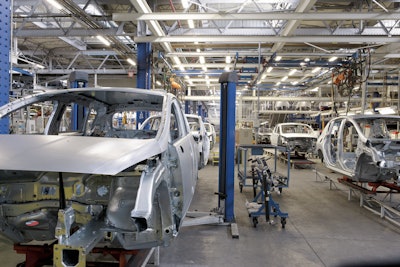
Manufacturers and retailers continue to reel over the logistics nightmare that is slowly unfolding across the global and U.S. stage. Shipping containers (from Shanghai) to the West Coast -- if you can find one -- for the holiday season can now cost as much as $32,000, an increase of over 400% in recent years.
But, ocean freight challenges only tell part of the story. Labor shortages, infrastructure shortages (including shutdowns and bottlenecks) and even warehouse capacity in North America continue to constrain nearly all aspects of truckload, less-than-truckload (LTL), last-mile and related supply chain transportation areas.
According to DAT, freight volumes hit a record in July, with DAT’s volume index rising over 100% to 222 from its baseline of 100 in 2015. From a cost perspective, according to DAT, summer spot prices were $2.73 per mile, an increase of over 70 cents from previous years, “setting records for all three equipment types.” Even last-mile delivery is a challenge, with 37.8% of last-mile delivery firms suggesting that finding qualified drivers to hire is a bigger issue.
Transportation capacity remains on a downward trajectory while prices and utilization are rising “at an increasing rate” and sector indexes have seen “capacity contracting for 15 consecutive months.” Conversely, tender reject indexes have been rising at a “at a higher clip starting around the same time.” Warehousing capacity is facing similar constraints, with a lack of available labor being referenced as the primary challenge curtailing availability.
What can manufacturers and retailers do to address these challenges?
A number of CEOs are facing logistics challenges that impact both the top and bottom line, all sharing a number of common themes and strategies.
First, plan ahead -- at the management level. CEOs and CFOs should be aware of the mitigation approaches that supply chain and procurement leaders are putting in place. This can include bringing procurement and supply chain functions closer together through the use of new technologies, including sourcing optimization, supply chain network design and supply chain analytics solutions. Capabilities such as these can allow for organizations to model all cost and non-cost variables for both “spot” and long-term supply chain and supply market considerations, factoring in logistics and a range of other variables. New solutions can even help manage asset vs. lease considerations on a total cost basis (and in the case of leasing, help negotiate down financing costs, which are often overlooked in total cost decisions).
Next, firms should prepare to pay more (and be willing to do so) for insurance -- not actual insurance, mind you, but insurance that buys forward inventory, visibility and capacity and mitigates against potential bottlenecks and cancellations. As part of this strategy, manufacturers should look to alternatives, including even developing their own fleet options. In the trucking industry, this could include not only owning capacity, but recruiting and training drivers as well, and offering incentives such as localized routes and weekends at home, which may impact direct costs in the short-term, but help keep employees who might otherwise leave over the long haul.
Another form of insurance is not one that procurement and supply chain professionals like to consider -- inventory. But, in a capacity constrained market with inflationary price pressures, holding additional inventory as a stopgap measure -- and potentially over an extended period -- may be the smart move to confront logistics, supply chain and broader supply market challenges. If we consider this as putting “lean” on ice for the near future, it may be a tip that even continuous improvement experts agree with over a short-term horizon given all of the logistics and supply challenges faced in recent months and expect to confront in the quarters to come.
Be the transportation supply chain. Own it. Even literally if you must.