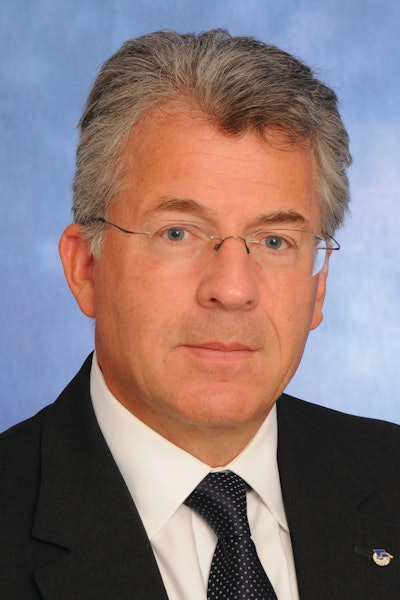
Fueling up your car at the local gas station may lead you to consider for a moment the supply chain that makes this act possible. For an executive with an interest in supply and demand management, that’s only natural. You may even arrive at the conclusion that this cannot be too difficult—after all, it’s bulk and only a few products, right?
Quite the contrary. Setting aside for a moment whether running fuel logistics is easy, there is a world of complexity before the oil or gas is even flowing from a production well.
Industry complexities
Demand for energy is going up relentlessly outside the Organisation for Economic Co-operation and Development (OECD) at the same time that ‘easy’ oil and gas are largely exhausted. More sophisticated technologies and equipment are used to coax oil and gas from ever deeper off-shore, sub-zero arctic regions, tar-sands and shale formations.
To pull off the successful implementation of those technologies, oil and gas companies are increasingly working with specialized partners—such that include suppliers of specialized vessels or transmission systems, operators of drilling rigs, geological specialists and drilling mud suppliers. The complex equipment used in floating production and storage vessels (FPSO’s), drilling platforms and fracking trucks has components from thousands of suppliers.
So, what does this all mean?
I recently asked a senior executive of one of the largest global oil field service companies what concerned him most about supply chain management. His answer came fast: Traceability, i.e., knowing in real time the supplier and current whereabouts of every piece of equipment and every component.
Since the very visible DeepWater Horizon explosion in the Macondo Prospect, this issue has become even more pressing to manage. As we move ahead, more adequate certification rules and more compliance control will only reinforce this.
Visual effects
Let me illustrate what can happen when traceability goes wrong. Not long ago, I was sitting next to a senior technical expert of a major U.S. engine manufacturer who had just returned from many weeks in the China Seas. The main purpose of his visit was to investigate the root cause of failure of almost all generator sets on a number of drilling platforms. Various days of no production translated into many millions of dollars lost and created major upsets for the many partners operating on a platform. Not to mention that the relationships with both the country owning the reserves and the financial partners were put at risk.
The reason for the failure was a low cost seal. Maintenance had bought a cheap knock-off instead of the original OEM part. A couple of hundred dollars saved and many millions lost.
In this instance, only generators failed and production stopped. In another occasion, it could have been a failed blow-out preventer resulting not just in down time but possibly catastrophic safety and environmental consequences.
The supply chain management before oil or gas flows from the well is becoming increasingly complex. And it is crucial in the oil and gas industry that companies not only trace all parts from origin to application but have the ability and resources to do so effectively.
Maarten van Hasselt is a Senior Vice President and Global Energy Sector Leader, America at Celerant Consulting, London. He has a combination of oil and gas industry and consulting experience spanning multiple continents with leading companies including GE Oil & Gas Inc., Royal Dutch Shell and Repsol. His expertise includes operational strategy and business development and spans the whole value chain from upstream to refining to marketing and distribution.