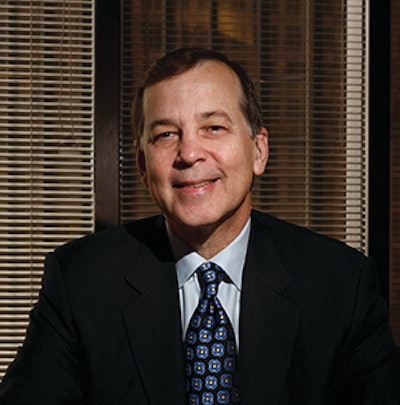
Chief financial officers (CFOs) know that supply chain performance has a direct impact on the bottom line. From balancing supply with demand to managing availability of inventory to managing a global distribution network, even the slightest miscalculation or interruption can be the deciding factor in announcing a profitable or unprofitable quarter.
Supply chain management, and specifically, supply chain risk management, is a strategic imperative for CFOs due to new and complex challenges in today’s global marketplace. For example, suppliers and third parties, both on and off shore, have an increasingly significant influence on supply continuity, company performance and brand image. As CFOs continue to drive efforts to reduce costs and manage working capital more effectively, supply chains continue to expand globally and inventories are becoming leaner, providing less margin for error.
We continue to find that the true value and financial impact of the supply chain is rarely viewed holistically to gain an understanding of the breadth and depth of the exposure. Rather, it is often viewed in silos, with issues and problems addressed as they arise.
But in today’s world, simply responding to issues with a “firefighting” mindset no longer suffices—this is not an effective approach to risk management. Consider the tragedy in Japan, which had a noticeable impact on the supply chains of many companies, including those in the steel, automotive, electronics and chemical industries. Immediately following the catastrophic tsunami, the resulting slowdowns and cessation of operations by so many companies raised questions regarding supply chain disruption risk and how to manage it.
Another example is the ongoing turmoil in the Middle East, which has the potential to adversely affect global supply chains, specifically with regard to possible disruption to oil supplies, and managing costs of hydrocarbon-based commodities and products.
Understanding Supply Chain Strategies and Risks
Supply strategies are complex by nature. There are many instances in which a single-source supply strategy is the right course of action, even when alternative options exist. The CFO, in collaboration with management, typically makes decisions to decrease inventory levels, rely on a single-source strategic supplier, and adopt just-in-time manufacturing and delivery techniques. These decisions involve trade-offs wherein quality, time and cost considerations often win out over business continuity considerations.
But supply chain disruptions are a reminder to CFOs that these trade-offs are not without risk. If the focus on supplier rationalization leads to extreme concentration, dependency and heavy emphasis on lean manufacturing leads to minimal buffers and tightly interconnected systems, disruption risk is further increased.
In today’s highly connected world, an end-to-end holistic or enterprise-wide view of the value chain is vital to understanding and managing operational risk. Supply chain risks can manifest themselves across a wide range of sources, including internal planning and operations, and those that impact a specific product, supplier, an entire category of spend and even those that are macro-economic in nature. This view requires the CFO to consider upstream supplier relationships, including the second- and possibly third-tier suppliers for strategic suppliers and categories, not to mention the logistics in linking these vital elements of the supply base with the company’s operations. The enterprise’s supplier relationships and the supporting supply network are just as important as its internal processes, personnel and systems because they are inextricably linked to what makes the business model work, albeit with less visibility. Therefore, any assessment of operational risk should be directed to understanding the risk of loss of any critical link in the supply chain.
When assessing supply chain disruption risk, CFOs need to ask appropriate questions regarding what could happen to the organization’s ability to fulfill customer orders and continue business operations if any key component of the supply chain were taken away through either failure or an unexpected catastrophe.
For example, which suppliers do we depend on for essential raw materials and component parts? What would happen if we were to lose one of them for any reason? How long would we be able to operate based on inventory buffers or supply or product alternatives? Are there other qualified sources of supply that can be readily available? Do we have inventory downstream in the supply chain to sustain operations during recovery?
What if there were:
- Temporary shortages in raw materials?
- Serious defects in supplier raw materials and component parts?
- Significant disruptions in transportation?
- Significant component or material price volatility, or spikes due to any of the above?
Do our key suppliers assess their risks? How do they manage their suppliers and supply chain? Do they have effective plans for responding in times of disaster and how do we know? Is there a formalized understanding and agreement in place?
When assessing the potential impact of a supply disruption, CFOs should consider the following:
- Visibility/transparency. How well are we monitoring our supply chain, and how quickly could we identify a potential issue and its impact?
- Velocity of the disruption. How quickly would we feel the initial impact?
- Persistence of the disruption. How long would we be affected if the disruption continued?
- Response readiness. How resilient would we be in reacting to the loss of any significant supply source?
When these additional factors are considered, risk management begins to intersect with crisis management. During business continuity planning, CFOs should consider all plausible scenarios stemming from the impact of losing strategic sources of supply for an indeterminate period of time.
Their objective should be to assess the immediate impact to the supply chain (e.g., specific suppliers, products and markets) in terms of both supply outage and financial impact, determine the expected recovery time following a severe supply disruption, and implement predefined and tested response plans to minimize the impact. This proactive stance is where many companies fall short and ultimately pay for the cost of inaction.
Strategies to expedite the recovery process should include identifying alternate suppliers or contract manufacturers that can assist following a no-notice manufacturing or logistics disruption. Contingency planning may also point to the merits of postponement strategies and inventory buffers to protect against the uncertainties of supply and demand, maintain customer service levels, as well as prepare for the unexpected.
If the company is reliant on a single-source supplier, finding alternative suppliers may require changing product specifications or working with other key suppliers to develop alternatives. Moving to an alternative supplier may carry risks of quality issues and must be managed carefully. It may be even more challenging in heavily regulated industries in which suppliers must be qualified. Supplier relationships honed over a period of years cannot be replaced overnight with an expectation of comparable performance levels.
In Closing
CFOs need to consider a number of key questions in assessing risks in the supply chains of their organizations. Do we take an end-to-end view of our supply chain when evaluating disruption risks, from second- or third-tier suppliers through customer fulfillment, or focus on a smaller scope initially? For critical suppliers, can we consider all relevant scenarios that could lead to supply disruption? Can we assess our resiliency and response strategies in the event of a supply chain disruption? By working with management and the board to address these questions, CFOs can make significant strides in advancing their organizations’ supply chain risk management.