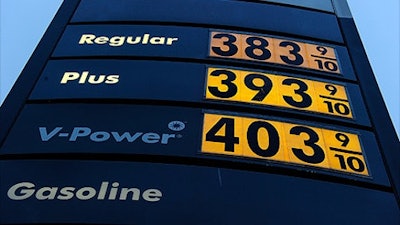
Rising fuel prices have been a major burden on companies struggling with a turbulent supply chain. As supply chain woes continue and gas prices remain at record highs around the country, many businesses are looking for ways to cut down on fuel usage. Increased gas prices lead to a domino effect of rising operational costs. However, with the proper tools and planning, businesses can navigate our ongoing emergence from the pandemic and prepare for the future.
On the road
It goes without saying that sensible vehicle operation is a significant factor in lowering fuel costs. For example, holding a load until a truck is full minimizes the number of trips and saves fuel costs. Empty or partially empty trucks needlessly wastes fuel. With proper planning and logistics management, businesses can save money and cut down on emissions significantly. If you do have to drive with an uneven load, it is important to put heavy items towards the front of the trailer to decrease resistance on your route.
Cutting down on idle time for drivers, such as creating a system where the idle shuts off after a certain amount of time, is another proven method to save on fuel through vehicle operations. Trucks burn up to 1 gallon of gas per hour sitting idle. By using route planning tools that avoid or minimize the simple act of making a left turn, major carriers save thousands of gallons of fuel and reduce thousands of pounds of carbon emissions each year — with the added bonus that right-hand turns are statistically much safer.
Though the optimal speed for fuel efficiency (and safety) is between 63-65 miles per hour, it can be difficult to convince drivers to stay within that range. Of course, this is because it impacts their driving time. Incentivizing drivers can save on fuel and increase safety. Establishing a fuel bonus program for drivers that gives a bonus at the end of each quarter can create a culture built around lowering fuel costs, and thus, the carbon footprint of the company as a whole. Avoiding congested areas with traffic that burn more fuel is another key component of a cost-effective supply chain. The length of the route and the time spent driving in it are key in calculating fuel costs. Traffic conditions and detours all will have an impact on transportation costs. Keeping track of this data is necessary when costs are high.
Every ounce counts
Performing an analysis of the efficiency of your shipping materials is among many key steps toward reducing fuel costs. Traditional wood pallets absorb moisture from their surrounding environment, adding to their weight. On average, wooden pallets are 35% heavier than plastic pallets, and that weight significantly increases fuel costs during shipping. If a plastic pallet is 25 pounds lighter than its wooden counterpart, for every 1,000 pounds saved, you can cut down on fuel economy by 1-2%. On a large fleet, that adds up rather quickly. Furthermore, plastic pallets are more durable than wood pallets and less likely to break or compromise cargo, which can also lead to supply chain delays. In addition, some hauls may not require pallets at all but can be loaded effectively with slip sheeting. Similarly, packaging materials that are wrapped vs. boxed reduce trailer weight. And, people add pounds to truckloads, too. Statistically, the national waistline has expanded over the past few decades. Incentivizing drivers and all employees to maintain a healthy weight can lead to numerous benefits, including lower healthcare costs, happier colleagues — and yes, even lower fuel costs.
Close the loop
Integrating supply chain activities with a closed loop ecosystem is another way to lower fuel costs and the environmental footprint. For example, manufacturers, retailers and the entire supply chain can benefit from a closed-loop model in which pallets are inspected by retailers after receiving and then sent back into circulation for re-use, rather than being shipped to a central pallet depot. This eliminates two legs from the transportation journey, saving time and effort as well as reducing fuel consumption.
Avoid delays
By being more selective and avoiding shippers that can cause delays and layovers, fleets can save time and money for businesses feeling the effects of complex supply chain issues. Routine diagnostics must be done to determine optimal routes and minimize unnecessary trips. Trucks used in long-haul routes need regular maintenance to prevent unexpected problems that can cause delays.
The long haul
Even when gas prices return to so-called normal levels, the proactive tactics above will save time and cut costs for your business in the proverbial long haul. The key components to focus on are increasing efficiency, reducing waste, minimizing risks and spending smarter. Sustainable and lightweight materials often last longer, minimize errors that can cause delays in shipping and reduce harmful carbon emissions. Finding ways to consolidate trips, eliminate deadhead miles and partner with efficient shippers will continue to pay dividends. Though the challenges of supply chain disruptions and inflation serve as a stumbling block now, finding ways to work around them will provide a blueprint for businesses to follow in the future.