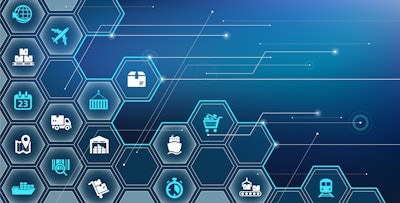
Most supply chain planning solutions are designed to plan and then react to just a limited number of events such as supplier delays, equipment breakdown or demand fluctuations. There is so much more happening locally and globally that can impact the operation of the supply chain and create havoc. Consider, for example, port delays, weather issues, geopolitical changes, natural disasters, or even the company’s website visits. Depending on your supply chain, any of these events can have a substantial impact on your operations resulting in hundreds of millions of dollars of losses every year for companies around the world.
A simple delay in arrival of raw material or components can impact production, missed delivery to customers, lost revenue or perhaps none of the above. The challenge is the ability to listen to such events, understand the impact and its consequences, if any, and correct or inform while learning from each event, in case there are patterns of occurrence. Blockage of the Suez Canal may not be a trend, however a supplier delay for a specific material during certain seasons could well be predictable.
Most of the current S&OP solutions are designed to do long-range rough planning and perform manual what-if scenario analysis in case something goes wrong. Their rough modeling also requires painstaking user intervention in order to make the plans just executable. They are unable to monitor relevant events in real-time, deficient in modeling capability to know what the many alternatives are and lack good enough intelligence to know how to respond. This results in painstaking user interaction to come up with solutions and proper response. The main problem is that they are too big and slow to handle the frequency and granularity of the events and be able to respond in real-time.
A different approach is needed in the form of distributed and intelligent “sensors.” A distributed environment can monitor, or listen, to such events, act and learn from their experiences. The latter allows predicting likelihood of events in the future. The more predicting capability, the less reacting and responding is needed. The ability to predict brings about resiliency and agility. Supply chains are becoming more complex and faster. At the same time, disruptions are happening more frequently and more costly. For example, just weather problems alone in 2019 caused more than $1 billion in damages each. Let alone pandemics, geopolitical and socio-economical issues such as Suez Canal closure, tariffs and regional unfair labor practices. To this end, avoiding or mitigating increasing supply chain risk is the highest on every company’s agenda in addition to agility and sustainability.
In a recent research, it was estimated that that for a $10 billion company with a well-performing supply chain, that can “listen” and respond to events, has the potential to raise earnings by up to 2%, boost sales by $150 million and reduce costs by $50 million. Listening and the ability to respond seems to be the first step to not just survival, but also growth. A distributed architecture is intended to imitate human’s brain and the nervous system, evolved over millions of years. Our nerves very quickly respond to immediate danger, while the brain learns to avoid them in the first place.
For such an approach to work properly, the system needs to have enough built-in intelligence to know what events are relevant and when to respond, otherwise chaos may result, as witnessed with the Coronavirus disease (COVID-19), port delays and Texas freeze.
Each agent is agile and intelligent making the whole agile and intelligent. For example, a message from a supplier being two days late may or may not be as critical. By sending this message to the “planning agent,” it is interpreted and decided if this causes problems and delivery delays. A warning from a weather station regarding arrival of a tornado in Florida may not be relevant if the company has no supplier or customer in that region. Since each agent is representing a business process, it is possible to extend and embed the intelligence that is needed and having the ability to learn more as new patterns emerge using machine learning techniques. More importantly, as each agent responds, they also remember occurrence of each event and decide if patterns are forming. To this end, they can predict late arrival of goods (say) in winter, arrival of tornados in fall on the East coast or increase in demand of a new product in certain region. Detecting such patterns allows predicting future issues that can be avoided.
What to expect from technology and digitalization
- There are real-time streaming data regarding weather, natural disasters, geopolitical changes around the world and more. A number of companies provide services for delivering such data. They can be used effectively to mitigate supply chain risk and predict potential issues in the future.
- When it comes to supply chain planning systems, model accuracy and accurate capacity planning in particular becomes critical so that a true digital twin is built. A digital twin imitates the physical supply chain. To this end, the model has to be whole and the system must be able to make the complete representation. An accurate model provides reliable commit dates and true financial projections. In contrast, S&OP solutions show equipment capacities as buckets.
- Systems also need to have real-time collaboration capability with suppliers, their suppliers, customers and beyond. This can increase velocity of business drastically in the face of problems and issues that may arise daily. Collaboration can be automated using specialized distributed agents that can communicate with suppliers and interpret their messages. For example, they can check on order arrivals to ensure on-time delivery.
- Scalability of the system is also critical. Nowadays. it is not unusual to model hundreds of sites in a digital model. Having the ability to plan and respond to events in real-time is a major factor in avoiding supply chain disruptions. Otherwise just taking the signals and not being able to interpret, because of an incomplete model, or being too slow, make receiving data or listening a redundant exercise.
Supply chains have become progressively more sophisticated, complex and critical in the past two decades. Speed and resiliency are the key. Artificial intelligence (AI) and machine learning have provided the much-needed techniques to tackle these challenges to plan, predict and respond in real-time in the face of growing disruptions.
Click here to hear more about digital twin technology: