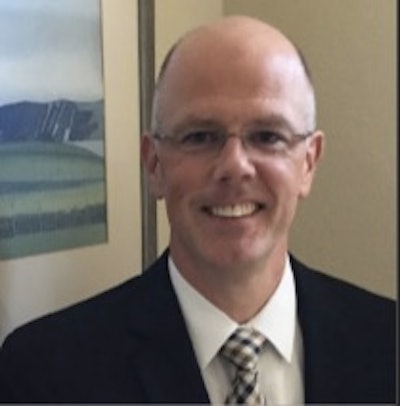
When inclement weather interrupts business along the supply chain, it doesn’t just affect workers on the production room floor. Relationships with the companies along the entire length of the chain also take a hit.
Let’s say, for instance, a vendor must shut down operation due to severe weather. It’s not an uncommon situation, yet, through no fault of its own, the primary business loses support. The primary business’ short-term success and long-term future is suddenly in peril. On the other hand, if things falter because of weather elsewhere along the supply chain, the vendor is left holding the bag with excess products or services that can’t be delivered or performed.
Or, what happens when a baker is scheduled to deliver goods to a restaurant, but is unable to make the drop due to weather? As a result, that restaurant may very well lose revenue, while also scrambling to find a replacement vendor. And should the eatery close, the vendor is left with goods that can’t be delivered.
This is a scenario that plagues many provider-customer relationships in not only the industries of food and hospitality, but also in automotive, electronic, retail and almost every other type of industry across the globe. No matter what you’re offering, executing the service relies on an efficient, effective, functioning supply chain. If extreme weather reveals a weak link in the chain, every other business on the line can falter (or suffer).
How to Weatherproof Your Supply Chain
Mid-crisis isn’t the time to make sure your supply chain’s ducks are in a row. Vendors, shippers and the primary business must all have their houses in order beforehand to ensure they’re still running during an emergency. With the rain pouring down or the hurricane just offshore, the executive team should feel confident and informed—they shouldn’t have to wonder about the very survivability of their business and supply chain(s).
If a company cares about its future and that of its supply chain relationships, all parties should be proactive about putting emergency provisions and procedures in place. Implement these five steps into your preparation to solidify and fortify your supply chain when Mother Nature is bearing down on it:
1. Construct a Continuity Protocol
Prepare for a crisis weeks and months ahead of a storm by creating a business continuity plan. That way, all contingencies are already considered and discussed by the time the extreme weather event arrives.
Business can continue with as few interruptions as possible if this plan details a secondary supply chain in the absence of the primary one. For example, a baker (the plastics supplier) and restaurant (automobile assembly plant) should work out secondary options for delivering and receiving baked goods (dashboards and door panel inserts) in case one or both is slammed by severe weather. The more bases you cover and the more scenarios you consider, the greater the chance a big storm doesn’t catch you off guard.
2. Put a Solid Depth Chart in Place
Back up all of your business’ vital systems in order to survive and meet obligations. No company should rely on only one form of contact and no company should rely on information from just one source.
Additionally, any company that relies on a backup generator during a weather-related power outage should have several options if it needs to top off on fuel. It would be embarrassing—not to mention costly—to spend time and money on an emergency generator and then still be shut down due to lack of gas. Plan for everything and nothing can surprise you.
3. Execute Many Dry Runs
Practice, practice and practice some more! Emergency procedures between supply chain partners should be rehearsed exhaustively long before a weather crisis strikes.
In 2001, it was well-documented that a lack of communication between police, fire, city, state and federal agencies caused major breakdowns during the 9/11 terrorist attacks. The mishap might have been avoided had all parties practiced a wide-scale, cooperative effort beforehand.
The same is true within a supply chain. If a primary truck fails, is it possible the substitute might be a different size, have a load that doesn’t fit, or contain loading equipment that’s either oversized or not big enough?
During a weather event, there is only one chance to get it right. Practice the continuity plan and call attention to overlooked details—both large and small—before it’s too late.
4. Never Stop Talking
Reach out early to other companies along the supply chain to ensure everyone is on the same page regarding possible weather-related disruptions. The idea is to eliminate surprises, so discuss topics such as anticipated slowdowns, staffing concerns, primary versus secondary equipment, closures, route detours, and how to communicate when one or more partners experiences a weather event.
Failure can lead to the termination of relationships along the supply chain (or even the end of one or more businesses within it). To avoid this, have lengthy conversations about preparedness and the ability to support one another in times of crisis before any contracts are signed. Don’t be shy when it comes to asking your partners what they’ve done to ensure their businesses can survive a disaster (weather or otherwise) and continue to support you. If you don’t like their answers, perhaps a different partner is in order.
5. Invest in Detection Technology
For impending weather-related disasters, all parties should have accurate and up-to-the-minute weather information specific to their facilities and areas of operations. You can’t find this detailed information from the National Weather Service or the local news station’s meteorologist. Their strength is public safety and public awareness, not supporting your business with detail and timeliness.
Businesses survive severe weather by being informed and prepared; you can, too, by contracting with a commercial service that provides custom weather reporting specific to your needs, and familiar with your business and concerns.
Whether the relationship is within food services, automotive, electronics or elsewhere, the best way to ensure success is to plan for continuity in the face of disaster. Get rid of the weak links early to help your supply chain relationships endure any storm.