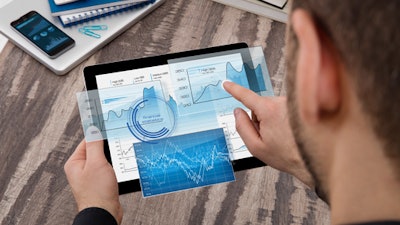
The Coronavirus disease (COVID-19) pandemic has disrupted trade and freight linkages, leading to a crippling shortage of containers like never seen before. Freight rates have skyrocketed and shipment delays have been a common issue across industries and sectors.
Worse, in March 2021, the Suez Canal — one of the world’s busiest trade routes — became blocked when a container vessel ran aground. It took six days to free the vessel, with hundreds of ships backed up on either side of the canal.
One estimate said the blockage was holding up trade valued at over $9 billion each day. Unfortunately, the actual cost is likely to be higher, given that the estimate does not include additional charges when ships had to reroute to take a longer path to their destination ports or changes in commodity prices.
These losses have hit many businesses directly, but other parts of the supply chain have also experienced trickle-down effects. In many cases, even the end consumer has been impacted.
How to cope with the ripple effect
The pandemic has forced a rethink in supply chain resilience, and pressure is mounting for the logistics industry to quickly adjust to the new landscape. Here are Top 4 must-dos for logistics leaders today.
1. Manage risk to ensure resilient operations.
COVID-19 threw a harsh spotlight on the lack of agility and flexibility of most supply chains. Now, more than ever, it is essential that the industry has a robust risk management network to manage disruptions. A good risk management framework identifies known and unknown risks. A typical unknown risk is a military coup in a country. A known risk could be a supplier’s financial troubles, which may disrupt the supply of specific components. Creating a risk management framework, assigning a weightage to every risk and constantly monitoring all the risks is essential for contingency planning, and ultimately improving supply chain efficiency and resilience.
2. Identify areas to optimize your network and bring down the total cost of ownership (TCO).
TCO is a concept that addresses all the costs in the supply chain. It includes everything from shipping costs and risk management costs to currency fluctuations. There is a range of metrics and KPIs that logistics companies can track to improve efficiencies and reduce costs. A ship utilization rate is one of the most critical operational metrics in the logistics industry. Tracking the amount of time the vessel is in use vs. in maintenance and repair can help optimize your network. Warehouse expenses is another reference of costs that needs close monitoring. Managing an optimized supply chain requires visibility on the TCO. Bringing down costs will also free up resources for innovation and the adoption of emerging technologies.
3. Automate and digitize.
Emerging technologies such as the Internet of Things (IoT), artificial intelligence (AI) and autonomous vehicles can play a positive disruptive role. One of the most significant innovations in the industry is the emergence of driverless trucks and cars, helping companies alleviate difficulties in finding adequate staff to drive the vehicles.
AI can also be applied to evaluating supply chain risk and developing a more robust strategic sourcing strategy. If there ever was a time in history that displayed the risks associated with suppliers, COVID-19 has managed to expose all the weaknesses associated to those providing services and raw material to our operations. For many, the pandemic presented a radical need to change to more local suppliers, financially stable suppliers able to endure the stress of a global catastrophe or suppliers with their own risk strategy plan already in place. Ensuring you have rapid and continuous scouting strategy can make one of the biggest and most important impacts on supply chain risk management.
4. Create and implement a multi-stakeholder engagement plan. Nothing moves until people move.
Any transformation you engage on, from implementing more robust supply chain networks to digitalization, will require you to engage all the people and communities involved in that change – starting with your own employees and suppliers. In the past, most change programs, including supply, operational and digital transformations, seem to lack the human element needed to actually engage people in successful transformation, yet alone accelerate it to drive company growth and hard, measurable outcomes.