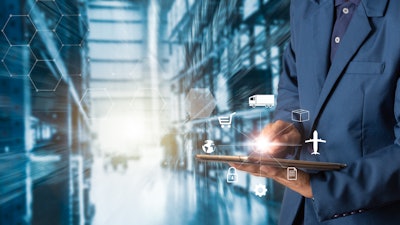
Elevated e-commerce sales are here to stay. Even in the face of consumers’ affinity for in-person shopping and problematic macro-economic trends, online sales remain robust when compared with pre-pandemic levels. In its report on second quarter 2022 e-commerce sales, the Department of Commerce estimated that online purchases comprised nearly 14% of retail sales, or $252.1 billion, a 7.4% increase from the same period last year.
This can be seen in the dramatic developments shaping the market for warehouse space. In research findings announced in June 2021, CBRE estimated that the United States will need 330 million square feet of additional distribution space by 2025 to meet robust e-commerce demand. CRBE also found that vacancy rates for industrial space remained at a record low and growth in rents remained at a record high throughout the first half of 2022, a strong indication that e-commerce demand continues to challenge existing materials handling operations.
All of this points to a new reality. Warehouses are larger, and yet retailers are still struggling to find room that keeps up with the throughput of today’s online shopping trends. To fully optimize space and efficiently process order throughput, retailers are increasingly adopting automated storage and retrieval systems (AS/RS).
The use of shuttles in AS/RS began to accelerate before the pandemic.
Of course, AS/RS are not new. Automated pallet cranes emerged in the mid-1970s to replace manual cranes operated from cabs that moved with the lifting surface. Miniload cranes followed, and as their name suggests, made it possible to move loads decanted from pallets into cartons, trays and totes.
Both remain in use today and can be very effective when storage levels are relatively static and required throughput levels are low. However, the acceleration of e-commerce during the pandemic radically increased the volume of orders warehouses must process and led to the rapid expansion of the AS/RS market.
Within this market, shuttle systems are more prominent than ever because of attributes like speed, scalability, ease of use and labor savings. Even before the pandemic though, many saw them as the future of AS/RS because of their applicability to e-commerce.
Shuttles are more efficient than other systems for e-commerce applications and are ideally suited for the goods-to-person (GtP) environments needed to achieve the higher throughput and item picking e-commerce demands and high variability of SKUs increasingly involved. Notably, shuttles also solve what for generations was one of the most time-consuming and labor-intensive aspects of item picking: workers typically spent 70% of their time just walking to find and pick items.
This reality and the repetitive nature of other picking-related tasks always challenged distribution centers (DCs) when attracting, retaining and training employees. Today, with many warehouses experiencing employee churn of up to 40% annually, those same challenges are prescient.
Even before the pandemic, this led to greater demand for shuttle systems that are scalable, have a smaller footprint, address labor challenges and empower organizations to increase the storage density of their existing facilities. A report issued by ARC Advisory Group noted many of these attributes align with today’s fulfillment needs and e-commerce.
However, even though it’s unquestionable that shuttle systems have a place in many e-commerce distribution centers, it’s imperative that organizations examine shuttle systems not just for their capabilities, but more importantly, for what they specifically need to be successful.
Not all shuttle AS/RS are the same.
There are many kinds and brands of shuttle AS/RS on the market today – all of which should be vetted considering each DC’s unique needs. High-performance is not necessarily the right choice for every application.
● One-dimensional shuttles. The first AS/RS to incorporate shuttles are often described as one-dimensional. While far more efficient than the cranes they replaced because it decoupled the inserter and/or extractor and in that way gained the ability to pick in more than one aisle, one-dimensional shuttles cannot leave the level they are assigned to and can only travel back and forth in the storage structure. As a result, they often include inactive shuttles on levels with less popular SKUs and cannot adjust to rapidly-changing order profiles or volume. They can; however, be ideal for organizations that have a limited number of SKUs and highly repetitive orders, such as in kitting or manufacturing applications.
Vanderlande
● Two-dimension shuttles. These shuttles can move forward, backward and side-to-side across aisles in the storage structure – and as a rule are much more productive than one-dimensional shuttle systems. Two-dimensional shuttles can also be directed by software to lifts to be carried up or down to levels where additional picking capacity is required. For these reasons, they are ideal in environments that require GtP picking, but have lower throughput needs.
Vanderlande
● Three-dimension shuttles. Able to move forwards and backwards, from side-to-side, and up and down within the storage structure under their own power, three-dimension shuttles do not require the use of lifts like their two-dimension counterparts. The absence of lifts saves costs, but such systems require the shuttle to deliver its load directly to the picking workstation and/or alternatively deliver returns back to storage. While ideal for lower-throughput applications in GtP environments, they are therefore prone to traffic jams in high-volume operations as they wait in line to drop off or pick up product.
Vanderlande
● Roaming shuttles. The most advanced systems to date, these shuttles are highly integrated with lifts, buffering conveyors, and software that sequences picking operations for maximum velocity and flexibility. The shuttle closest to the item is sent to retrieve its container and deposit it on a lift designed for picks, with a conveyor then transferring it to the GtP workstation. Separate lifts then pick up containers for their return to storage, while advanced vision software identifies the item and number of items needed for each order at the workstation. These capabilities make roaming shuttles much faster and ideal for environments where inventory changes often and throughput rates are necessarily high. They also virtually eliminate the pick errors that can impact customer satisfaction, but do require investment in a highly-integrated system.
Vanderlande
AS/RS applications of shuttles will continue to increase as e-commerce volumes grow. Every DC ultimately must determine which mix of capabilities they need and what kind of shuttle system addresses them – all while considering existing perimeters like the available storage structure, current needs, budgetary constraints and future growth.