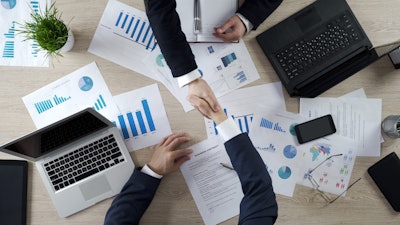
Last year, if you were asked to share the most confounding supply chain disruption ever experienced, what would you have said? Perhaps a regional catastrophe like the 2011 tsunami in Japan or a component shortage like the 2018 multilayer ceramic capacitor (MLCC) famine.
What about today? If your answer changed this year, you aren’t alone. In fact, Jabil’s “Supply Chain Resilience in a Post-Pandemic World” survey of 715 supply chain professionals found that the Coronavirus disease (COVID-19) impacted 78% of respondent supply chains, more than any other disruption over the last decade.
Disruptions aren’t new. Supply chain leaders see material shortages, trade wars and natural disasters come and go. Each problem is different, but they are usually contained and short-lived. We find workarounds in the meantime, and if it’s a site that’s down, we try to get it back online as quickly as possible.
But, the extraordinary challenge of a global pandemic is that it’s global and pervasive. It isn’t confined to a particular location or a particular type of component. And if operations are ramped too quickly without comprehensive safety measures in place, the problem could easily worsen and extend.
COVID-19 has caused untold havoc on our networks and more than a few sleepless nights. But, it has also afforded us a teaching moment that can help us supercharge our supply chain resiliency in ways never considered before.
Here are five lessons learned from COVID-19.
1. Set a course to multi-source
Nearly 90% of survey respondents suffered a direct business impact from sourcing issues amid the COVID-19 pandemic. These issues led to production and time to market delays and tighter profit margins, among other problems. As a result, 40% of survey respondents report that their companies have adjusted their sourcing partnerships.
It’s safe to say that adjustments in many cases meant additions. To navigate this tricky year, you can bet we took advantage of every one of our 100 sites and more than 27,000 suppliers. Without the ability to multi-source, meeting our customer needs would have been impossible.
Relying on a single source or a single geography is a recipe for disaster. Having a stable of alternative qualified suppliers is crucial to maintaining production volume amid a global crisis like a pandemic.
2. Diversify geographies
Of course, even with 100 sites and thousands of suppliers, it does little good if they are all located in the same place. An important element of resiliency is to ensure suppliers and makers are dispersed globally.
COVID-19 taught us an important lesson in this regard, which is why we’ll see more companies investing in a diversified global footprint. In fact, in our survey, nearly 90% of participants agreed that, even though they’ve always known the value of a diversified supply chain footprint and sourcing strategies, recent events (COVID-19, tariffs, etc.) have made it even more clear.
Although this type of planning doesn’t happen overnight, we’re already seeing partners taking initiative by electing a local team to make decisions about what’s sourced in their area. By delegating these decisions regionally, they are able to enhance diversity more effectively.
3. Respect the technology
Supply chain success relies on three pillars—people, processes and technology. As COVID-19 enveloped the world, two of these pillars cracked; people were laid off or displaced by quarantine, and processes were disrupted.
So, reliance on technology intensified significantly, and those with outdated or insufficient systems had a harder time recovering. It’s no wonder, then, that over 90% of surveyed supply chain leaders thought companies will recover more quickly if they invest in digital technologies and analytics, and nearly 100% said that they are already investing in technologies or services to address the pandemic’s effect on supply chains.
What is the most popular type of technology that companies are pursuing as a result of COVID-19? As you might guess, supply chain optimization and visibility technologies top the list.
These applications help leaders scenario-plan by imagining different situations that could impact various points of the supply chain. They use a combination of big data and sophisticated analytics that paint an end-to-end quantitative picture of a company’s supply chain and actionable business insights.
Optimization technologies have always been a powerful and game-changing, but it was absolutely mission-critical to navigate 2020. If you had it, your investment may have seen multiples of return in this year alone.
4. Rubberize your resilience strategy
Resilience is like a rubber band. If one area is stretched or stressed, the rest of the band reacts to compensate. It’s easy to bend, but hard to break.
When supply chain resiliency is established, local disruptions aren’t fatal because a contingency plan for production, inventory, lead-times and logistics shifts into gear. With 62% of OEMs having experienced production delivery or time-to-market delays due to the pandemic, robust resilience programs are crucial to a quick recovery and keeping customer delivery timelines on track.
Much like technology, companies that lacked a resilience strategy suffered the consequences this year. But, it’s never too late to get started. One approach might be to start by establishing a demand plan for the “new normal,” as opposed to historical-based forecasts.
However, manufacturers choose to approach it, resilience planning will no doubt be a point of emphasis for years to come.
5. Relationships matter
When we think of the supply chain, we think of materials, components and widgets. But, most importantly, the supply chain is made up of people – people who, like us, are trying to keep their loved ones safe and their businesses afloat.
Supplier relationship managers are extremely important, especially during times like these. They do not negotiate prices or transact with their commodity counterparts. Instead, they focus on building relationships at the executive level by understanding their businesses and seizing opportunities for mutual growth.
COVID-19 has thwarted supplier relationship management, which relies heavily on face-to-face interactions and in-person meetings. Supply chain managers are rethinking how they can maintain those relationships’ new ways.
But, like many of these other areas I’ve reviewed, those who had not invested in relationships prior to the pandemic found themselves behind the ball this year when supply dried up. If a supplier is only running at 20-30% capacity because of a disruption, you can bet their limited goods will be prioritized by the strength of their relationships.
Supply chain disruptions come and go, and COVID-19 was, no doubt, a supply chain disruption for the ages. We shouldn’t underestimate these when they come along, but we also shouldn’t underestimate our ability to prepare and take action.
If you’ve talked about the need for a more strategic supply chain in theoretical terms, take note that we’re now living the perfect business case. Now is the time to embrace the lessons 2020 has given us and justify investment ROI to business leaders so that our supply chains are ready for whatever comes next. Because, as we know, it’s only a matter of time before the next disruption.