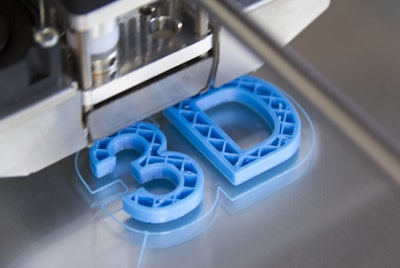
Experts are predicting you may find it hard to fill your holiday shopping list this year. As the year-end retail season gets underway, the global supply chain is still broken.
It’s easy to point to the Coronavirus disease (COVID-19) pandemic as the culprit, but the kinks in the supply chain have many causes. Even the industry analysts have never seen disasters compounding upon disasters as we have throughout the past 18 months.
That’s why it’s time to recognize that despite economic benefits globalization, there are now too many fragile links in the international supply chain. In the United States alone, the search for cheap labor that sent so much manufacturing offshore is a 20th Century impulse whose time has passed.
Highly automated and digitalized manufacturing technology fused with the marvels of the internet cloud help avoid many of the current supply chain problems by making products closer to the customers who need them.
How did we get here?
Consider the extent of the current predicament.
Shipping containers that brought medical supplies to distant parts of the world are now stockpiled in places far away from manufacturing centers. Labor shortages and quarantines mean there aren’t enough drivers for container chassis at major ports. Shipping bottlenecks have led to component shortages, which then lead to product shortages across the world.
Now, in many cases, the companies that haven’t been caught short are ones that stockpiled inventory. Good for them, but that’s hardly an efficient process or sustainable plan for the future.
For businesses that survive the season, this crisis should be a wake-up call as to how they manage their own supply chains. Companies must begin to move beyond outmoded approaches to design, prototyping and production in manufacturing, whose vulnerabilities are now clear.
It’s time to integrate digitally driven additive manufacturing — more commonly known as 3D printing — more fully into the manufacturing mainstream.
Why 3D printing?
The advantages of additive manufacturing for companies dealing with supply chain woes begin with its digital efficiency. Your company’s product essentially exists as a software file until it is sent, via the cloud, to a 3D printer located as close as possible to the end consumer. No container ship necessary.
Shrinking the distance to the consumer puts the advantage back with the manufacturer by eliminating the added costs and logistical challenges endemic with far-flung supply chains. Your “factory” can be located much closer to where your customers live.
Cloud-based software tools let designers and engineers design, prototype and refine complex structures on a single platform. Next-generation 3D technology delivers parts based on those designs with much less waste than other means.
How 3D printing works in the real world
It can be tempting for heads of manufacturing to default to familiar processes. For those who haven’t paid attention to how quickly the technology has advanced, 3D printing can even seem gimmicky and best left to home hobbyists. That thinking is at least 10 years out of date.
Cutting-edge companies around the world have embraced additive manufacturing as a foundation for their products – everything from car parts to sports equipment to COVID-19 testing swabs now come from 3D printing technology. In many cases, the products created through modern 3D printing technology provide significant mechanical performance advantages.
Bringing manufacturing closer to customers has given companies and their clients significant advantages.
Unleashing the benefits of 3D printing
The global supply chain problems are not going away soon. So, let’s stop thinking of this as a crisis and recognize that the world has changed, and so will the manufacturing model. What will it take for more manufacturers to follow suit?
For many business leaders, it means rethinking long-standing cost-benefit assumptions. Fortunately, when companies are considering a move toward 3D printing, their product and procurement officers are more engaged than ever in the conversation. Engineers and designers spot the advantages at once and take little convincing — if they’re not already clamoring for the change.
The real challenge to 3D printing tends to come from the head of manufacturing, who is rightfully cautious of how much time and money it will take to overhaul such a fundamental process. Fortunately, with recent advances in 3D printing software, it can be less capital-intensive than previous generations of injection molding or other methods of manufacturing. And that’s before reckoning the cost savings on shipping.
Companies that fail to answer the supply chain’s wake-up call risk the perpetual slumber of going out of business. Embracing 3D printing will help companies bring manufacturing closer to customers, bypass many of the supply chain complications and realize cost savings.
Those that stick only to the traditional ways will be left to hope their ships, eventually, come in.