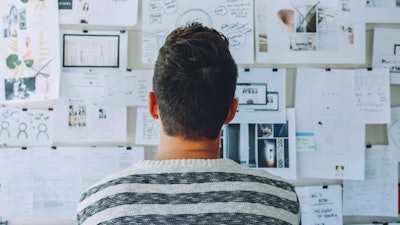
The Coronavirus disease (COVID-19) drastically transformed global manufacturing, challenging many established and accepted paradigms of supply chain management and forcing companies to reevaluate risk mitigation strategies. However, there is a clear consensus on the greatest supply chain challenges that have continued to wreak havoc since the onset of the pandemic. Global supply chains have been drained, and many industries lack the installed production capacity to catch up in the near term. This has made it impossible to depend on consistent deliveries and highlights a fatal flaw within the just-in-time (JIT) strategies being used by most industries. Take the global semiconductor crisis for example. Analysis from Seraph shows that holding just $30 million in additional inventory would have allowed for an additional $3 billion in profits.
Supply chain stability and required actions
Pre-pandemic, there was a fundamental assumption that supply chains were inherently stable. The expectation that suppliers receiving electronic orders would build the parts and ship high-quality product on time and with advance notice to the customer was rarely challenged. As exceptions were increasingly rare, supply chain and production capacity optimization emphasized a preference for holding low inventory levels throughout the supply chain to minimize capital deployment. Minor disruptions arising at one juncture would be typically covered by the limited inventory held at other points in the chain such that companies could effectively manage the interruption. Enterprise resource planning (ERP) systems managed the reorder processes well, while supply chain professionals maintained system parameters and manage exceptions.
During COVID-19, there was a gradual drain of the already minimal inventory levels throughout supply chains across many industries. The unexpectedly swift recovery of economic demand driven by government stimulus has caught supply chains by surprise. With inventory buffers depleted and production capacity attempting to cover both renewed customer demand and inventory replenishment, restoring the supply chain is now a major challenge across most industries.
In the automotive industry, the consequences of poor inventory management are unfolding in real time with the current shortage of semiconductor components. Although these chips are an essential part of vehicle production, neither the OEMs nor suppliers had long-term purchasing strategies in place to safeguard production. Ironically, this is not a singular event. Just like the financial crisis in 2008, automotive suppliers started canceling orders from their supply base at the start of the pandemic, as limited capital was built into component pricing for inventory or warehouse space. While automotive production stalled, consumer electronics companies increased production capacity to meet an unprecedented spike in demand during global lockdown periods. The absence of a long-term purchasing strategy has inflicted billions of dollars in avoidable production losses on the OEMs.
Look at establishing a dedicated supply chain War Room Team to track suppliers from Tier 1 through Tier N as defined by their risk profile. This team should be charged with executing a new risk quantified supply chain strategy, where the probability and impact of potential events are built into the model and proactive interventions can occur to limit surprises. Industry leaders are already on this path.
Supply chain organizational design and skill acquisition
People have become a critical constraint for many industries, as the COVID-19 pandemic continues. The skilled worker shortages that existed prior to the pandemic have become more apparent, as has the lack of people development. COVID-19 highlighted these challenges, however most companies still lack a plan to address this pressing need, as they are currently firefighting immediate problems with small teams that can be mobilized. One area we all know well is at the heart of this problem, production control and logistics.
Production control and logistics teams are dependent on ERP systems that land orders and interface directly with requirements specified by their customers. Organizations were designed to minimize human capital and rely on the ERP systems to secure production. Moving forward, there’s a need for significant external help to assess and optimize inventory projections not simply based on distance and transit time, but that incorporate financial, quantified risk and customer support factors. Further complications will need to be addressed in warehouse space that was previously designed upon highly optimized JIT models.
A recent survey from the National Association of Manufacturers (NAM) revealed that an overwhelming 62% of respondents reported attracting and retaining a quality workforce as their primary current business challenge in Q4 2020. The skill gaps clients are experiencing make the need for having a clear people strategy even more important. However, very few organizations have the skills and capacity to address these changes internally. Senior management should make this a point of focus and immediately source external organizations.
Reestablished supply chain monitoring with a dedicated War Room Team
Beyond risk mitigation through inventory optimization, companies need to adopt modernized and structured approaches to supply chain management relative to previous years. Pre-COVID-19, the hierarchy of supplier networks was well established and the links between them stable. When large customers send purchase orders to a Tier 1 suppliers, there was an expectation that it would be further communicated out to the Tier N sub-suppliers and delivered on time with quality and quantity assurance. Due to COVID-19 disruptions, Tier N suppliers have increasingly become “surprise” capacity constraints.
For the automotive industry, these new challenges are driving significant changes in raw material and supplier management strategy, particularly at the OEM level. Certain critical commodities such as semiconductors, resins and metals, have all been managed by the supply base for the last few decades. However, as demand for most consumer goods is forecast to grow at record pace, manufacturers have already begun to manage these constrained commodities. Manufacturers have historically depended on rapidly formed “shadow” task forces to manage supply chain challenges. The growing frequency of “black swan” events is driving manufacturers to put dedicated supplier tracking teams in place and invest in tools to help them gain better visibility into the supply chain. This can include OEE tracking software and early alert tools.
Here’s an action plan recommendation:
1. Evaluate your systems and supply chain organization and engage the required expertise either by bringing back retirees or engaging external support who can partner with new hires to learn at an accelerated pace.
2. Implement a supply chain war room with a dedicated team, comprised of staff who have no other responsibility than to protect the flow of material to production.
3. Execute a supplier tracking strategy and incorporate risk adjusted metrics into future sourcing decisions.