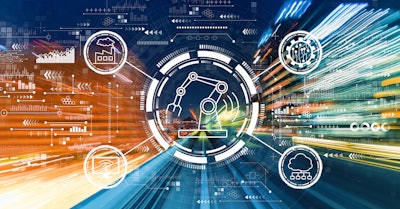
For too long, it has felt like only larger manufacturers can afford to modernize and digitalize while smaller organizations have been priced out and left behind. The increased availability of manufacturing technology means that despite misconceptions, digitalization is becoming more accessible. More and more organizations are adopting technology that allows them to uncover new efficiencies without entirely overhauling their processes.
Manufacturing leaders should address four key trends in 2025. Regardless of the size of the organization, these trends can be applied by integrating new technology with existing processes.
Trend 1: Digitalization on the Shop Floor
As digital solutions become more affordable and scalable, even smaller manufacturers are starting to embrace digitalization on the shop floor. There are many ways to do this, from adopting cloud-based systems and IoT devices to implementing more sophisticated simulation technology like digital twins.
This shift improves efficiency, reduces errors, enables real-time data access and enhances productivity without requiring significant investments. It also empowers smaller organizations to innovate and better compete with larger organizations.
Until now, perceptions about the high cost of new technology and infrastructure have meant that many organizations are put off digitalization. However, there are ways to address this. For instance, to reduce the upfront investment required, organizations should consider phased implementation to spread out these costs over time. By targeting efforts on lightest lifts rather than the highest return initiatives, early wins can fund future phases of digitalization. Organizations can also seek government grants and incentives to help fund digitalization across the organization.
The labor shortage across the manufacturing industry is another concern for organizations looking to increase digitalization on the shop floor. Exploring partnerships with educational institutions to develop a pipeline of skilled workers and investing in training and development programs to retain existing employees can help mitigate this issue.
Finally, implementing cybersecurity measures, a training program for employees, and regular audits can address security concerns. For instance, some solutions allow manufacturers to maintain on-premises infrastructure while still reaping the benefits of the cloud. The majority of cloud-based solution providers provide cybersecurity support as part of their solutions, thereby reducing the burden on the manufacturer and lowering the barrier to entry for smaller shops with tighter budgets.
Trend 2: Going Paperless
As it stands, 42% of manufacturing leaders say that they face difficulties in data sharing between teams, according to a survey by Hexagon and Forrester. Going paperless is one of the most effective ways to help teams and employees across the plant to communicate and share information more easily. It improves efficiency and productivity and reduces the risk of errors by providing increased oversight and control over document management systems. Going paperless allows manufacturers to capture and digitalize historical knowledge, which can be democratized across the organization, leading to quicker problem solving and allowing for faster on-boarding of new hires.
Going paperless can feel intimidating, but it doesn't have to be done all at once. Small shops can transition gradually by creating a roadmap that allows them to avoid disruption to current processes.
Using digital twins to simulate various scenarios and test improvements can help validate the roadmap and address any potential data integrity concerns before it is finalized. As the transition progresses, the cost savings and waste reductions will become apparent.
Trend 3: AI in Manufacturing
AI is reshaping every organization, and manufacturing is no exception. Integrating AI into the manufacturing process opens new doors by enabling predictive maintenance and automated inspections. This drives quality control and supply chain optimization, which results in lower costs and quality improvements across the organization.
While using AI in manufacturing presents many benefits, it also introduces a new set of challenges. For instance, getting AI systems to function effectively requires a significant amount of high-quality data. To ensure this data is as accurate and error-free as possible, organizations focus on implementing strong data cleaning, management and governance practices.
Another key challenge is integrating new AI technology with legacy systems used widely throughout the industry. Thankfully, this is becoming less of an issue as AI tools become increasingly compatible with existing infrastructure. Today, manufacturers can phase their digital transformation approach by using middleware solutions to bridge old and new systems. Organizations should focus on integrating scalable AI applications that provide immediate benefits and don't require significant training or system overhauls.
Regardless of the simplicity of the AI technology that is implemented within the organization, managers need to provide employees with the required training to empower them to use the tools with confidence and reduce errors.
Trend 4: Simulation Technology and Prototyping
Simulation technology can create virtual replicas of physical objects, processes, or systems. It can also reduce manufacturing costs and improve efficiency by allowing organizations to create virtual prototypes, optimize processes more efficiently, and monitor equipment in real-time.
Digital twins are a specialized type of simulation technology being adopted across many industries, including manufacturing, healthcare, and urban planning. They can continuously integrate and analyze real-time data from other real-world objects, which helps to quickly identify issues and mitigate risks before they occur. Their ability to deploy at scale means manufacturers can test multiple scenarios virtually, which reduces costs, speeds up time to market, and increases product quality. As a result, simulation technology like digital twins is rapidly replacing large parts of the physical prototyping process.
The availability of advanced data management solutions means that simulation technology can be easily integrated into existing workflows. Manufacturers can increase their return on investment by starting with high-impact areas and gradually expanding as appropriate. Many types of simulation technology can also be quickly scaled, which makes it suitable for smaller shops.
Supply Chain Trends Related to Manufacturing
By enhancing visibility across the supply chain, digitalization opens up new possibilities for manufacturers. Better demand forecasting and reduced lead times allow organizations to fully embrace the just-in-time philosophy, which means items can be produced to meet demand instead of being produced in advance of need. This helps to reduce inventory levels, mitigate waste and lowers ongoing costs.
In addition, IoT integration allows real-time tracking and increased transparency throughout the entire supply chain. This can be used to highlight potential delays and disruptions, identify potential quality issues, and prevent defective products from reaching the customer.
While these digital solutions offer many benefits, integrating them into the supply chain can be complex. In Hexagon's survey, 34% of manufacturing leaders said that poor integration of automated technology with existing technology is a barrier to productivity and collaboration within the organization. To simplify the process, organizations should use modular solutions that can be integrated gradually and seek expert advice when it comes to complex integrations.
Increased digitalization can also introduce new security vulnerabilities across the organization. Given that the number and severity of cyber threats continue to rise each year, organizations should select vendors that can help implement cyber security measures and mitigate cyber security risks.
Manufacturers Must Stay Ahead of Shifting Trends
As manufacturers continue to transition away from paper-based systems, the industry is learning to embrace digital tools that help organizations integrate newer technologies.
Increasingly, innovations in AI are helping to improve quality control by automating inspections and enabling predictive maintenance to reduce errors and lower costs. Meanwhile, sophisticated simulation technology like digital twins is allowing organizations to create virtual prototypes and optimize processes more efficiently across the entire organization.
To remain competitive, manufacturers must resist the urge to shy away from industry changes and find ways to reap the benefits within their organizations. As these technology trends continue to shift, it is crucial to remain informed and adaptable.