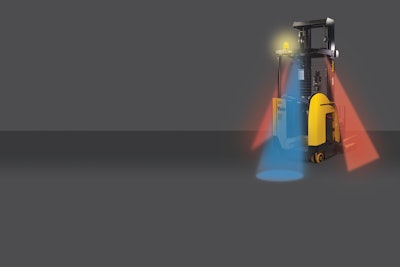
Even before the Coronavirus disease (COVID-19) pandemic disrupted businesses worldwide in 2020, supply chains were evolving quickly. New technologies are changing the way warehouses operate, helping manage more complex inventory due to consumer appetite for greater choice in frozen foods, beverages and other categories.
With operations adopting technology to address operational challenges, safety efforts must adapt accordingly. Safety requires constant focus and attention throughout the organization, especially as warehouse environments continue to evolve at a rapid pace. But, while technology can be a catalyst for process improvement, it can also present opportunity – opportunity to enhance safety training and adherence to proper procedure.
Training – virtual reality technology
OSHA estimates that approximately 70% of forklift accidents could be avoided with better adherence to standardized training and safety procedures. Operator training is a foundational element of forklift safety, as is complementary pedestrian training. But, warehouse operations are plagued by high turnover, regularly over 40% on an annual basis, and high turnover presents a large training burden as businesses bring new personnel up to speed.
Even before employees are hired and training begins, virtual reality simulators can be used as a candidate screening tool for employers trying to fill vacant lift truck operator positions. Once new employees are brought onboard, virtual reality simulation can offer a primer that helps decrease the learning curve for new hires and can help improve the consistency of lift truck training between facilities.
Although not a replacement for on-truck training, virtual reality simulators enable operators to practice lift truck operation in an immersive environment. This approach offers valuable experience that can help operators prepare to execute tasks and share environments with pedestrians without taking an actual lift truck out of service or risking damage to equipment, facility infrastructure or oneself.
Data-driven accountability
Equipping lift trucks with a telematics system can help further enhance safety and training efforts. One important feature of telemetry is the ability to restrict truck access to only operators with proper certification for that truck type. Every operator must swipe an individual access card with certification information encoded, or else they cannot start the equipment. The system also provides notifications when operators have certifications expected to expire shortly.
Telemetry tools include sensors affixed to gather data on lift trucks, including hazardous driving behaviors, such as excessive speed or impacts. This data can be tracked according to individual operators, adding an extra layer of accountability for ineffective, unsafe drivers while incentivizing high-performing employees. For an even greater level of detail, truck-mounted camera solutions are available to capture footage immediately before and after any lift truck impact. Having access to this kind of rich information allows organizations to isolate and make decisions to work on remediating problem areas and reinforce ideal operating practices to increase safety.
A telemetry system can also be used to limit truck performance based on operator experience and skill level. For example, new hires might have their trucks capped at slower speeds to help reduce potential risk while more experienced operators can still operate the same truck at levels that allow maximum performance.
Lights keep operators and pedestrians aware
Whether navigating dark trailers or dimly lit freezer areas, lift truck operators commonly encounter environments with low light. To help increase visibility so operators can perform with precision, speed and confidence, warehouses can take advantage of truck-mounted lighting solutions. For example, work lights installed on masts and rear work lights can provide targeted illumination whether positioning forks or traveling in forward or reverse directions.
But, assisting operators as they work is only part of the benefit of truck-mounted lights. Pedestrian safety and forklift safety go hand in hand. In fact, it is beneficial for all employees to review portions of the forklift operator training that address pedestrian safety. In addition to warning signs in areas where lift trucks operate, lights can provide an effective means to grab attention and inform pedestrians of the presence of powered equipment.
For example, blue LED spotlights cast in front of or behind a truck’s directional travel path, red zone lights projected onto ground level around the truck perimeter and top-mounted strobe lights all help notify those in the area of approaching trucks. Audible alarms also help notify pedestrians and other lift truck operators of equipment in close or immediate proximity. They even automatically self-adjust to five decibels louder than any surrounding ambient noise, eliminating the need for constant manual adjustments.
Robotics and safety
The aforementioned labor challenges facing food and beverage operations work to drive greater demand for robotic solutions to take on repetitive tasks. For example, robotic lift trucks can be assigned repetitive transportation and retrieval tasks, such as picking up pallet loads from conveyor lines or staging areas and bringing them to storage or out to shipping docks.
Robotic lift trucks are also engineered according to specific safety standards, such as ANSI B56.5. They are programmed to move around every physical structure in warehouses, and travel at controlled speed and acceleration. They move through complex warehouse footprints, avoiding columns, racks and walls, and can even safely cross pedestrian paths. In fact, they keep a greater distance from pedestrians and structural features than human-operated forklifts.
Everyone in warehouses should be trained on how to properly interact with mobile robotics. The “rules of the road” are different from the guidelines for traditional equipment with human operators, and they must be clearly defined. While robotic lift trucks have sensors and systems designed to prevent impacts, warehouse workers, supervisors and guests can be unpredictable, which makes clear explanation and enforcement of rules even more important.
Every change can have an effect on safety
Food and beverage distribution operations are more advanced than ever. And, in a fast-evolving industry, process changes and technology updates are common. But, while these may be adopted to meet performance targets or respond to labor challenges, they can still have an effect on safety. Careful evaluation of technologies and their specific application can enable managers to properly address operational and safety impacts for lift trucks and personnel.