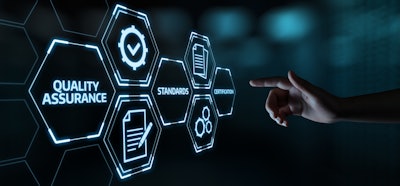
The chip shortage has reached a crisis point, leading to higher consumer prices on game consoles, mobile phones and TVs; potentially impacting nearly 1 million units of global light vehicle production.
That has given new life to the conversation about the need for more supply chain resiliency.
But, this is not a new conversation. Supply chain players and pundits have been talking about the need for resilience for years now. A 2014 McKinsey article went as far as to suggest that companies adopt an incentive system originally developed in the U.S.S.R. to reduce uncertainty and improve target estimates for central planning forecasts of state-run companies.
Let’s be clear; enterprises shouldn’t adopt Soviet business practices. But, now is the time for organizations to operationalize their supply chain resilience by aligning incentives, organizations and systems within a new, data-driven approach
This orientation is not new. Academic studies have clearly established a disconnect between incentives and performance measurement in supply chains. The problem of aligning incentives across a decentralized global electronics value chain often results in inefficiencies and additional costs. When data is distributed across supply chains, it is more difficult to identify and measure performance across common metrics. The practical implications of this research are simple: if you want to change a behavior to maximize resilience, you must develop metrics that reinforce that behavior and convince people that these metrics are being regularly seen by others.
Resiliency at the point of new product design is a good place to start
Building resilience into new product introduction (NPI) efforts is a great way to get started.
Return on resilience efforts need to start at the product level because much risk is locked in at the point of new product design. Engineers can lower new product risk by increasing their scope of external intelligence and grading the risk of components within their bill of materials.
But, using market intelligence to lower risk and build resilience into NPI efforts is just part of what’s needed to make products – and the businesses that create them – more resilient.
Return on resilience requires cross-functional alignment
Formalizing a return on resilience approach requires aligning incentives across corporate, engineering, finance, procurement and supply chain disciplines within an organization.
This may require a top-down mandate, as it will impact corporate key performance indicators (KPIs) at a departmental level and bonus or performance measurements at an individual level.
This could come in the form of assigning a specific KPI goal related to the successful completion of a product through its design or introduction and/or pushing engineering to improve resilience beyond the product itself.
Striking the right balance between cost savings and other considerations is key
Organizations have long talked about the importance of considering multiple factors in sourcing direct materials, diversifying their sources of supply and better understanding supplier risk. But, such efforts often fail to land correctly. This happens because the finance departments in most organizations that benchmark the performance of semiconductor and electronics component procurement frequently put cost containment goals above all other considerations.
As Harvard Business Review notes, lean global supply chains and just-in-time methodologies in manufacturing, which rely on forecasting based on historical data and don’t typically consider major disruptions, are partially to blame for supply chain disruptions.
The Wall Street Journal reports “as supply chains get more global and car makers increasingly rely on single suppliers, the system has grown brittle” so the “hyper-efficient auto supply chain symbolized by the words ‘just in time’ is undergoing its biggest transformation in more than half a century, accelerated by the troubles car makers have suffered during the pandemic.”
Organizations should establish common ways of measuring risk
However, organizations are not going to see a shift in their behaviors related to sourcing processes or RFQ awards until their finance departments accept and understand other risk factors. Creating such understanding will require normalizing the risk factors for products and their components by establishing a common way of measuring risk across different products. That way, product resiliency can be operationalized through the implementation of a risk index.
This approach is broadly accepted in other domains. Cost benefit analysis is an established economic approach and the World Bank has an economic resilience framework. Methods and models also exist to help define resilience in engineering, among other disciplines.
Yet seldom is resilience operationalized in direct material sourcing and supply chain. It's not complicated, it just needs to be formalized. For example, an organization could source from one supplier at the lowest cost, or it could source from three suppliers, but the prices might spread to 15% across three suppliers. What an organization might want to do in the latter case is optimize the volume allocation so that the lowest cost supplier gets 60% of its volume and the other two suppliers get 20% each. The weighted risk premium is then 12% above the lowest cost to ensure diversified sources of supply. Finance would say that's a good outcome.
New forms of market intelligence can enable even greater resiliency
More sophisticated models could emerge over time, enabled by new forms of market intelligence to help buyers understand risk drivers and trends in specific commodities.
That could include various risk aspects, such as the financial health of a supplier. A supplier’s manufacturing location, which can impact trade and tariff policy, is another risk factor that semiconductor and electronic component buyers might find worthy of consideration.
The physical supply chain, including logistics and transportation, represents another important set of risk factors. If you’re buffering inventory at a location or employing a mix of air and sea transportation, the portion that you’re shipping by air will reduce your average total lead time. So, it is not just an increase in costs, which is how it's treated now. Instead, it can be viewed as part of the cost of return on resilience that you’re investing in the supply chain more formally.
Now is the time for a fresh approach to operationalizing resilience. Organizations that embrace more intelligent approaches will be better positioned to thrive in this unpredictable world.