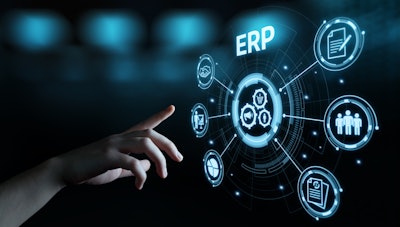
Rising consumer demand for ethically sourced and environmentally friendly products, new climate change legislation and growing pressure from stakeholders means sustainability is now front of mind for every organization. Simultaneously, an increasingly competitive and uncertain global economy of fast-rising materials and shipping costs is forcing manufacturers to implement intelligent, agile and cost-effective production processes to improve efficiency and throughput.
Fortunately, despite these converging challenges, businesses today have the digital tools to support collaboration with industry peers on a global scale. The rise of Internet of Things (IoT) connected smart factories provide manufacturers with the capabilities to leverage data insights from their shop floor and supply chains to develop end-to-end circularity in their sourcing, production, and distribution processes. This is helping to minimize unnecessary waste and reduce carbon emissions for more sustainable operations.
As more manufacturers and distributors move into a circular economy business model, decision makers are turning to innovation to support this transition, with 80% of CEOs increasing digital technology investments to counter current economic pressures. Alongside this, we see 87% of business leaders are expected to increase their organizations’ investment in sustainability initiatives over the next two years, creating a huge opportunity for technology providers and enterprise to successfully partner to support the transition to net zero profitably.
Innovation drives sustainable supply chains
With governments across the globe committed to achieving net zero carbon emissions by 2050, businesses that make, sell and move products are re-evaluating their extended supply and value chains to meet current industry expectations. The shift is significantly impacting manufacturers, who are turning to cloud-powered Enterprise Resource Planning (ERP) solutions and Manufacturing Execution Systems (MES) to maintain compliance with net zero legislation while remaining profitable.
More businesses are replacing their legacy system and switching from on-premises hardware in favor of cloud powered Software as a Service (SaaS) solutions, as part of this strategy. Based on the findings in recent findings by Epicor, a clear majority of enterprises in the automotive, building supply, care, distribution, manufacturing and retail industries are now more likely to use a hybrid cloud ERP solution - 96% of those surveyed are using some form of cloud ERP solution while nearly half (46%) are either primarily or entirely on the cloud.
Cloud ERP plays a vital role in empowering manufacturers and distributors to diversify their capabilities with minimal disruption and lower on-site energy consumption for more sustainable and cost-effective operations. This also supports more sustainable hybrid working practices by enabling workers to easily monitor all warehouse and production processes from anywhere with an internet connection.
Despite advancements in artificial intelligence (AI) and wireless connectivity helping to accelerate decarbonization efforts, a recurring problem for many businesses leaders is how to effectively measure and embed sustainability across their extended supply chains. Many rely on an integrated ERP system to analyze supply chain data and calculate the true cost of compliance. This means any disruption to the sourcing or distribution processes can be acted on immediately, to ensure products are not just profitable for the business but affordable for their customers.
Sustainability versus cost and availability
For sustainable supply chains, manufactures and distributors need to have easy access to accurate data on product quality, traceability, trackability, reuse or repair. With stock shortages, logistics challenges and inflation continuing to affect the sustainability versus cost and availability balance, deploying powerful digital solutions that can quickly convert real-time data into actional insights is critical to ensure greater business agility and resilience.
Manufacturers are being expected to incorporate sustainable materials into their solutions right from the initial product design phase. In response we are seeing a rise in digital tools that integrate Computer Aided Design (CAD) into ERP systems with guiding rules to ensure sustainable processes and materials are being used from the build. We are also seeing increased adoption of low code/ no code automation and analytics tools to overcome resource, materials, production, and delivery challenges, especially when intelligence can be shared to make circularity efforts cost-effective.
To overcome the sustainability challenges of the 21st century, manufacturers and distributors must work more collaboratively with their ecosystem of partners, suppliers and customers, as they move away from rigid manufacturing and supply in favor of onshoring and circular economy practices. Technology providers have an equal responsibility to listen and respond to their unique pain points, so they can customize industry-specific solutions that support intelligent manufacturing for a more sustainable future.