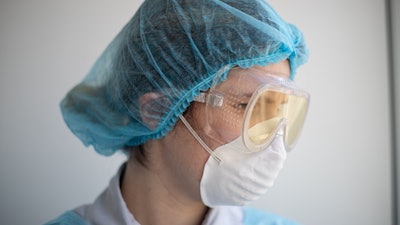
Almost overnight, medical ventilators became our most precious material resource.
It’s an unprecedented challenge for the medical supply chain, forcing outside manufacturers to contribute their time and resources to the effort. As hospitals continue to overflow, ventilators are making all the difference for those who can access them. For those who cannot, or for those whose shipments are lost or damaged along the way, incoming COVID-19 patients may not receive the lifesaving care they need.
Over the next several months, the production, delivery and sharing of medical ventilators will be a top priority for all, from hospital staff to the thousands of manufacturers involved. Furthermore, the history and health of each ventilator will be of critical import when banking on them to keep patients alive.
Ventilator location and status
“Where are the ventilators?” This is the very last thing a hospital director should have to wonder right now, as they work tirelessly to house, diagnose and treat thousands of new patients. The COVID-19 crisis may be the most pertinent use case for real-time asset tracking in our lifetime, outside of military aid and operations.
As of now, standard retail for this equipment is out the window. Ventilators are being churned out of makeshift factory lines and temporary wings of enterprise factories (e.g. carmakers, aerospace firms) and shipped across the country or world with no room for error or delay. Some independent designers are even building unorthodox ventilators with their available materials. Anything helps, and though by all accounts we should have been better prepared, the crisis is bringing people together like few events in history.
Plus, the ongoing exchange of ventilators between states will be a major storyline to follow for the next several months of the COVID-19 crisis, along with the full-steam production and shipment of new machines. Until supply matches the demand across the board, these devices will be a currency of sorts that are passed around the country each day. As such, tracking their location and active status will be a key measure of the crisis response, on par with hospital staffing and patient care.
Device history and performance data
Medical professionals must not only procure and track thousands of ventilators, surgical masks and other materials, but also ensure their quality and authenticity upon arrival. If a ventilator was potentially tampered with, or its delivery is disrupted in any way, hospital teams need to know so they can adjust accordingly. Moreover, those involved at every touchpoint require details about the current health and efficacy of these costly, complex assets — before planning to hinge a patient’s life on whether one works as intended.
If a machine failed at some point and needed repairs, or displayed any “exceptions” in its overall performance, that’s data worth knowing among hospital workers, operators and anyone else in the supply chain. Details such as these are not only paramount when ordering and receiving ventilators, but pertinent for when considering potential suppliers. If devices sent from a certain company fail 40% of the time, for instance, you should know this before asking them for help over other providers.
Ideally, asset stakeholders would get context-specific insights for any asset or item affixed with unique barcode technology. Data can include change of ownership details and location logs as well as historical records of any and all issues. Even before the COVID-19 pandemic, companies strived to provide customers with comprehensive, timely information about their shippable assets. Today, this approach can help address the crisis and help assist in preventing a possible crisis with ventilator distribution and operation.
Device accountability and the FDA
The FDA, CDC and other agencies will be closely involved in oversight of the COVID-19 recovery effort, including ventilator usage and performance.
Any reportability of device failures and exceptions for these agencies will go a long way in inevitable congressional hearings, where individuals or businesses may be held accountable for loss of life or related negligence. For example, if someone knowingly sold a malfunctioning ventilator to a hospital, reported device data will be valuable evidence for families of those affected when seeking justice.
Tracking solutions will assist in the capture and filing of this data, so that these practices can be properly enforced across the board.
Counterfeiting and the grey market
Product counterfeiting is a wide-scale threat for businesses and consumers alike. Damages caused by counterfeit goods will reach an estimated $4.2 trillion by 2022; this does not factor in the health-related issues caused by counterfeit drugs, alcohol, food and other products. While the current global emergency is a unifying force for many, counterfeiters and others may view it as a golden opportunity to cash in at the expense of others.
The healthcare industry has been a focus since the beginning. Track-and-trace solutions can be used to bolster pharmaceutical traceability efforts, ensuring that the right medication makes it to those that need it most without risk of counterfeiting or mishandling.
With each critical and unpredictable new day, hospital directors can utilize these tools to know how far deliveries are and any relevant details about their handling, while being able to authenticate their legitimacy the moment they arrive.
But, these desperate times force the hand of many hospitals to seek ventilators and personal protective equipment (PPE) from third parties, due to mass shortages from trusted manufacturers. A great deal of sellers buy in bulk from original manufacturers and resell at an upcharge. These “grey market” goods present a number of ethical questions, like those hoarding toilet paper and selling it to neighbors in need. Grey market distribution can also lend to mistrust and concern among buyers that their products are legit or working properly.
The grey market will inevitably persist during this crisis, alongside the counterfeit market; the goal is to mitigate as much as possible, eliminating risk and uncertainty for OEMs and their customers.
Life beyond the crisis
There are countless lessons to be learned once the dust settles, and some inevitable, immediate shifts in thinking to be made in the healthcare industry. For instance, hospitals will be forced to overstock their supplies in a long-overdue response to federal warnings, while manufacturing of essential assets like ventilators may move closer to the countries and states ordering them.
In the meantime, the crisis at hand requires an outsized effort to adapt and prevail.
Tracking and authentication solutions can be an integral piece of the puzzle for those on both ends of the chain, helping to manage ventilators and PPE once they are produced and track them on the way to their final destination. They can also help to monitor asset location within hospitals themselves, optimizing patient care and minimizing stress for medical staff.
A silver lining to this global emergency is that it’s forcing the industry to think as a team, open our minds and work together toward a safer future. Macro improvements to healthcare operations and manufacturing are guaranteed and already underway.