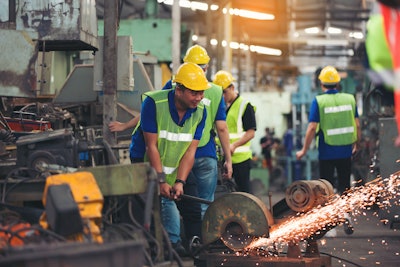
The manufacturing industry’s labor shortage shows no sign of letting up. More than two million U.S. industrial jobs went unfilled in the past decade, costing the economy $2.5 trillion, according to McKinsey estimates. This problem is only worsening as older generations retire, few are springing up to take their place. Today, many members of the younger generations prefer working in industries like tech and healthcare, which may offer more comprehensive pay and benefits.
In order to address the labor shortage, industrial companies need to invest in digital solutions. This does not, contrary to popular belief, necessarily mean replacing human factory workers through means such as robotics and automation. Rather, it means taking advantage of solutions that use cutting-edge technologies such as machine learning and artificial intelligence to empower existing factory workers and provide them with new skill sets that they might not possess.
Engineers and operators on the production floor, for example, may benefit from a digital twin. This much-hyped technology allows the user to create a virtual copy of an industrial process. Using this tool, they can explore both hypothetical and actual scenarios they might encounter on the factory floor, and tinker with process settings to see how to adjust them. For example, investigating how shifting the temperature of a specific reaction a few degrees might affect the yield and quality of the final product that comes out. This reduces the company’s dependence on having more employees, and in particular more specifically trained employees, as fewer employees with less on-the-job training can learn to do the same tasks.
Not only can these tools be employed to improve existing processes, but they can also be used as educational tools. By using a digital twin, the user can explore the overall production process and learn how to make process improvements, thus building their domain knowledge. This can be especially beneficial for newer engineers who might previously have been reliant on the domain knowledge of others, who may be retiring. Workers can use a digital solution to learn about their factory and discover new ways to improve the manufacturing process such as understanding what the optimal temperature is for a certain step or what complex interrelated factors cause a particular quality issue.
Meanwhile, maintenance teams at factories in all kinds of industries, from chemicals to cement, can employ a digital solution to improve the overall health of their assets, freeing up the calendar of existing maintenance workers. With these teams in critical supply, intelligent asset health solutions can step in. By using sophisticated algorithms, they can predict when heat exchangers, reactive catalysts and other assets will no longer run optimally. Workers can then explore root causes of degradation to find the optimal maintenance window, discover when a machine is likely to decline and what factors can prolong its lifetime and delay maintenance as long as possible. As a result, the technology relieves the burden on employees who may be in short supply.
Finally, let’s not forget that the labor shortage also extends to data scientists. These teams are valued by companies for being able to take the thousands of data points generated each moment by factory sensors and interpret them to produce actionable recommendations. With data scientists in short supply due to the ongoing labor shortage, managers at an industrial company may well fear that there are fewer experts capable of interpreting the data they are continuing to generate every day and using it to optimize the process, which could mean missing out on profits and losing out to the competition.
As in the previously mentioned use cases, digital technology can come to the rescue, empowering existing data scientists by taking many tasks off their plates. Specifically, it can automate tasks like rote data analysis and manual data processing and cleaning, so they can spend their work hours exploring more significant problems involving the factory’s plethora of data. Furthermore, if a company is in the position of having no data scientists at all to investigate a particular problem, whether for budgetary reasons or because of the labor shortage, a machine learning solution can even ingest all the data generated on the factory floor and determine the optimal settings to make production more efficient in real-time, essentially turning engineers and operators into data scientists.
Digital solutions aren’t only for individual roles. They can also be used to benefit overall collaboration within a manufacturer’s workforce. For example, the collaboration between engineers and data scientists traditionally requires significant back and forth, which is only worsened when one or both of those roles is in short supply. With a digital solution, experts in a given area of the factory can enter their expertise directly into the software without engaging back and forth with data scientists, thus making the overall collaboration more seamless for everyone involved.
The overall picture of American manufacturing’s labor shortage picture may seem bleak. It is true that many workers are retiring and the trend shows no sign of letting up. However, by taking the necessary steps to address it through harnessing today’s digital solutions, companies can empower their existing employees and perhaps attract newer generations to change their point of view to see factories as the workplace of the future.