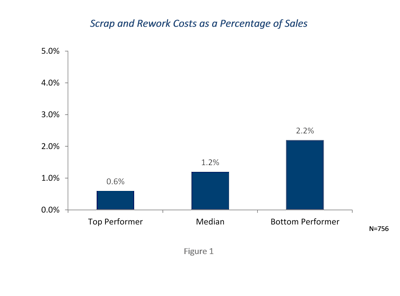
Scrap and rework is defined as material that is added into production but is not part of a finished product. Because the cost of this scrap material does not add value to the organization, it gets included in the calculation for the total cost of quality, or poor quality. This measure sums all costs associated with poor quality or product failure, including rework, scrap, warranty costs and other costs incurred in preventing or resolving quality problems.
As Figure 1 shows, top performers spend 0.6 percent of sales on scrap and rework, compared to bottom performers who spend 2.2 percent. For an organization with $2 billion in annual sales, that is $32 million a year being wasted on scrap and rework that could be better spent elsewhere in the organization.
Even the top performing organizations are not able to get down to zero percent for scrap and rework. Therefore, these organizations implement production schedules that integrate lost time due to scrap, rework and retesting. As a baseline, though, they also ensure that documented, consistent processes and practices are used to drive consistency in production output. Another key practice is ensuring that any manufacturing or engineering changes are clearly communicated throughout the supply chain.
Top performers also improve performance by applying quality management techniques to reduce defects and costs related to scrap and rework. One proven tactic is taking a “5S” approach, a lean manufacturing tool that improves workplace efficiency and eliminates waste. Another is implementing Kaizen methods. Kaizen, the Japanese term for improvement, refers to small-step continuous improvement focused on finding and eliminating waste
For organizations that have outsourced manufacturing to a third party, it is critical to ensure accurate and complete documentation is provided for all products, including drawings, datasheets, work instructions, bills of material and other details. Inadequate documentation and instructions can lead to rework and scrap.
In addition, to ensuring manufacturing processes are lean and in control, quality methods are deployed and outsourced manufacturers are on the same page, it is also useful to look at possible supplier issues and correct any problems at the source to avoid issues later in the supply chain that could result in scrap and rework.