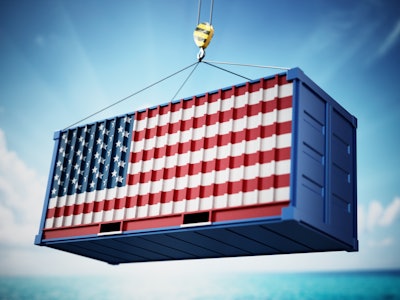
Organizations today need a comprehensive sense of global and marketplace factors that could potentially disrupt procurement and sourcing, as well as the supply chain as a whole. Given all the moving parts that organizations need to consider—from the marketplace, governments, environmental and social concerns, third-party logistics providers, customers and more—risk monitoring technologies are becoming more critical than ever.
Even the savviest organizations have sophisticated risk monitoring systems that provide important intelligence not only for supplier risk, but also for second- and third-tier supplier risk as well. Plenty of other organizations, however, are taking on unnecessary risk by not having any risk monitoring systems in place at all.
Tracking external factors
In many respects, monitoring supply chain risk is a data management challenge. Data inputs can include news alerts, customer feedback, weather forecasts, legal filings, and more, and the status of these inputs can shift by the second. A good monitoring system must be able to aggregate and normalize a vast number of these inputs and monitor them based on organizational concerns and priorities. Best-in-class systems also include embedded analytics that provide insights on the probability and severity of each risk and provide automated alerts for any outlying trends.
APQC research found that many organizations still have an opportunity to adopt technology to monitor supply chain disruptions and capture risk profiles. About one-third of surveyed organizations lack these systems completely, leaving them vulnerable and slower to react to unforeseen disruptions.
Another one-third have systems, but do not provide any information on the potential impact of disruptions to the organization. For example, these organizations might be aware of severe congestion at various ports around the world, but without a time-consuming investigation, they have no way of knowing exactly what it means for them or their suppliers. Procurement teams in these organizations at least have a foundation upon which they can build. Collaborating with enterprise risk management and IT functions can help them to leapfrog in terms of data management maturity as they implement more sophisticated risk monitoring systems.
Organizations that lack these systems completely will only be able to react to disruptions once they have occurred, and even those with systems that provide basic monitoring (but no information on impact) may lose valuable response time. APQC research finds that the largest share of respondents (40%) report that it takes them one day to identify impacted materials, sites, commodities or products in response to a supply chain disruption. Nearly 30% of organizations take one week, and 20% take one month or longer—a crippling amount of time for most industries.
When major disruptions hit, the difference in response time to activate contingency plans and move materials, sites, commodities and products as needed can spell the difference between success and failure for an organization. In line with the classic adage “time is money,” these response times do have a demonstrable impact on the total cost of procurement. Organizations that report the ability to respond to disruption within minutes spend $19.79 per $1,000 purchases on procurement, while those that take one month or longer to respond spend $23.32 per $1,000 purchases. This means, for example, that for every billion dollars in purchases, the slowest organizations will end up spending more than $3.5 million dollars above what the fastest-to-react organizations spend for procurement.
Some monitoring systems can create risk profiles of suppliers, materials, supplier manufacturing sites, categories and products. These systems give organizations a comprehensive look at where components come from and create custom risk profiles not only for direct suppliers but also for second- and third-tier suppliers. More than one-third of respondents say their organizations are not currently using these systems at all, either because they have no plans for one or because they are in the process of developing one in-house.
The 19% of organizations that have a well-integrated system for proactive and reactive risk management are much better prepared for risk because they are positioned to address issues before they become problems and shorten response times to unexpected situations. For example, if a supplier is located in a disaster-prone region, these organizations will know and (if they are prudent) will have contingency plans ready before disasters occur.
Conclusion
Supply chain disruptions threaten significant risk for organizations that are caught unprepared. The good news is that the risk monitoring technologies available today can significantly reduce the time it takes for organizations to learn about disruption and respond to it. The best risk monitoring systems leverage capabilities like next-generation automation and predictive analytics, which not only speed up response times by alerting organizations more quickly, but also help reduce the time that humans need to spend tracking and monitoring data. As a result, organizations that invest in these systems have more time to think strategically about procurement and can put plans into action more quickly when disruptions hit the supply chain.