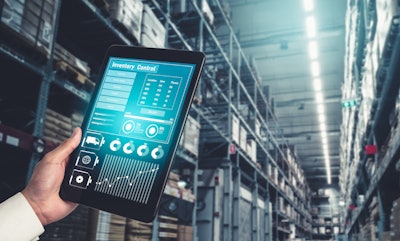
Smart manufacturing's value has been realized, with survey respondents reporting up to 20% improvement in production output, 20% in employee productivity and 15% in unlocked capacity, according to Deloitte’s Navigating Challenges to Implementation study.
Yet, while companies are realizing value in smart manufacturing investments from the past several years, many are still facing significant challenges in managing complex transformations as they contend with operational risks, talent shortfalls and cybersecurity preparedness.
"The smart manufacturing journey is still emerging, but its value is undeniable. Our survey shows that most responding manufacturers agree with the need to invest in smart manufacturing but require help navigating operational complexities to see meaningful results. Smart manufacturing prepares enterprises to be ready for increased demands and, in an era where increased capacity can set companies apart, organizations that have already invested in smart manufacturing solutions will likely have an advantage – those who haven't, may not be able to defer much longer," says Tim Gaus, smart manufacturing business leader and principal, Deloitte Consulting LLP.
Key takeaways:
· 78% of surveyed leaders are allocating more than 20% of their overall improvement budget toward smart manufacturing initiatives to build this foundation, including implementing clean data analytics, sensors, cloud, AI, etc. Looking at the next two years, 46% of respondents ranked process automation as the first or second priority investment, 37% ranked physical automation first or second and 24% ranked factory synchronization first or second.
· In terms of systems prioritized for investment, the first or second highest investment priorities are advanced production scheduling (35%), execution systems (33%) and quality management (28%). Investment in automation may be seen as an important element in alleviating skilled labor shortages and maximizing productivity, while factory synchronization may mitigate the impact of labor, asset and materials constraints.
· Close to half (48%) report moderate to significant challenges in filling production and operations management roles, and 46% reported the same for planning and scheduling roles. And, while nearly half (48%) of respondents reported having a smart manufacturing training and adoption standard in place, human capital was at the lowest maturity level of all smart manufacturing categories surveyed. Adding to this, as the nature of work fundamentally changes and people are now working alongside AI, more than one-third (35%) of those surveyed are concerned about upskilling their employees to work with advanced technology to realize the full potential of smart manufacturing and operations.
· Reported investment priorities over the next two years remain data focused, with 40% investing in data analytics, 29% in cloud computing, 29% in AI and 27% in the Industrial Internet of Things (IIoT). Regarding AI adoption, 29% are using AI/machine learning (ML) at the facility or network level, and 24% have deployed Generative AI (GenAI) at the same scale. Moderate investments are also being made in experiments and proofs of concept (POC). Twenty-three percent (23%) of respondents are piloting AI/ML, and 38% are piloting GenAI.
· Almost two-thirds (65%) of respondents ranked operational risk as the first or second priority requiring mitigation efforts in pursuing smart manufacturing initiatives. The risks include business disruption and losses stemming from change or failed initiatives.
· And, 40% of respondents have publicly reported 6-10 cybersecurity breaches in the past year.