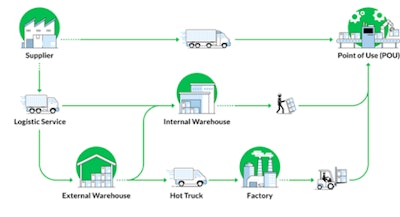
Material flow analysis (MFA), or process flow analysis (PFA), are fundamental aspects of a material handling strategy. MFA has the goal of mapping, inspecting and evaluating all flows within an organization. Its focus is to gain a statistical benchmark for a supply chain. For instance, how are parts flowing from suppliers, to storage locations, and finally to the point of use? And, how can you get product to customers in a faster, yet more controlled manner?
When operational MFA can formally track issues and exceptions, it will expose opportunities for improving the production process, reducing operating costs, and finding ways to cut waste. This analysis is then used to save valuable time, assets and expenses.
The problem: preventing critical disruptions
Some of the most critical disruptions in production happen due to material availability at point of use. When production is down because of missing parts or materials, lead times for products become uncertain. Employees and customers alike are negatively affected. The customer does not get their product at the promised date and time. The employees in the assembly lines are idle and costing the organization sometimes thousands of dollars (per minute). In the meantime, the material flow managers are scrambling to resolve the issue.
MFA can be applied in almost all aspects leading up to production. It also can help you explore the causes of missing items at the time of production and in some cases, real-time visibility to manage disruptions. An MFA also gives you the ability to track downtime, so you can allocate production resources where they can be utilized across multiple departments.
The difference between a formal and informal MFA lies in the technology used to conduct the analysis. Many manufacturers and third-party logistics providers continue to rely on phone, email, and spreadsheets to communicate, making historical data collection and analysis time-consuming and inconsistent. An informal approach makes it difficult to drive process improvements that will prevent future disruptions.
The key component: trackable improvement
Formally tracking every aspect of material flow through cloud-based software solutions enables a supply chain team to learn and improve immediately from each issue and exception.
Data integrity is key to discovering problems and identifying effective ways to reduce them. Cloud-based software solutions are available today that are simple to launch and easy to integrate into other supply chain systems a manufacturer is using. These solutions offer everything from streamlining communication, so everyone is working with the most current information, to automating in a repeatable fashion how you react to and avoid disruptions.
Look for options with built-in workflows that track the state of a request and are easily configured to handle different types of processes. A great tool will not only make entering and processing requests easy but will also provide real-time visibility. This makes it obvious who owns the request, details what the next steps are, communicates automatically as the ownership shifts and tracks key metrics. Additionally, the tool should make it easy to evaluate the root cause report on both day-to-day level statistics and longer trends.
Cloud-based software can ensure that requests are shared and tracked in a fashion that provides both management and operators the necessary data to make informed decisions and analysis. It also will ensure processes are repeatable and documented. And, that points in the process requiring cross location communication or hands-off are well documented, trained and automated.
Processes and tools that generate metrics can analyze them regularly using proven techniques to drive improvement. Systems automation is the most effective way to maintain order in a supply chain that can turn chaotic at any time.
The final piece: an incident command center
Once MFA is optimized with formal tracking and automation, the final piece of the puzzle to prevent critical disruptions is a cloud-based incident command center. This concept is not much different than the command centers a city would set up in case of fires or other threats. Data collection from MFAs drive automated process improvement and can alert teams about potential issues, so they can be remediated and investigated.
Imagine the benefits of knowing in real-time that a part has gone missing or a shipment is late. Or the time and stress saved in knowing the missing part is sitting on the loading dock. Imagine the efficiency of updating all systems immediately after a change in the production process is implemented. Imagine the achievement in reducing urgent requests and incident reports from 200 per day to 15.
Production visibility is more important than ever. Whether you are working to build resiliency over long-term risks, avoid imminent impact or recover from an outage, communication, visibility and coordination are essential. Taking an automated, integrated approach to MFA will give you an opportunity to be proactive in optimizing the cost of production. Isn’t that what supply chain strategy is all about?