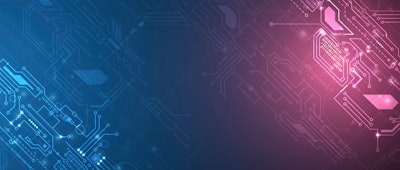
Over the past year or so, we’ve experienced our fair share of supply chain disruptions, from the ongoing semiconductor shortages to the airline failures this past holiday season. And, while these supply chain snarls appear to be loosening, they still serve as warning signs for any organization that deals in logistics or manages a supply chain.
Here's what the warning signs might look like and how they’re often tied to a cascading tech failure waiting to happen.
You’re Using Multiple Siloed Platforms
Organizations grow. They adopt new tools to support their growth. So they grow some more. Then they adopt even more platforms (in 2021, organizations used 110 SaaS applications on average). Soon, these organizations are balancing dozens of different systems, and none of them integrate with each other. Or at least, none of the platforms seamlessly share real-time data with one another.
If this sounds like you, I can guess what you did next. You likely developed some workarounds. Maybe you even bit the bullet and started manually entering purchase orders into your vendor management system. But over time, you realized these manual workarounds weren’t just inefficient; they were also leading to more errors and hurting your bottom line.
If your various platforms aren’t integrated and sharing real-time data, that means other members of your team aren’t making decisions with the most up-to-date information. And in logistics, the difference between real-time data and data that’s, say, 20 minutes old is massive.
For instance, maybe you receive, and accept, a purchase order for your exhaust systems. It’s a bulk order – 250, let’s say. Your third-party inventory system says you have enough inventory to manufacture the exhaust systems. But that’s only because the system’s data hasn’t yet updated. In reality, you’re short about 1,000 gaskets you need to fulfill the order. The siloed data, in this case, likely delays the expected delivery of the order – potentially damaging your relationship with the vendor.
Your Legacy ERP System Isn't Supported by the Provider
The symptoms of an outdated enterprise resource planning (ERP) system are often similar to the pain points you may experience from siloed platforms. For example, let’s say you adopted an ERP system as your organization began to scale. You keep the system updated and accept bug fixes. But lately, you haven’t been receiving any updates because the system is so old.
You hire developers to create patchwork solutions that keep your system relatively operational. But more and more cracks are beginning to form in the system. Soon, you’re not even receiving bug fixes. The system isn’t supported by the provider anymore. You’re on your own. The developers are keeping the system alive, but there are operational inefficiencies littered throughout. And the resulting lack of support leads to cybersecurity vulnerabilities that are exposed in a data breach.
This forces you to manage the fallout of this security issue while maintaining your supply chain, whether that's preserving relationships with vendors or ensuring deliveries go out on time. And you still have to deal with the outdated system that landed you here in the first place.
You Don’t Have a Comprehensive Employee Training Program
At first glance, this may not seem connected to the technology powering your supply chain. But your organization’s approach, and openness, to technology adoption lays the foundation for how innovative and scalable your supply chain can be.
One of the greatest hurdles to digital transformation is the mentality of “we’ve always done it this way.” This philosophy seeps into every part of an organization, and it often leads to inadequate training programs for employees, which can have a devastating impact on your operations.
Consider this hypothetical: you work in logistics. Your company adopted an ERP system about five years ago, and you have legacy systems that work alongside it. Longer-tenured members of your warehousing team know how these systems interact and how to reconcile the disparate data sets from the various platforms. They know, for instance, how to manually cross-reference the data from inventory management features in your ERP with the purchase orders from your third-party sales platform. This point of manual input is the difference between your company keeping products moving and delaying orders because you lack the necessary inventory.
Newer employees, conversely, know that if they have any issues, they should go to the senior members of the team. Eventually, though, these senior members leave your organization, taking their institutional knowledge with them. Without a comprehensive training program that acclimates employees to your technology systems, staff turnover doesn’t just change the makeup of your company; it also jeopardizes team-wide workflows and best practices.
It Doesn’t Take Much to Set Off a (Supply) Chain Reaction
A running theme in this article, and in logistics generally, is that even the tiniest of breakdowns can create a large chain reaction. An outdated airline reservation system, for instance, can adversely impact every system it connects with, from crew scheduling to maintenance to ground operations.
Now, this isn’t to say using multiple systems is inherently bad. Maybe, to run your company, you need third-party solutions to fill gaps in your ERP software. But these add-ons can't come at the expense of end-to-end visibility. Once you lose track of one part of your supply chain, you risk the whole chain collapsing in on itself.