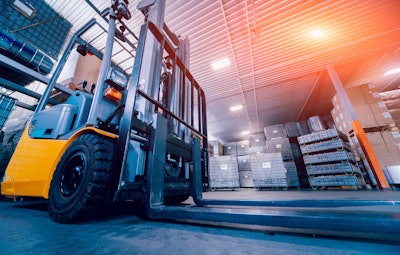
There have been few historical events that have had a greater impact on the food and beverage industry than the Coronavirus disease (COVID-19) pandemic. COVID-19 has brought novel urgency and complexity to how companies remain agile in the face of food item shortages or demand fluctuations in grocery products, all while ensuring a safe working environment.
The act of balancing increased efficiency, agility and worker safety is also occurring at a time of unprecedented change in consumer expectations and behaviors in the grocery space, forcing companies to increase supply chain flexibility and resilience to meet ever-changing demands in response to the pandemic.
As food and beverage professionals begin to consider what operations might look like on the other side of the pandemic, it’s a good opportunity to look past adjusting to the “New Normal” and consider what processes can change for the better. In many ways, the pandemic has become an accelerator or catalyst for positive change, forcing companies to re-examine, re-focus or fast-track existing or new operational initiatives, like curbside pickup or same-day delivery.
Following are five actions that food and beverage warehouse managers can take to help enhance efficiency, safety and flexibility during the pandemic, while also better positioning operations for continued performance gains and success beyond.
- Adjust and standardize processes and procedures
Take a look at your existing processes and procedures, especially those focused on health and safety. Determine what may need to be adjusted for today’s environment and identify where you may have gaps that need addressing. For instance, COVID-19 has brought hygiene front and center, leading to new policies across workplaces, including warehouses and distribution centers.
Warehouses and distribution centers should consider the need for a structured cleaning program for their forklifts and other material handling equipment. Relying on operators to clean the equipment before or after their shift is not always efficient and is only effective as long as they remember to do so, while following the standard protocols. It may be worth checking with your forklift provider to see if they offer a forklift cleaning service. They may even be able to schedule their onsite technicians to regularly clean equipment between shifts, leaving your operators more time to focus on productivity and efficiency.
Additionally, take a look at your existing training program and see how any new safety procedures or requirements should be incorporated. New health and safety initiatives, such as sanitization and social distancing efforts, can be explained and reinforced within the structure of your existing program.
- Keep up with routine service and planned maintenance
When it feels like operations are moving a mile a minute, service and maintenance can often fall to the back burner while other priorities, like keeping in-demand grocery items stocked, are addressed. It’s important to resist the temptation of putting off routine maintenance to keep lift trucks in top-working condition. Keeping fleet well-maintained will ultimately increase productivity and support overall warehouse safety.
Utilizing a fleet management tool can help you keep tabs on overall fleet health, as well as track maintenance records to keep service events on a regular schedule. Including these types of tools in your daily operation will enable you to proactively plan for vehicle maintenance, replacement or retirement, without negatively impacting productivity or uptime.
- Understand forklift fleet utilization
In “normal” times, you should understand how and when your forklifts are being used. Today, this understanding is even more critical as COVID-19 has reminded us of the importance of preparing operations for unexpected product shortages and delays, as well as shifting consumer expectations and demands, like the rise of e-grocery.
At any given time, knowing how many forklifts are in operation or sitting idle can be extremely valuable in right-sizing your fleet and shifting equipment where it’s needed. Armed with this information, you can make informed decisions about the number and types of forklifts you have and better manage your resources. You can determine if you need to rent or buy additional trucks or simply reallocate certain ones within your organization. You can also more accurately project how many forklifts you need at each facility during typical peak seasons or timeframes.
The key is making decisions based on data. Utilize a fleet and operator management system to gain visibility into an array of fleet and operator information, including forklift utilization. The connected technology can give you invaluable, actionable data on how and when trucks are being used, so you can ensure operators are achieving similar levels of productivity and safety as well as determine if the fleet is sized properly for efficient performance. It will also better prepare you to manage unexpected fleet allocation challenges.
- Leverage available technology solutions
Automation and energy solutions can play a critical role in increasing efficiency and productivity, especially when it comes to cold storage environments.
Utilizing lithium-ion batteries can often result in increased performance and longer runtime, and cold storage environments are no exception. Lithium-ion batteries offer greater energy efficiency over lead-acid batteries, especially in cold environments where traditional lead-acid batteries can often take a significant hit in the frigid temperatures. Since they are maintenance-free, sealed units, the need for battery watering is also eliminated.
Another approach to leveraging technology is dual mode technology, which enables forklifts to switch between manual and automated operations, depending on the needs of the facility. Dual mode automation enables warehouses to take an incremental approach to deploying automation, with minimal supporting infrastructure and can function with or without a warehouse management system. Operations with cold storage environments are also considering automation to help limit time spent by operators of manual lift trucks in harsh, freezing temperatures.
- Utilize both vertical and horizontal square footage
At times throughout the pandemic, it felt like some grocery items just couldn’t be kept on shelves. During these moments of increased demand, it can be beneficial to reconsider how items are slotted throughout your warehouse to increase productivity and decrease pick times.
If you have less warehouse square footage, it can be beneficial to convert to a narrow aisle or very narrow aisle format, with reach trucks or turret trucks specifically designed for these environments working efficiently at height. By adding more bays or rows, warehouse managers can fully utilize floor space, an achievement that becomes even more significant when considering the cost of maintaining cold storage environments. Building up and not out to increase storage density within the existing space also eliminates unnecessary airspace that can cause cooling inefficiencies.
With food and beverage products moving more rapidly, it’s important to review slotting strategies to understand how slotting different products at different heights can ultimately benefit your operation. By utilizing lift trucks that can handle heavier loads at greater heights, you can spend less time re-slotting and considering optimized placement of faster or slower moving items, especially when it feels like demand is changing at every turn.
By focusing on these areas and making the needed adjustments, you will show your operators and warehouse employees that you are committed to creating and maintaining a healthy and safe work environment. Additionally, you will help to prepare your operations to maintain the flexibility and efficiency needed to keep pace with ever-changing demands and customer expectations, regardless of what “normal” may prove to be.