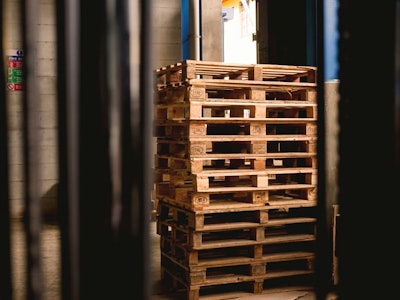
Developing a transparent, clean and sustainable supply chain strategy in an increasingly complex world is quite an endeavor. While globalization has dramatically increased competition, many companies have been looking to utilize the workforce in low-cost countries to remain competitive. However, the race for lower costs, added to externalization, can quickly damage a brand’s reputation when sourcing organizations lose visibility over their supply chains. Stories of companies from the textile industry have scarred other sectorisa. Many companies are now encouraged to evaluate their suppliers’ networks to avoid scandals, ensuring product quality and fairness.
For months, companies have to deal with a global pandemic, slowing or even interrupting supply chain operations and jeopardizing many businesses. Some borders are still closed, the workforce has been reduced and some products’ demand has exploded. Supply chain departments have to face their vulnerabilities and cope with enormous challenges. No company and no country is safe from shocks.
Because supply chains keep evolving, many questions have arisen. Are current sourcing strategies resilient enough to fight unpredicted events? What would be efficient and resilient solutions to ensure supply chain operations during such uncertain times? How can supply chain managers gain control over global suppliers in a pandemic situation?
External shocks and supply chain vulnerabilities
Supply chains have constantly been exposed to shocks: natural disasters, data breaches, financial crises, geopolitical disputes, etc. The magnitude of these shocks keeps rising and ends in disastrous economic consequences. In 2019 alone, 40 weather disasters caused damage to organizations exceeding $1 billion each. Companies have established resilient strategies to monitor their vulnerabilities. But, not all shocks are equal, and it is often the unpredicted events that have more impact.
A recent survey from McKinsey Global Institute states that shocks lasting a month or more occur every 3.7 years. The frequency of more minor shocks (1-4 weeks) is even lower (between 2-2.8 years). Supply chains are not exposed to the same shocks based on the industries and multiple variables. Because of their high digitization level, R&D and exposure to digital data flows, semiconductors are susceptible to cyberattacks and trade disputes but are less exposed to natural disasters. On the contrary, labor-intensive industries such as textile and furniture are primarily exposed to natural events (flooding, heat). Shocks may also emerge within the supply chain ecosystem, but these are more predictable (e.g. supplier bankruptcy, plant shutdown). In response, organizations tend to assess the risks and set up business recovery plans in case of disruptions. But, in most cases, these are unpredicted events that cause more damage.
Supply chain strategies are also affected by political and social factors. For instance, developing countries try to seduce industries with their low-cost labor market, while developed countries bet on their data security to host highly digital companies. Recent events such as the Coronavirus disease (COVID-19) have stressed the importance of self-sufficiency in pharmaceuticals and have accelerated some trends -- the growing role of digitization, the focus on proximity with customers, the ability to reply to sudden urges and the need for regionalization. The August 2020 McKinsey Global Institute’s survey estimates that 16-26% of global exports could relocate in the next five years. But, shifting production from one country to another has a cost that some companies are not ready to pay (e.g. industries with huge fixed investments).
Supply chains are highly exposed to shocks but seem to confirm the maxim saying that there is an opportunity in every crisis. Resilience should not be opposed to efficiency, and companies tend to prove that point.
Complexity, resilience and efficiency
Innovation is at the heart of every resilient and efficient supply chain strategy.
Implementing a digital twin (i.e. a digital copy of the supply chain activities), allowing companies to track their supply chain events, pays off. And, by “supply chain,” it is essential to understand the value chain from raw materials extraction in mines to the final product sold to customers in stores or online. The future stake is not only to monitor what and where Tier 1 suppliers buy, but also to understand what and where Tier 2 to Tier n suppliers buy their components. E-procurement software solutions helping companies create value through order automation, invoice processing and Rfx follow-up are not enough anymore. Supply chain managers must focus on even more strategic operational tasks, such as demand planning forecasts, analytics from finance and marketing and supplier innovation.
The last trend, though, was to acquire a full suite covering the end-to-end process. Benefits are numerous -- one single implementation, ease of change management, one solution provider meaning one single point of contact, low IT maintenance, discounts based on the number of modules purchased, etc. But, how do customers expect total efficiency on the value chain end-to-end process when not acquiring the best-in-class solution for their needs? Technology is growing as fast as market needs are. Still, companies keep spending a ton of money trying to fix data for their end-to-end solution to work efficiently when the problem might come from the solution itself. Developing a transparent and efficient supply chain strategy starts with acquiring the right tools, the ones designed for a sole purpose. That is why a modular approach is often preferred when companies want to get the best out of their information systems. Implementation and integration might be more complex, but outcomes are more significant.
To sum up, companies do not always value investing in innovative solutions to build resilient and efficient supply chains. Top management often pressures operations teams to look for short-term productivity -- +10% sales per year, -5% total costs, etc. If disruptive events tend to occur more frequently, only companies investing in supply chain innovation might survive in the long run. Such investments can also pay off on a short-term basis -- productivity boost, digital capabilities improvement, industry ecosystems strengthening.