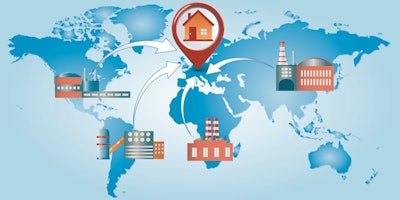
The worst global pandemic in 100 years has forced a change in the world order greater even than the events of the 2007-08 financial crisis. With many locations in the world still under lockdown or some form of restrictions, many experts confidently predict that supply chains are going to have to fundamentally change, along with how they operate.
The reason why this may be is not like any other downturn in recent history is because the Coronavirus disease (COVID-19) has impacted all elements of the value chain, yet no one was prepared for it. The industry is still languishing in a Coronavirus-induced fog and the path out is far from clear.
Supply chain re-evaluations
Because much of the current crisis stems from the underlying frailties of global supply chains, we can guess that most supply chain and logistics managers will be looking harder at resilience and robustness. There is panic that, once a few of the weaker links go down, the chain will tumble shortly after.
This almost certainly means that the supply chains of the “New Normal” will be far different from what we currently are used to. They will stress diversification of manufacturing and reshoring. But, this will only be possible if there is a significant investment in the right technologies to improve on productivity.
Manufacturers now know more than ever that it is important not to rely on single suppliers, and instead find ways to make use of components that can be sourced from many different locations. This could mean the end of China’s current manufacturing hegemony.
Reshoring, automation and ‘microfactories’
If there was anything to cushion the shock of the Coronavirus, it was automation. For example, the supply chains for many semiconductors were not as disrupted as in many other industries. This has spurred on discussion for investments in a nascent technology—that of microfactories.
A microfactory is not a small factory, but a novel way of thinking about production. In short, it is a production plant that can be made up of lots of component microfactory “cells” that can come together in a myriad number of ways depending on the work that needs doing.
Microfactories are increasingly alluring to businesses considering a reversal of the cost-focused globalization that has been the exception rather than the rule since the 1980s. It is the high degrees of automation that factories offer that may be the essential ingredient in decentralizing production. Another advantage is that these microfactories circumvent the problem that most Western countries have in that they have lost the social infrastructure that supports manufacturing.
Although it is too early to tell, these multi-purpose microfactories will probably be designed to deal with much smaller batches to avoid the need for original equipment manufacturers (OEMs) to build their own lines. Instead, they can call on local contract facilities, which can then issue the software to help them re-program the line, so they can start producing a specific product. All the while complex robotics and artificial intelligence (AI) act to keep product carriers moving through conveyors, examining what needs to happen next and what tools are required in order to deliver on complex tasks.
Accelerating the inevitable?
Even before the Coronavirus, the market was leaning toward smart factories. They are an inevitable product of the slow drawing out of the so-called Industry 4.0 revolution. But, the pivot toward reshoring has accelerated interest because local production helps to cut the delivery time to a minimum.
Microfactories may only be complementary to larger facilities, instead of outright replacing them. (And, in any case, these larger factories will also inevitably start moving toward Industry 4.0 tech.) The idea, for now, is that they will make it easier for OEMs to access a more personal type of manufacturing through outsourced providers instead of outsourcing the lot to one location in China and beyond. Larger producers may also see microfactories as a backup plan, in case one of their suppliers is unable to deliver on its promises.
Resistances to de-globalization
Of course, this doesn’t mean that everything will come back home. A lot of OEMs still rely on individual fabrication plants for each product they employ. Meaning they will have little prospects by way of building a more flexible supply. Only the very largest companies are absolutely guaranteed the option of multi-sourcing.
Another factor to keep the globalization trend alive may be the increase in technologies designed to help suppliers become more resilient — hence eliminating the switch over to a more localized production. Digital twin technology is now being readily applied to product design, and will certainly assist OEMs in determining visibility over what it is they buy from overseas. In a digital twin environment, manufacturers will be able to utilize digital models to help them window shop suppliers and subcontractors at their leisure. In that sense, there may not be as much need for local microfactories.
In short though, it can safely be said that how supply chains operate will change a lot over the coming years. We might not know how this change will come about, but we can predict. The Coronavirus has both accelerated the inevitable and forced the coming change. Whether this truly will be the end of the 40-plus-year trend of globalization, or just a new manifestation of it, time will tell.