2030, it's estimated more than one in 16 workers will need a different occupation.
Automation, robotics and AI eliminate routine manual jobs that involve administrative "spreadsheet" duties. As your organization adopts these technologies across business units, you’ll see a higher demand for non-routine analytics jobs that require skills like critical thinking and technical familiarity.
Employee responsibilities will focus on managing people, applying expertise and interacting with stakeholders. For example, customer service representatives will spend less time inputting data and providing shipping updates and more time building customer relationships and managing processes.
The skills your employees will need to develop include:
● Both basic and advanced technology skills to work alongside and govern technologies. This is the area in which we face the largest skills gap and includes roles like data analysts and software engineers.
● Soft skills like empathy, advanced communication, entrepreneurship, creativity, initiative-taking and leadership. For example, even as machines are increasingly used in production lines, first-line supervisors need to problem-solve bottlenecks and ensure operations are smooth.
● Physical labor in customer-service roles is on the rise. But, other unskilled manual roles are at high risk of automation. For example, robotics can operate vehicles and package products but aren't able to care for patients.
One skill worth highlighting is the ability to generate software and digital solutions without coding. There has been explosive interest in low and no-code technologies that assist citizen developers in delivering company-specific business applications, like automating tasks. Using such technology is a skill in itself, and developing that skill within your company will increase innovation and efficiency.
Overcoming the skills gap through upskilling
Though it's predicted Industry 4.0 will deliver net positive job gains, the current skills gap threatens that growth. Without properly skilled employees, your organization may face reduced productivity, increased workload across staff, employee dissatisfaction, lost business and stifled innovation.
Both public and private intervention is needed to help the workforce adjust.
Additionally, individual companies are taking it upon themselves to retrain their workforces. While upskilling your workers will take time and funds, it’s worth the investment. The price of turnover and acquisition per new hire is about 30% of an employee's annual salary, with the cost increasing as seniority level goes up. Layoffs can also reduce company morale and eliminate valuable historical company knowledge. You can reskill workers via internal resources or partner with an education provider.
It’s also important to consider how to promote equality as we overcome the skills gap. If current employment trends continue, only 42% of these new jobs gained by automation will go to women. Additionally, the majority of jobs lost will be in low-wage positions, while the jobs created will be in high-wage positions. This potential outcome threatens to exacerbate existing inequalities for people of color, low-income individuals and the less educated.
Fortunately, there is still time to shape Industry 4.0's impact. Your upskilling program should be intentional about including employees from different backgrounds if we aim to uplift society as a whole.
Digital transformation demands human collaboration
As past workforce revolutions have shown, technological improvements offer many benefits to workers, the workplace and humanity. But, we can’t ignore the fact that the current skills gap and lack of awareness threatens the full realization of these benefits. Our organizations need to educate and reskill workers on how to co-exist with emerging technologies. Remember, automation is only part of the transformation — technology alone is not the end all, be all. Your business still needs skilled human leaders and employees to drive innovation and growth.