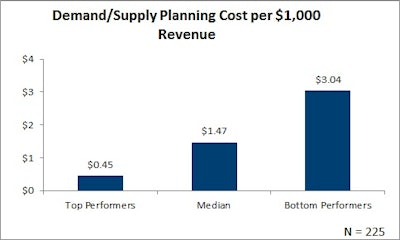
Demand and supply planning costs include those associated with forecasting or developing finished goods or end-item inventory plans, and coordinating the demand and supply process across the entire supply chain. The American Productivity and Quality Center’s (APQC’s) Open Standards Benchmarking data in supply chain planning shows there is a $2.59 difference between top- and bottom-performers regarding these costs per $1,000 in revenue. This represents a potential cost savings of $12.95 million for an organization with $5 billion in annual revenue.
Organizations can reduce planning costs by adopting enterprisewide systems or policies to standardize supply chain planning, regardless of whether the entire supply chain planning operation is centralized or decentralized. This standardization can lead to streamlined processes that require less time and fewer personnel to complete. Organizations can also use real-time demand data and alert notifications to determine when adjustments to the supply chain are needed and enact those adjustments as quickly as possible.
Having excellent insight into the materials needed and available from suppliers can help organizations act quickly to shifts in demand. While looking at internally collected data is helpful in understanding this, many organizations also collaborate with suppliers. Organizations collaborating with suppliers are more efficient in their supply chain planning efforts and ultimately have lower supply planning/demand costs.
A basic level of supplier collaboration can mean working with first-tier suppliers to determine short- or long-term requirements for particular products, and develop forecasts. To go beyond this, organizations can work with suppliers to obtain their inventory levels and capacities, which can then be used in the demand planning process. Organizations can also consider adopting the formal collaborative planning, forecasting and replenishment (CPFR) model to facilitate information sharing with their suppliers through a shared information system. This can aid both buyers and suppliers in understanding the inventory needed to meet market demand.