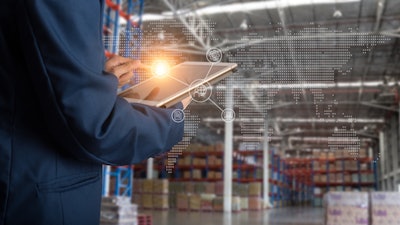
The food logistics industry faces numerous obstacles. With changing government regulations and complex supply chains, it can be difficult for businesses to navigate the ever-evolving landscape of food logistics. There are several areas of expertise that must be taken into account when running a successful operation in this space, including regulatory compliance, financial forecasting and risk mitigation, customer demands and preferences assessment, resource optimization, technology integration, infrastructure development and maintenance.
Each of the aforementioned tasks require careful planning and execution to ensure smooth operations while also keeping track of costs associated with delivering the end-product on time. Not to forget the unforeseen changes that could cause unexpected delays or increased costs. It’s crucial for businesses operating in this sector to stay up to date with the latest trends in order to effectively plan for any eventualities that may arise, and this is where delivery technology can help.
How delivery technology can mitigate and relieve food logistics disruption
- Strategic planning
Understanding customer needs and optimizing delivery routes is key to successful food logistics. To start, assess historical patterns of past deliveries and service levels. Long-term recurring plans should be applicable for periods of 1-2 quarters.
Previously, route planning was done with pen and paper, but now computers can quickly assign new staff to existing regular routes. This technology can help you test your recurring route plans, and optimize the number of deliveries in order to meet customer service goals while reducing mileage and streamlining the whole process.
2. Real-time visibility and monitoring
Real-time visibility and monitoring are vital for any successful delivery operation, allowing you to verify that your deliveries are on track. You can monitor driver location and ETA information as well as average stop times, dwell times, fuel usage, and onboard temperatures. This is especially important for food deliveries, where it is crucial to keep the food at the proper temperature.
Order status can be viewed by the sales team too, so they can inform customers of any changes in their orders quickly. As unforeseen events occur that may delay delivery, a plan B is essential to have in place and automatic notifications should be sent to keep customers updated. Although this may cause initial disappointment, taking this extra step will foster a sense of trust and reliability with customers.
3. Delivery execution
Delivery execution is one of the most critical steps in the food delivery process. With modern technology, such as GS1 barcodes and delivery capture devices, wholesale food delivery is faster than ever before.
Benefits of this technology include tracking goods for food safety, capturing proof of delivery, contactless delivery, electronic documentation, custom workflow capture, return capture and item substitution for customer satisfaction, and exception capture to solve problems in real time. All of these features help guarantee that the customer receives their order safely and quickly.
4. Analytics and reporting
Delivery technology is revolutionizing the data collection and analysis process for food logistics, enabling businesses to make informed decisions with insights from powerful reports. It can generate reports about on-time vs. delayed deliveries, popular items delivered, inventory age, miles driven vs. planned miles, driver performance and spoilage/returns.
This data will help pinpoint customer preferences, manage food waste, boost fuel efficiency, increase driver productivity and improve quality control. Plus, these reporting tools also help to facilitate recalls in case of a food issue, letting businesses swiftly remove any affected items from circulation while avoiding customer complaints.
There’s a lot that goes into traceability. Here’s what has to happen:
- Record product lot numbers every time products arrive at the warehouse.
- Maintain the traceability of raw materials as appropriate.
- Manage the movement of every product effectively during delivery.
- Identify the area of every product lot quickly.
Food is what connects the world. It invites us all to experience other cultures and join in to learn what makes us unique. That’s why it’s so important this industry works like a well-oiled machine, and that can only happen through adapting to current situations with technology. As tech rapidly evolves, we must change with it.