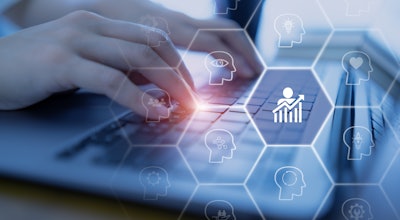
A trio of pandemic related challenges over the past several years—global supply chain bottlenecks, ongoing labor shortages and rising inflation—are forcing manufacturers to optimize operations and find ways to do more with less. A recent National Association of Manufacturers (NAM) survey reveals that 45% of manufacturers say that worker shortages have left them unable to take on new business and have led to lost revenue opportunities.
Fortunately, emerging technologies such as robotic process automation (RPA), artificial intelligence (AI), machine learning (ML), cloud networking and the Internet of Things (IoT) are allowing manufacturers to push forward and fuel growth despite these challenges. In fact, 41% of manufacturers plan to invest in IoT technology over the next two years as a way to automate operations and do more with less, according to the NAM survey.
However, a lack of expertise in these emerging technologies is slowing adoption—severely hampering manufacturers’ digital transformation journeys. In order to adapt to a new normal and continue to fuel growth, manufacturers will need to focus on hiring best-in-class employees that have the technical expertise in emerging technologies that help improve resilience and performance.
A New Focus on Upskilling and Reskilling
According to the PwC Digital Trends in Supply Chain Survey 2022, increasing efficiency and reducing costs are manufacturers’ major priorities—outpacing digitization, automation and upskilling by wide margins. This suggests that many companies are focusing more on the bottom line in the short term but have yet to make some of these potentially transformative actions a bigger focus.
As manufacturers implement new technologies to help mitigate the impact of worker shortages, they need to take on a larger role in giving employees the expertise they need to be more agile and work with these new tools to navigate bottlenecks. Reskilling will become absolutely necessary—including increased digital skills and a renewed emphasis on continuous training.
Upskilling and training will allow manufacturers to adopt more Industry 4.0 technologies—including machine-learning robots and co-bots, smart conveyors and smart warehouses with autonomous or semi-autonomous materials movement. We could also see more applications in virtual reality (VR), augmented reality (AR) and other digital technologies.
Blockchain applications in manufacturing, in particular, are expected to explode, with nearly one-quarter of respondents (22.6%) in the PwC survey saying they plan to invest between $1 million and $5 million in the new technology over the next two years. Another 21% plan to invest similarly in cloud-based, common-data platforms.
Making Upskilling a Priority is Critical
Advanced automation technologies are allowing manufacturers to overcome a host of pandemic-related issues that have hampered growth over the past several years. However, a focus on short-term efficiencies rather than long-term optimizations is hurting their ability to build long-lasting solutions that can continue to deliver value and growth. Manufacturers need to work with their employees to gain the knowledge and expertise needed to implement these new solutions. Upskilling and reskilling will become key to optimizing their use of these technologies—but only if they make on-going training and skills development a priority for their organization.