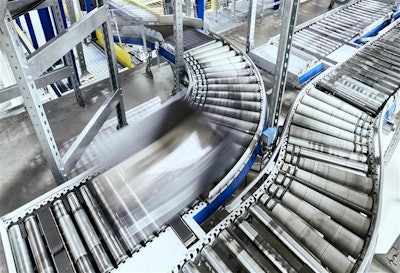
Supply chain disruption is easy for anyone to see, but the impact of the pandemic spreads far beyond toilet paper and household cleaner shortages. Since early 2020 and the emergence of the Coronavirus disease (COVID-19), issues like material and labor shortages coupled with increased demand have impacted nearly every industry. In a 2021 survey, the Institute of Supply Management reported that 56% of respondents cited shipment delays as their top COVID-19 concern, up from 16% in March 2020. Forty-three percent of respondents said their main concern was limited raw materials or supplies availability.
As the pandemic continues to surge into 2022, manufacturers will be wise to expect and prepare for further supply chain disruptions. But, what can be done to mitigate the damage?
How to alleviate ongoing supply chain challenges in manufacturing
It might be impossible to entirely right the wrongs of supply chain disruption as the pandemic continues, but manufacturers can turn to advanced technology to increase collaboration with different parts of their ecosystem. Sharing insights around the real-time health of production lines can improve transparency, bolster resiliency and generate new productivity efficiencies even as the supply chain continues to be unpredictable at best. Focus on enhanced, data-driven communication with the following steps:
1) Open your organization to industrywide collaboration.
Many companies might have once gained a competitive advantage by slowing down other companies and preventing them from innovating, but in the current landscape, that strategy is unlikely to bring long-term success. Manufacturers must adjust their mindsets to think about their companies as part of a larger effort within the manufacturing ecosystem. Combining experiences and learnings will help the industry thrive as a whole, while operating in silos will slow down supply chain recovery and harm every organization.
Engage with other industry experts via organizations, industry-specific consortiums or online groups. Discuss digital transformation in manufacturing, learn from each other’s mistakes and begin to think of the industry as a single organism to keep healthy so that your company can thrive within it.
2) Collaborate around data on the assets and performance of machines themselves.
Manufacturers must then consider the importance of establishing a single language to communicate about machines, and machine data and insights should be at its core. It’s about arriving at some standard by which manufacturers deem data useful, so elements like information around spare parts, maintenance, conditions where machines break, etc., can be useful when shared on a global scale.
For example, think about the standard for personal information to identify people in modern-day society. The U.S. government looks to details like ID, name, address and other fundamental data. Many companies rely on these standards, and some have even expanded the data pool, with companies creating huge troves of stats and identifiers for a person. Different companies hold different data, but share that data across other platforms for advertising. And, while no one oversees these standards for identification, except for when it comes to privacy rules and regulations, they are clear across the board.
Different companies use the same machines across various plants and products within the manufacturing ecosystem. Sharing machine health data provides incredible efficiency because manufacturers can gain insights and contextual information about how machines are managed to ensure optimal efficiency with their own assets. When plants buy machines, they invest in the asset for its entire life cycle. The more data and insights you can access about machine health and management, the longer the life cycle will be and the greater your returns.
3) Enable communication and collaboration at the technical level.
While some manufacturers already have forums to discuss value-added production principles or management layers for a plant, forums for manufacturing technicians to collaborate, learn and ask questions are lacking. Organizations that create more opportunities for industrywide collaboration at the technical level will gain an advantage over those that don’t.
Technicians should use tools that allow them to easily share data and insights with other employees, inside or outside the company, to collaborate and learn. But, management will first need to free up more of their time to seek out innovation and new ideas. Platforms that provide predictive maintenance and machine health insights allow teams to operate proactively, spending less time on reactive and time-based work and more time on future-forward thinking.
For manufacturing companies, surviving today’s supply chain disruptions and thriving well into the future will require more collaboration and innovation at the industry, company and ground levels.