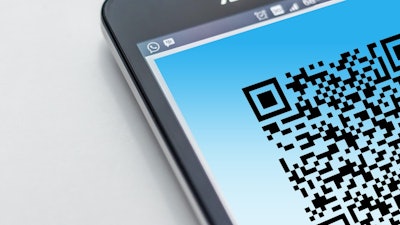
For supply chain managers, 2020 was a nightmare year. The Coronavirus disease (COVID-19) pandemic has disrupted global logistics chains at an unprecedented scale, and the situation has not changed in 2021. Businesses need to optimize any operations that rely on vendors or risk continued disruption and uncertainty.
Production is not the only process that relies on a steady supply of supplies. Machinery and other assets critical to the production of goods suffer from wear and tear over time. They require maintenance, which in turn, relies on a regular supply of spare parts.
Lack of an optimal maintenance strategy will lead to holdups and delays in production. These will have costly ripple effects on the entire supply chain of the business. Maintenance managers usually rely on one of three common maintenance strategies, each with a unique impact on a firm’s logistics and supply chains.
1. Reactive maintenance
In this relatively simplistic approach, the assets will be repaired only once they actually breakdown or reach a stage of wear and tear where repairs become unavoidable. As a result, it is also called breakdown maintenance.
Reactive maintenance is required in virtually all firms from time to time. But this strategy works well when it is restricted to inexpensive/unimportant assets that are not critical for the production process.
Advantages
● Requires less planning
● Lower initial and ongoing costs
Disadvantages
● More expensive in the long run
● Assets may have reduced lifespan due to lack of maintenance and frequent breakdowns
● May cause unexpected and costly production delays
● Higher safety risk to operators and employees
Implications for supply chains
In terms of ongoing impact, reactive maintenance strategy does not impose a significant burden on the firm’s supply chains. This strategy does not require a regular supply of spare parts, so vendor-side supply chains are only affected when there is a breakdown.
But, if there is a significant delay in production due to a severe breakdown of equipment, the customer-facing supply chains will be affected. Distribution networks will suffer holdups and freezes as the flow of products dry up.
With the global economy in shambles and markets in recessionary mode for the near future, firms have precious little leeway at the moment. Any disruption to production and supply chains could have disastrous consequences – a reactive maintenance strategy leaves far too many things to chance and is not at all suitable for this scenario.
2. Preventive maintenance
In virtually every aspect, this strategy is the antithesis of reactive maintenance. Instead of waiting for the machinery to breakdown, the business will take a proactive approach and try to prevent it from happening in the first place.
This involves period maintenance and repair work carried out at strict intervals. While it removes a lot of uncertainty regarding the risk of breakdowns and disruptions, that peace of mind comes at a significant cost in terms of staff, labor hours and supplies/spare parts.
Advantages
● Significantly reduces the risk of equipment failure
● Offers better on-site safety
● Prolongs the operational lifespan of machines
Disadvantages
● Requires small to moderate resource investments to get it off the ground
● Can be inefficient due to overestimation of maintenance requirements (maintenance needs to be planned around production schedule)
Implications for supply chains
With high demand for maintenance suppliers and spares, this strategy will add additional vendors and subcontractors to a firm’s supply chain. During an adverse event like COVID-19 lockdowns, it will put extra pressure on logistics managers to hunt for alternative vendors.
Some firms pursuing this strategy may be forced to stockpile spares and maintenance supplies as an insurance policy. But, on the bright side, it does reduce the risk on client-side logistics as it keeps the production line working smoothly and without incidents.
Due to the absence of any cheaper alternative, this maintenance strategy is favored by most businesses, at least as far as expensive and critical assets are concerned. But, going forward, they will need to look for more efficient alternatives.
For instance, preventive maintenance can be quite wasteful, as it involves conducting repairs regardless of the actual condition of the asset. It puts an avoidable burden on supply chains, overhead and even the environment, which is an important factor to consider in an era of sustainable goals.
3. Predictive maintenance
A relatively newer concept built on innovative technologies – Internet of Things (IoT), smart sensors, etc. – predictive maintenance strikes a fine balance between the extremes of the two other maintenance strategies.
Unlike reactive maintenance, it does not involve sitting around and waiting for a machine to fail. Instead, it relies on constant monitoring of assets using advanced sensors, when they pick up any early signs of wear and tear, the manager can schedule appropriate repairs or service.
Advantages
● Provides increased visibility into the condition of assets
● Helps prevent breakdowns and costly repairs
● Promotes asset longevity
● Is economical in the long run
Disadvantages
● The higher initial investment required in IT and tech
● It might be hard to retrofit sensors on very old equipment
● Requires trained staff
● Some of the cutting-edge technology is still in its early phases of development
Implications for supply chains
The modern global supply chain leverages IoT sensors and artificial intelligence in a big way for tracking shipments and optimizing delivery times. Using the same technology in maintenance management should help businesses improve supply chain efficiencies further.
The more calculated predictive maintenance strategy imposes less strain on a firm's supply chains. Insights into asset health allow managers to plan the number of parts they need to order from vendors well in advance. And, on the market side, fewer breakdowns mean that the flow of products to the clients remains undisturbed.
One of the side effects of the global pandemic has been the rapid adoption of digital technologies by businesses and their clients. As a novel strategy, predictive maintenance had found fewer adopters at the enterprise level before 2020.
That state of affairs should change in the coming months as more firms are compelled to seek improved efficiency in maintenance and supply chain management. Predictive maintenance holds a decisive edge over older strategies and should give enterprises the edge they need in dealing with an increasingly unpredictable business environment.