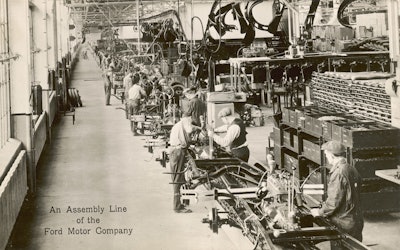
Industry 4.0 is in every sense of the word a complete revolution of traditional manufacturing and supply chain management through the increased reliance on the Industrial Internet of Things (IIoT)—automation, machine learning (ML), big data and other smart technologies. With a market value of around $65 billion (which will triple over the next 5 years), Industry 4.0 provides an answer to many of the common challenges companies face today—namely, the need for end-to-end connectivity and real-time insights.
Understanding how groundbreaking Industry 4.0 will be requires one to revisit the three previous Industrial Revolutions. In late 18th century Britain, manufacturing evolved from labor driven by human and animal effort to labor powered by water and steam. About 100 years later, Henry Ford’s assembly line was introduced. Water and steam would be replaced by oil, gas and electric power, resulting in the first forms of automation. The proliferation of more electronics in factories characterized the Third Revolution, including the shift away from analog and mechanical to digital technology. At every stage, the speed and effectiveness of production increased significantly. Industry 4.0 won’t just bring improvements to efficiency, but fundamental changes to how manufacturing and supply chain management companies operate.
Why adopt Industry 4.0?
Although resistance to each industrial revolution existed, progress continued. Businesses that oppose change will become outpaced by competitors that adopt Industry 4.0 practices and technology. Moreover, despite the time, resources and training necessary for implementation, the overwhelming benefits of adoption will considerably enhance business processes via analytics, accurate data and monitoring.
Manufacturing businesses already collect vast amounts of data, but the problem is that this data is locked in siloed systems, creating limited data sharing. The lack of data harmonization will make integration almost impossible, causing inconsistencies between distributed sites and impacting the bottom line. But, with Industry 4.0 practices like smart manufacturing, enterprises can evolve their current baseline processes and performance through analytics, accurate data streaming and monitoring. Similarly, by using predictive analysis tools, including artificial intelligence (AI) and ML, manufacturers can predict equipment failures and prevent them before they happen. Finally, leveraging computer vision can proactively recommend spare part purchases, among many other prognostic efficiencies.
Adopting Industry 4.0 practices and technologies will likewise enable organizations to tap into insights and optimize all facets of their manufacturing processes and supply chain, boosting profitability and competitiveness. Part of this high productivity comes from – again – better data access. For example, the advanced sensors, embedded software and robotics of Industry 4.0 smart factories collect and analyze all types of data, empowering businesses to make more informed decisions. Furthermore, when the data from production operations becomes unified with operational data from other enterprise systems, even more visibility into actionable insights becomes possible. Yet, while Industry 4.0 will enable manufactures and supply chain managers to create new jobs, it will come with challenges – particularly employee training. Inevitably, teams will require upskilling to achieve desired business outcomes.
How to begin adopting an end-to-end approach
While it is essential to understand the game-changing benefits of adopting Industry 4.0, successfully implementing these new technologies and methodologies will require an end-to-end approach that incorporates people, processes, technologies and data. When it comes to people, it’s critical to have a comprehensive understanding of their current capabilities and what gaps Industry 4.0 can fill in, such as will re-skilling be necessary or can new technology fix the issue? Likewise, it will be vital to ensure that one’s workforce aligns with factory leadership and other key influences. In terms of processes, manufacturers will need to ask themselves how they plan to inject new technologies into existing strategies. Rather than brute force a square block into a round hole, businesses should first closely examine and analyze their processes, considering stages, manual and automated processes, defect levels and potential causes and all sources of data.
As for technologies and data, manufacturers need to determine which of the Industry 4.0 technologies will most benefit their business. Whether Internet of Things (IoT) and cloud computing or augmented reality/virtual reality (AR/VR) and digital twins, companies must have a game plan for leveraging these technologies. Digital twin simulations, plus AI and ML, can run simulated scenarios with no risk to real-time production, reducing scrap and yield losses. Similarly, organizations will need to consider their infrastructure from a cloud-to-edge networking perspective. Before implementation, manufacturers need to outline their infrastructure requirements, including any cybersecurity and platform architecture necessary to support data collection and storage.
Protecting against future disruption
These past few years of supply chain crisis have laid bare the vulnerabilities of the manufacturing industry. As businesses struggle to fill vacant positions to keep pace with supply and demand, the willingness to adopt Industry 4.0 grows. And, to build a robust strategy that can survive disruption, manufacturers will need to integrate production operations with transparent and efficient supply chains. From predictive shipping to data sharing, Industry 4.0 will transform the way manufacturers interact with suppliers, consumers and partners and enterprises need to take every preparatory step for the next industrial revolution.