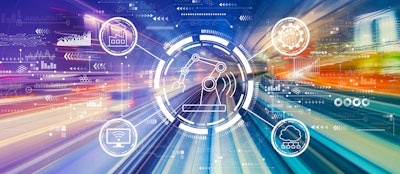
Manufacturing enterprise resource planning (ERP) solutions has a proven capacity to enhance workflow visibility, streamline asset and resource management and deliver real-time reports that support data-driven decision-making, making it highly relevant in the modern manufacturing landscape. Eager to remain competitive, many modern organizations favor manufacturing ERP implementation.
Owing to the solution's central role in manufacturing enterprises, stakeholders should make a reasonable and well-grounded ERP vendor choice.
5 ERP selection criteria for manufacturers
Functionality is the most obvious selection criteria for ERP, and rightfully so. But when it comes to industry-specific ERP platforms, feature sets often look identical. Thus, stakeholders need to consider other important aspects of ERPs.
1. Deployment model
There are fundamental differences between cloud and on-premises ERPs—in their environments, pricing models, maintenance needs and levels of security.
Installed and managed in an enterprise’s own IT infrastructure, on-premises ERP provides owners with full control over its operation and the freedom to customize, configure and protect it as they see fit. However, all this must be done under their own steam, so an in-house IT team is a must in this scenario.
Driven by the need for unlimited storage space, flexibility and mobility, many manufacturers today opt for cloud-based ERPs instead. They are scalable and customizable on-demand, accessible anytime, anywhere, come equipped with necessary security controls and cost a moderate monthly fee. On the other hand, public cloud infrastructure is hackable by nature and vulnerable to downtime.
Hybrid ERPs combining on-premises and cloud features are an option for forward-thinking manufacturers. Choosing to keep the most sensitive data and operations on-premises and hosting less critical business processes in the cloud, you can tailor the infrastructure to your needs and financial capacity while having the best of both worlds.
2. Scalability
Scalability is about the extent to which an IT infrastructure can scale up, how much it will cost and what new maintenance efforts it will demand. Another feature to keep in mind is the ease of integration and customization—do new features require development or are they plug-and-play?
If you plan to expand to foreign markets, then it’s also critical to choose an ERP that supports global growth and complies with international financial and legal requirements and tax rules.
Last but not least, if an ERP vendor doesn’t seem to keep up with the trends, there is a risk your enterprise will outgrow the ERP’s capabilities.
3. Ease of integration
An ERP needs to be well integrated with the rest of your manufacturing IT infrastructure to bring the intended benefits.
Depending on an ERP’s default features, integration can be with dedicated integration tools or default APIs. Although integration through them would still require handiwork, this is a realistic task for in-house IT teams.
If a platform offers neither integration route, manufacturers will need to build a custom integration adapter or application for each ERP integration. In this case, the process may prove lengthy and require specialized expertise.
Another, more specific integration option is in-built EDI connectors or integration modules, commonly utilized in the manufacturing industry for exchanging business documents with suppliers and customers.
4. Mobile application
The increasing geographic distribution of manufacturing operations and the shift to partially remote work puts a premium on reporting and real-time data accessibility. Thus, when deciding on your future ERP platform, look into its mobile capabilities and how well they meet your requirements.
Apart from the fact that not all vendors have a proprietary mobile app, it is worth noting that ERP applications may differ in feature variety, customization opportunities and compatibility from their desktop versions.
5. The total cost of ownership
The ERP price is a primary consideration for future adopters, but in practice the system’s total cost often goes far beyond initial expectations.
In addition to ERP licensing fees, manufacturers also need to make allowances for the required hardware and user licenses together with the implementation, customization and data migration resources needed.
Operating costs, including additional user licenses, admin and support costs, additional integrations and security provisions, should also be given due consideration.
Over and above, assess the expertise of your in-house IT team related to ERP maintenance, upscaling and customization. Will your specialists be able to keep the system up and running and prevent potential downtimes and security issues, or will you need to hire extra hands or even outsource the task to external ERP developers? The cost of external assistance may vary significantly from solution to solution and should be taken into account, together with the gamut of IT outsourcing risks.
What’s your choice?
In the modern landscape, manufacturers are more focused than ever on keeping their production processes flexible, cost-efficient and resilient to disruptions. ERPs, historically geared toward supporting manufacturing workflows, prove an appropriate solution for achieving these goals while also streamlining some labor-intensive tasks and gaining useful operational insights.
For the ERP software to prove beneficial in both the short and long term, manufacturers need to take into consideration other relevant aspects beyond functionality, such as available hosting options, the total cost of ownership, ease of integration and upscaling and the availability of a mobile app.