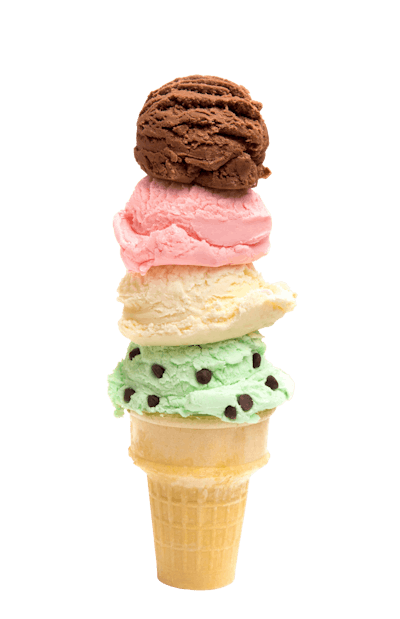
Blue Bell Creameries was founded in 1907 and is now one of the top ice cream manufacturers in the country. The company is committed to its customers and to making ice cream with the most delicious and highest quality ingredients. With four manufacturing plants and 57 distribution centers, Blue Bell sought a mobile data collection software partner that could keep up with busy operations.
Challenge
Blue Bell had been using Oracle E-Business Suite 11i environment for its existing automated data collection solution and decided to upgrade to Release 12 to overcome workflow issues and improve overall functionality. During the transition, the Blue Bell team discovered that Release 12 also created unexpected challenges.
These new challenges included maintaining compliance as it related to tracing food ingredients and products, unreliable handheld device connectivity inside its facilities, the need to adapt to multiple types of mobile devices and tracking fixed assets via paper-based systems.
Solution
To overcome the obstacles with the enterprise resource planning (ERP) upgrade, multiple operating systems, delivery logistics and solution scalability, Blue Bell sought a software partner with robust, flexible and customizable solutions. Blue Bell tapped RFgen and deployed RFgen Mobile Foundations for Oracle E-Business Suite, a powerful, flexible and cost-efficient solution.
The software suite enhanced operations by implementing mobile barcoding in receiving, inventory, manufacturing, quality and fixed assets. It also replaced Blue Bell’s legacy barcode system as they transitioned to the new release of Oracle e-Business Suite.
“We quickly realized RFgen’s solution would not only solve our mobile batch requirements, but would also provide real-time integration to our Oracle E-Business system to manage the shop floor transactions used in our plants,” says Jim Kruse, board secretary and controller for Blue Bell.
Results
Not only had RFgen helped Blue Bell make a smooth transition to Oracle E-Business Suite Release 12 without losing functionality or data collection capabilities, but the company also remains highly satisfied with RFgen’s reliability and performance. RFgen proved to be the right solution for Blue Bell’s challenges, offering continued scalability and seamless integration across multiple offering systems.
Blue Bell employees are now using RFgen to receive ingredient inputs from vendors on the load docks using handheld barcode scanners that quickly scan information from purchase orders. On the inventory and production side of the house, the scanners are being used to do cycle counts, keep accurate inventory in real time and track inputs going into product batches.
“RFgen handles our inputs, outputs, returns and also some quality control transactions on the handheld,” says Kruse. “All of the lots going into this system are tied together with quality information as well as receiving adjustments of inventory, inputs into batches, returns back to inventory and outputs that are basically a WIP completion or a finished intermediate item such as a mix, chocolate or cookie. There’s no way we could collect so much data without the RFgen mobile platform.”
RFgen solved one of Blue Bell’s most frustrating issues with their previous vendor -- data drops. The prior solution had a bad habit of dropping its connection with handheld devices.
“The inventory guys would then have to go and find the pallets that they already stored in the racks,” says Clint Eilers, cost control analyst at Blue Bell.
Warehouse employees then had to re-scan all the items on the pallets and hope the connection wasn’t dropped a second time.
RFgen implemented a mobile fixed asset solution that allowed the company to upgrade to a digital paperless process. This process offered a solution to Blue Bell’s complex logistical delivery challenges. The system also helped the customer’s delivery system of over 800 truck drivers manage Blue Bell fixed assets located at thousands of branch and customer sites with drastically greater efficiency and accuracy. Drivers no longer performed manual calculations or modifications to paper-based forms, minimizing time delays from miscounts and human error.
Key achievement summary:
● Increased productivity and improved data accuracy by utilizing handhelds for cycle counts.
● Resolved data drops with trusted and reliable offline data collection and higher quality handhelds.
● Significantly enhanced fixed asset tracking.
● Helped over 800 truck drivers manage Blue Bell’s fixed assets located at thousands of branch and customer sites with greater efficiency and accuracy.
● Equipped Blue Bell’s in-house developers with the ability to customize transactions and workflows in a fraction of the time and cost of the previous solution.
● Seamless training support.
Looking ahead
As Blue Bell continues to grow and their needs evolve, the company continues to assess the ways they can continue to leverage the power of RFgen’s offerings. Other possible applications include exploring how the continuous availability batch mode can be used to improve route accounting for delivery of ice cream products to supermarkets and convenience stores.
“We have a lot of ideas for RFgen based on its scalability. I have a feeling it’s never going to end,” says Blue Bell’s program analyst Vitalina Lisovaya.