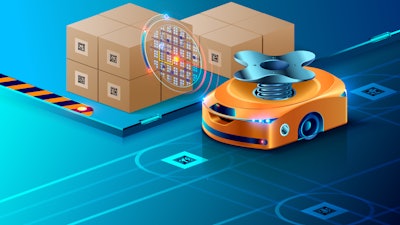
Enterprise logistics are under more pressure than ever — the labor crunch, fierce competition, next day (even next hour) delivery all challenging supply chain efficiency and resiliency. Companies are expected to ship goods on time without fail, requiring them have a firm grasp on what’s happening inside their facilities at every moment. As a result, companies are looking to digital transformation initiatives to solve their supply chain challenges by using the latest technologies to reduce unplanned downtime, improve throughput and productivity and increase visibility into day-to-day operations.
No technology or process change can by themselves be expected to solve these challenges. But combining technologies under the broad term “digital” is proving to deliver positive results. Still, with so many moving parts, companies must use a strategic, targeted approach to realize the benefits of digitization.
Rather than “following the leader,” apply digital solutions to tackle the most meaningful challenges unique to your business.
As consumers demand more and faster, it’s tempting to jump right into operationalizing systems to meet rapid delivery demands. However, the first step for most companies should be to perform an assessment of your facilities and operations to define desired business outcomes. The logistics space, especially for grocers and other foodservice providers, is crowded by competitors trying to deliver goods to consumers in record time. Determine which areas are most critical to address for your business, then identify the right solution for your needs. For example, one company might have issues with unplanned downtime and need improvements in predictive maintenance, while another may have bottlenecks in their operations that limit their ability to ship products at certain times. Problems (and solutions) are myriad, so an initial assessment will ensure your investments are effective.
In general, most distribution facilities should start by addressing one of these two areas:
- Modernizing operational networks and IT systems to improve cybersecurity and serve as the foundation for digital investments.
- Implementing advanced analytics to optimize operations with efficient inventory management or predictive maintenance.
Once you’ve identified what you’d like to digitize, resist the urge to do everything at once. Instead, start small and broaden the focus as you achieve success.
Companies typically pursue one of two pathways for digitization:
- Apply digital transformation narrowly at first to address specific, high-value key performance indicators (KPIs) like grocery pickup and delivery time. And then apply it more broadly across prioritized aspects of operations over time.
- “Go big” with next-generation facilities — think of, for example, retailers building distribution centers for online grocery ordering where they don’t otherwise have a brick-and-mortar presence.
Start with targeted business outcomes that are high-value and quick to implement, then focus on longer implementation opportunities as those begin to show results.
Know when to lean on technology or when a problem might be better solved with human touch.
Integral components of digital transformation have been around for years — artificial intelligence, machine learning, the cloud — just to name a few. What’s new is using the connectivity and intelligence of these technologies to allow smarter optimization decisions, whether those decisions are made by humans, software, or a combination of both.
Many organizations tend to jump to shiny, new technologies before assessing or fully understanding internal user requirements and need for collaboration among departments, vendors and suppliers. Understanding organizational change management and having a plan of area critical for successfully implementing a digitization initiative. Avoid the trap of kaleidoscopic analytic applications that require perpetual clicking to get actionable information (if any all). Technology must be an enabler and analytic applications must be intelligent enough to facilitate user tasks. So first prioritize user experience requirements over technology.
When you connect your operational technologies with your company’s information technology (IT) and network infrastructure, you begin to connect the Industrial Internet of Things (IIoT) dots in the facility and facilitate a more comprehensive view of operations and maintenance — a view that drives results. The advent of Industry 4.0 technological advancements (big data, the cloud, IIoT, digital sensors, etc.), makes connecting the right data with the right intelligence easier than ever before.
While consumer demands are certainly a leading source of pressure points, food shortages and even recalls cause their own disruptions. These disruptions present yet another case for moving toward digitized logistics in a planned, purposeful way. Whether relying on traceability to track a tainted product or real-time inventory data to move product to where it’s most needed, the key to transformation is thoughtfully considering the solutions that have the biggest impact on your business.
With the right digital transformation approach, companies can expect to see annual productivity improvements of more than 5% in inventory, lead time, data collection, quality and more.