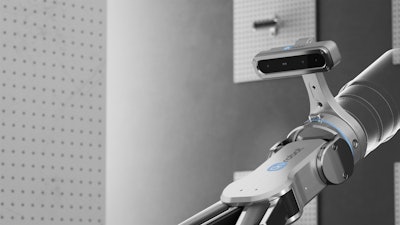
Adding a machine vision system to your operations can provide several benefits for food processors, including enhanced productivity and product traceability, improved quality outcomes and streamlined use of existing machinery and automation.
In safety inspection applications, for example, machine vision can be used to identify foreign materials and contaminants in food packages, to check for damage to packaging, to sort, grade and portion food items and to check for color and potential spoilage – important capabilities in a strictly regulated sector with an extremely low tolerance for error.
Vision systems can also be used to track food products throughout a processing facility. For example, a machine vision that reads barcode information can help processors accurately track and trace products from the moment of arrival to their departure, in a correctly labeled box.
Additional uses for vision systems in food processing plants include checking fill levels, inspecting seals, verifying date and lot information, identifying damaged packaging and ensuring that products are a consistent size and shape.
The global machine vision system market size is projected to reach $74.9 billion by 2027, at a CAGR of 11.3%, with adoption among food processors a significant component of this growth.
But, with a myriad of vision systems available, what qualities should food processing facilities look for?
Choosing the camera
At the center of every vision system is its camera. In fact, the system’s camera is the main influence on the cost --and ultimately, the complexity—of the overall deployment, so it’s important to make the right choice. There are three main types of cameras used in machine vision systems -- 2D, 2.5D and 3D.
2D cameras are the least capable. Typically, 2D cameras determine length and width (X and Y axis), but are unable to determine height, which severely limits the number of applications they can support.
3D camera-based systems provide a wealth of data, but for the overwhelming majority of applications, investment in 3D camera systems is expensive overkill. Additionally, 3D camera-based vision systems are complex to set up and maintain, and typically require a degree of technical expertise that’s beyond the in-house capabilities of many food processing companies.
2.5D-based systems, on the other hand, hit the perfect balance between cost and complexity. 2.5D provides the essential depth perception required to perform important tasks in food processing facilities.
For example, a 2.5D camera-based vision system deployed on a packaging inspection task can provide the depth data needed to determine how many items have been stacked in a box, enabling processors to ensure that every box is packed with the correct amount of product, every time.
With food processors facing the challenge of maintaining high standards in a highly regulated, low-margin sector, 2.5D camera-based systems make the most sense in terms of cost and performance.
However, not all 2.5D camera-based systems are the same. Let’s take a look at the key features that differentiate various 2.5D vision systems from each other.
Calibration
Before your vision system can be deployed, it must be calibrated. Depending on the system, this can be a tricky and time-consuming process, so look for systems that offer one-shot calibration. One-shot calibration features mean that the camera can calibrate itself on the basis of information supplied by one image, removing the need to fiddle around with multiple images and camera settings and dramatically lowering the barriers to a successful deployment.
Built-in color and contour detection
Look for 2.5D systems that provide software with easy to implement, built-in color and contour detection functionality. Especially useful in quality tasks, these features provide the information your robots need to easily sort, inspect, or pick and place unstructured objects, based on simple color and size information input by the operator. Systems without this functionality are much more difficult and time-consuming to operate and should be avoided.
Compatibility
Machine vision systems are often used to help maximize the performance of existing automation. With this in mind, make sure to invest in 2.5D systems that are compatible with the widest possible range of robot brands. This will ensure that your vision system remains viable should you decide to change your robot at some point in the future. To maximize your investment, avoid systems that are only compatible with one robot brand. Furthermore, invest in 2.5D systems that provide plug-and-play compatibility with the widest range of robots, as this will greatly simplify the deployment process.
Flexibility
Some vision systems are directly integrated into robot arms and others must be directly attached to a robot wrist or arm in order to function correctly. Both scenarios present serious limitations in terms of flexible deployment. Look for systems that can be mounted externally, separate to your robot as will maximize the number of potential ways in which the system can be deployed. For example, a well-positioned externally mounted camera could be used to check on the condition of the equipment surrounding food products, helping you to precisely time cleaning operations.
External mounting not only eliminates the issue of cables running alongside your robot, but it also allows you to optimize cycle time. While the vision system handles image capture and processing, the robot can work on another task.
Machine vision can improve safety and quality, support the demands of flexible production and help ensure compliance with industry regulations. Thanks to improvements in camera technology, particularly in the 2.5D range, and the parallel emergence of easy-to-use software, it is possible for food processors to add vision to their operations with minimum fuss.