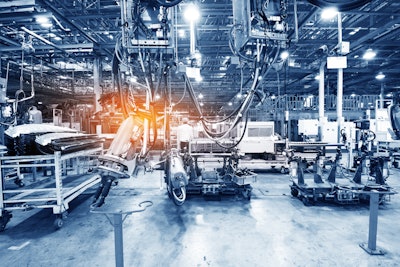
The holiday season is approaching, and manufacturers are again working to recalibrate strategies to align with a volatile and uncertain market. Anticipating a surge in demand always requires agility and foresight, but enduring challenges—like labor shortages, ongoing strikes, and external pressures from extreme weather and political uncertainties—are making the task all the more difficult this year. Though leaning into growth potential amid the coming demand surge is tempting, September's manufacturing metrics indicate signs of contracting production, adding a new dimension to Q4 planning.
In short, industry leaders are at a crossroads. To move ahead with confidence, they must develop a comprehensive understanding of the market trends likely to impact operations over the next few months.
Within Your Business
The holiday season presents both opportunities and challenges for manufacturers, as they strive to maximize productivity while navigating internal hurdles. With labor shortages persisting and consumer demand fluctuating, organizations must confront these pressing issues to maintain operational efficiency. Understanding the implications of these challenges is crucial for manufacturers aiming to thrive in a competitive landscape.
Labor Challenges
The labor shortage is still a formidable obstacle for manufacturers, with many organizations struggling to fill essential positions that drive productivity and innovation. Recent reports indicate that the manufacturing sector has experienced a significant workforce decline, projecting that approximately 2.1 million jobs will remain unfilled by 2030. This shortfall not only jeopardizes production capacity but also stifles innovation and hinders growth initiatives. As businesses gear up for the holiday season, the imperative to attract and retain skilled workers has never been more critical.
To combat this issue, manufacturers may want to start by revisiting upskilling programs. Investing in training initiatives empowers employees to acquire new skills and adapt to evolving technologies. This approach not only addresses labor shortages but also fosters employee loyalty and engagement. Collaborating with educational institutions may also help, as strategic partnerships with community colleges and vocational schools can lead to tailored programs that align with industry needs, ensuring a pipeline of skilled talent.
Demand Changes
As the holiday season approaches, manufacturers must be ready to meet heightened consumer demand—without overproducing or straining their facilities. They can do this by leveraging advanced analytics and demand forecasting tools to anticipate consumer needs.
Predictive analytics tools utilize historical data to identify future demand patterns, allowing businesses to optimize production schedules and inventory levels. This is essential for meeting anticipated demand without overextending resources. Manufacturers should invest in inventory and material management systems that provide real-time visibility into stock levels.
Beyond Your Four Walls
As manufacturers navigate the complexities of the holiday season, it’s essential to control what you can and prepare for what you can’t. External challenges, such as extreme weather and supply chain disruptions, require proactive strategies to safeguard operations.
Extreme Weather
The manufacturing sector is increasingly vulnerable to extreme weather events, which have the potential to disrupt operations significantly. Recent hurricanes and wildfires have highlighted the need for robust contingency planning, and the majority (80%) of manufacturers say that improving resiliency is now a top priority. Many hope to do so by investing in infrastructure that’s built to withstand severe weather and developing risk management strategies to get ahead of disruptions.
To do either, manufacturers will need to assess the unique challenges within their supply chains to design contingency plans that are specific to their operations. This may include diversifying suppliers, investing in resilient infrastructure or establishing backup production facilities in less vulnerable regions.
Shipping and Transportation Troubles
Internal staffing isn’t the only people management issue that affects manufacturers. Widespread labor strikes in other areas of the supply chain—such as the one by the International Longshoremen's Association (ILA), involving about 45,000 dockworkers striking at key ports from Maine to Texas underscore the vulnerability of our manufacturing infrastructure to external incidents.
While manufacturers might have plans in place to accommodate these disruptions, the sooner they activate on those plans, the more likely they are to succeed. As the holidays draw nearer, manufacturers must devote time to opening lines of communication with suppliers and shipping partners, so they get as much advanced notice about pending issues as possible.
Material Shortages
Despite raw materials shortages easing over the past year, manufacturers still grapple with the threat of material shortages that hinder production and extend lead times. McKinsey’s recent report on the raw materials market found that, while key material supplies are scaling quickly, demand for these materials is likely to scale faster than production. As a result, balancing supply chains may continue to be challenging for manufacturers—and prices are likely to rise in in the coming years.
To accommodate this volatility, manufacturers should focus on strengthening relationships with suppliers to ensure priority access to materials, which can help secure supply continuity. They may also want to revisit their buying and storage plans to buffer against supply chain disruptions, especially for high-demand items.
Adjusting for Agility
What’s apparent amid all of the above is that, in today's rapidly changing environment, the ability to pivot quickly in response to demand fluctuations or supply chain disruptions can mean the difference between success and failure. Adopting agile manufacturing principles can enhance flexibility, enabling companies to streamline processes and reduce waste. However, the power of an agile supply chain is in the preparation.
While there’s still time to spare ahead of the season’s busiest days, manufacturers will want to consider the above market factors and contextualize them against what they already know about their businesses. They must dive into their data, champion collaboration, call for cultural change, and channel all of that into contingency plans that are ready for what’s to come.