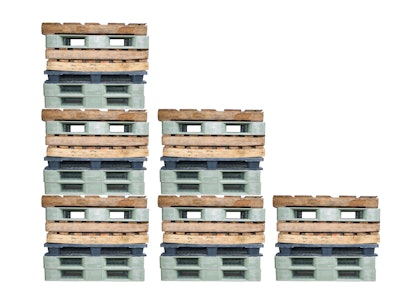
Proper handling and packaging are essential for food and beverage supply chains to function. Consumers depend on reliable handling throughout the supply chain to ensure the food on their plates is safe to consume. They often are unaware of how food moves in the supply chain. But what happens when the packaging used to move, store and transport food doesn’t meet expectations? Spillage and contamination are all-too-real risks in the industry and can pose serious hazards to consumers if preventive measures are not enforced.
Cleanliness and allergen management have long been top checklist items for food and beverage supply chains, but the Food Safety Modernization Act (FSMA) has caused re-evaluation of handling processes and systems in order to prevent contamination. These regulatory changes, combined with consumers’ fascination of knowing where their food comes from, have pushed transparency and innovation in food and beverage supply chains.
Now, more than ever, suppliers are motivated to re-evaluate their systems and the materials that come in contact with goods, creating an increased need for packaging that helps minimize contamination risks. Food processors and their suppliers are considering cleanable, reusable packaging to support FSMA requirements and to increase consumers’ confidence.
Using Reusable Packaging for a Cleaner Supply Chain
Reusable packaging products, like plastic pallets and totes, are essential for reducing the risk of unsanitary contact and ensuring consumers are provided with food and beverages that were handled with care during storage, transportation and warehousing. Reusable packaging offers a variety of benefits, including easy cleaning, allergen management, detectability, color coding, labeling and traceability.
Many food processors and suppliers are now switching from expendable packaging—such as wood pallets and corrugated fiber boxes—to plastic packaging for sanitary reasons and to avoid efficiency roadblocks. For example, a dairy manufacturer made the switch to plastic pallets because shavings, splinters and other residue from wood pallets required them to shut down their lines every three days for cleaning—exhausting four hours of activity each time. Reusable packaging helps prevent this residue and is standardized for more fluent movement through automated systems.
A Peerless Media Group study found that, although more than 90% of companies still use wood pallets in some form, 37% use plastic, and some have almost entirely replaced wood with plastic. More users are switching to plastic because wood pallets cannot always meet the same level of performance and consistency due to the material’s inherent ability to absorb and retain moisture and odor. Used wood pallets are often shared or repurposed, so it’s difficult to know what has permeated into them in previous cycles.
Wood and plastic pallets were recently put to the test at the Virginia Tech Center for Packaging and Unit Load Design. It conducted a comparison study that revealed plastic pallets completed more than 200 cycles without failure, compared with wood pallets that completed—on average —11 cycles before failure. Reusable plastic pallets are not only durable, but are also available in hygienic designs, which allow for proper cleaning and can help minimize the risk of food and beverage contamination before it’s too late.
Hygienic plastic pallets, for example, are made of nonporous material that cannot absorb moisture, odor or mold, and they don’t have cavities or hollow areas for water to collect. They’re easy to clean and dry, and their contoured surfaces and corners lower the risk of punctured goods and cases. These plastic pallets also are available in a range of sizes, styles and risk-reducing materials to accommodate most supply chains. Available in custom colors, these pallets provide a more visual way to store allergens like eggs and nuts to support allergen control and management. With the FSMA regulations in mind, companies should strongly consider hygienic plastic pallets, if they haven’t already.
Management Best Practices for Reusable Packaging
To best ensure a clean container or pallet, it is crucial to have a process to track, retrieve, clean, return and inventory reusable packaging. Reusable packaging management can help ensure reusable packaging is reinserted into the supply chain properly, improving food safety and providing an opportunity for traceability if problems arise in a supply chain.
A reusable packaging program is only as strong as the way it’s managed. Companies have the most success implementing reusable packaging when the program is paired with a dedicated management team. This team may include company decision-makers, as well as third-party resources that specialize in managing reusable packaging and know how to efficiently analyze the data. Utilizing a third-party management provider also allows companies to avoid burdening their current, already busy workforce, so they can focus on their core business.
Benefits of robust packaging management include:
Proper handling that leads to a long service life. The development and implementation of these programs allow for proper handling and increased product service life. The protocol helps today’s food and beverage suppliers “keep eyes” on handling and manage the complexities of transporting, tracking and servicing packaging materials.
System efficiencies. Reusable packaging is a catalyst for implementing a lean manufacturing system, where frequent on-demand deliveries, standardized package sizes and efficient packaging processes improve the flow of product and reduce the need for extra storage or warehouse space. The standard lightweight design of reusable packaging allows product to travel safely and efficiently to its destination.
With dock and driver time at a premium, trailer loading and unloading efficiency is key. A process focused on accurate tracking of empty reusable containers reduces mistakes and creates accountability and trust between shippers and receivers.
Improved asset tracking that provides visibility. Knowing the status of products along the supply chain and where they are located is imperative for operational efficiency within the food and beverage industry. As the technology becomes more common, reusable packaging manufacturers are finding ways to use sensor technology, like RFID or GPS, for improved asset tracking. By tracking packaging throughout its lifetime, comprehensive data like dwell time, environmental conditions and the like, can be collected for real-time decision-making, preventing spoilage, product damage or supply chain lags.
Analyzing this data leads to well-rounded insights that are often more difficult to gather from one-time-use packaging. Armed with this data, companies can trace whether a product has been diverted—or otherwise tampered with during transportation and storage.
Strong Benefits of Reusable Packaging With Every Use
It’s no surprise that cleanliness and the risk of contamination can keep food and beverage suppliers awake at night. But with today’s packaging innovations, keeping your supply chain safe and sanitary is becoming increasingly easier and more efficient.
Reusable packaging has become an essential piece of the supply chain for food and beverage companies looking to gain and keep public trust. This packaging is reliable, cleanable and allows for improved traceability and asset tracking.
Particularly for food and beverage supply chains, reusable packaging can help minimize the risk of contamination and potential financial—and reputational—costs of food recalls. But most importantly, reusable packaging is a reliable method to move product in the supply chain and can provide confidence to today’s consumer that their food will arrive safely.