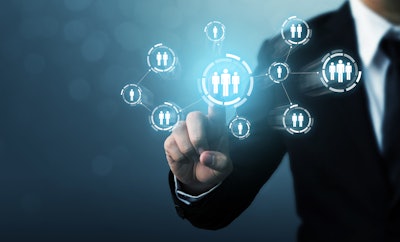
After an especially chaotic few years, change and disruption may feel like the only certainties in supply chain. Along with macrotrends like a global pandemic, geopolitical conflict and a competitive labor market, new and emerging technologies are continuing to transform the ways in which supply chain organizations carry out key processes. Meanwhile, changing customer behaviors and expectations are putting pressure on organizations to continually boost their efficiency and customer responsiveness.
Amid so much change, logistics employees—which includes employees working in transportation as well as warehousing—are remaining remarkably steady. In 2022 research with more than 1,100 global organizations, APQC finds that transportation employees have a median tenure of eight years, while warehouse employees have a median tenure of 10 years (Figure 1). Median turnover rates are also lower than many people might expect—around five percent for warehouse employees and 9 percent for transportation employees.
Figure 1, APQC
Contrary to horror stories you may have seen in the media about what it’s like to work in a warehouse, it seems that many logistics employees find their work meaningful enough to stay with their current employer for a decade or longer. It’s certainly a line of work that makes a difference in the world—even the ability to hold a pen or pencil in your hand means that you have some supply chain and logistics employees to thank. The ability to carry out meaningful work is especially attractive to millennials, who now make up at least half the workforce in many organizations.
APQC finds that it takes a median of 9 months for both transportation and warehouse employees to become proficient in their roles. It is in every organization’s best interest to retain its logistics employees for that reason alone, rather than watching them take their experience and expertise elsewhere and having to train new employees.
Organizations have a wide range of tactics at their disposal for retaining employees, from competitive compensation and reward programs to flexible work arrangements. However, APQC research on employee retention has found that the pursuit of better career development opportunities is the most common reason why employees seek work elsewhere. Providing opportunities for your logistics employees to continue growing their skills is one of the most effective ways to keep them engaged and satisfied with the work they’re doing.
Focus on your learning budget for logistics
Many organizations have an opportunity to invest more than they currently do in developing logistics employees. For example, APQC finds that the median learning budget for transportation employees is $135 per year, while the median learning budget for warehouse employees is $130 per year (Figure 2).
Figure 2, APQC
Learning and development technologies available on the market today allow organizations to achieve economies of scale and keep development costs lower per employee. Even so, it’s still the case that many organizations may be underfunding development for logistics employees. APQC finds that the median learning budget per business entity employee (regardless of function or department) is $147.78—nearly 20 dollars more per employee than what organizations spend on logistics employees specifically.
There’s no good reason why logistics employees would need a smaller development budget than their peers in other functional areas—in fact, the opposite is more likely to be true. Artificial Intelligence (AI) is a case in point. We’ve found that the adoption of AI-driven technologies is driving the need for new skills among supply chain professionals. This not only includes the technical skills needed to use technology effectively, but also soft skills like collaboration, communication, critical thinking, problem solving, and relationship building skills. These skills allow supply chain professionals to step into more strategic, value-added forms of work once technologies like automation and AI take over manually intensive tasks like data entry.
If your organization falls in the bottom quartile for logistics learning budgets, it’s certainly worth taking a closer look to ask if you should be investing more. You might find that the amount you currently spend makes sense because of your organization’s size, ability to conduct on-the-job training, existing employee expertise, or other factors that are unique to your organization. At the very least, it’s important to have a rationale for why you spend the amount that you do in this area.
Next steps
Investing in the development of your logistics employees not only helps them be better prepared for new technologies, but also reduces the risk that these employees will seek development opportunities elsewhere. To retain logistics employees and the years of experience they bring to the table, it’s important to benchmark your learning budget for these employees against your industry peers and competitors. Providing logistics employees with meaningful opportunities to grow will make them more likely to stay.