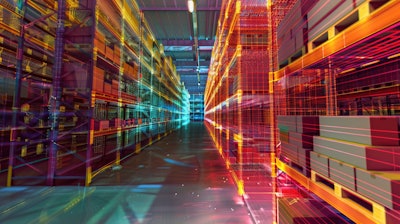
Industrial facilities, particularly warehouses and manufacturing plants, are becoming more complex, more automated and more dynamic. With that complexity comes heightened risk, such as collisions involving forklifts, autonomous guided vehicles (AGVs) and human workers, which remain a persistent safety challenge. Despite the proliferation of automated safety systems, the statistics tell a stark story. Each year, around 100,000 forklift accidents occur in the United States, according to OSHA. Roughly 35,000 of those result in serious injury, and the average cost per incident is $180,000. Even more alarming is an estimated 90% of all forklifts will be involved in an accident at some point during their operational life. That level of risk demands a reevaluation of how we sense and respond to hazards in industrial environments.
Traditional solutions that are primarily built around 2D lidar, radar, or camera-based safety systems can no longer keep up with the spatial complexity and speed of today’s operations. When you consider the full scope of what a modern warehouse contains, including tight aisles, hanging chains, pallet stacks, mixed-use zones with both people and machines, it becomes clear that a 2D understanding of space is insufficient. That’s where 3D lidar comes in.
Understanding the limits of 2D safety systems
Many industrial safety systems rely on legacy 2D planar lidar sensors for basic collision-avoidance using a feature called zone monitoring, which consists of safety “fields” set up to detect objects or motion within a pre-defined space. These systems can detect whether something enters a zone, triggering a stop or alarm. However, 2D monitoring is limited with a narrow field of view, lower resolution, and difficulty dealing with vertical complexity. 2D sensors often miss obstacles like a low-hanging chain, a pallet lying on the floor or an overhead beam that are outside their scanning plane.
Equally problematic is their inability to distinguish between relevant and irrelevant objects. False alarms are common and can lead to downtime, while missed detections can result in injuries or damage. Environmental conditions like dust, fog or smoke further reduce their effectiveness. As warehouse operations become faster, denser and more automated, the need for a more robust solution is clear.
Elevating safety through 3D spatial awareness
The next evolution in industrial safety and automation is 3D digital lidar that brings real-time spatial awareness and intelligent zone monitoring to the warehouse floor. Unlike traditional 2D systems, 3D lidar captures the full volume of a space, not just a flat plane. This makes it possible to monitor vertical clearances, detect hanging objects and differentiate between objects such as a pedestrian’s foot and a rolling box.
At the core of this innovation is the concept of customizable 3D zone monitoring. Instead of relying solely on external computing, modern 3D lidar systems now embed this functionality directly on the sensor itself. This not only reduces latency in detection and response but also simplifies system integration, allowing facilities to deploy intelligent safety zones more quickly and cost-effectively.
Rethinking zone monitoring for a 3D world
Smart zone monitoring enables critical safety actions such as warnings, deceleration or emergency stops when objects enter designated zones. Advanced lidar systems can monitor over a dozen zones in real-time, adapting dynamically based on vehicle speed, steering angle, or other inputs. This adaptability is essential for environments where paths and priorities constantly shift.
Crucially, modern 3D lidar technology supports parallel data processing—delivering both actionable alerts to low-power safety systems and rich point cloud data to higher-powered systems for analytics and perception. This dual-layered approach helps reduce false positives, especially in dusty or variable lighting conditions, without sacrificing awareness or control.
3D lidar also increases operational efficiency. A high-resolution 3D lidar with wide field-of-view can cover the same area that would otherwise require multiple cameras or 2D sensors, thereby simplifying the autonomy stack. The result is better performance with fewer components and less integration complexity, especially valuable in space-constrained warehouse environments.
Practical use cases in warehouse automation
In practice, 3D zone monitoring can be transformational across several smart warehouse applications:
● Forklift collision avoidance: 3D lidar can detect pedestrians, racking, and other obstructions in all directions, including overhead or below the fork level, helping prevent high-impact collisions.
● AGV and AMR safety: By embedding dynamic 3D zones into autonomous mobile robots, facilities can prevent collisions with people or infrastructure even in high-traffic or fast-changing areas.
● Loading dock management: Monitoring entry and exit zones for unexpected obstacles or motion can minimize risk during one of the most dangerous phases of warehouse operation
● Conveyor systems: 3D sensors can detect jams or foreign objects on conveyors, preventing bottlenecks and improving throughput.
Toward predictive safety and smarter warehousing
Looking ahead, 3D digital lidar is playing an increasingly critical role in industrial environments not just for collision prevention, but for long-term operational efficiency and intelligence. The high-resolution spatial data captured by these sensors can be leveraged beyond real-time alerts to support ongoing facility management. Over time, lidar can help identify subtle changes in layout, track recurring patterns in near-miss zones and monitor for debris or material buildup that may pose safety risks. This kind of persistent environmental awareness opens the door to more proactive safety strategies and predictive maintenance planning.
In addition, 3D lidar is a cornerstone for enabling Simultaneous Localization and Mapping (SLAM), which is essential for autonomous systems operating in complex, ever-changing spaces. SLAM powered by dense, accurate point clouds allows automated guided vehicles and mobile robots to localize with greater precision and resilience. This enhances not only navigation, but also the safety, efficiency and adaptability of smart warehouse operations.
As warehouses grow smarter and more autonomous, safety must evolve in parallel. 3D digital lidar offers a clear path forward, one where machines and humans can safely coexist, guided by real-time awareness and intelligent zone-based protection.
Collision avoidance is no longer just about preventing accidents—it's about building smarter systems that understand and respond to their environment. In that vision of the future, 3D lidar isn't just a sensor, it's a cornerstone of the smart warehouse.