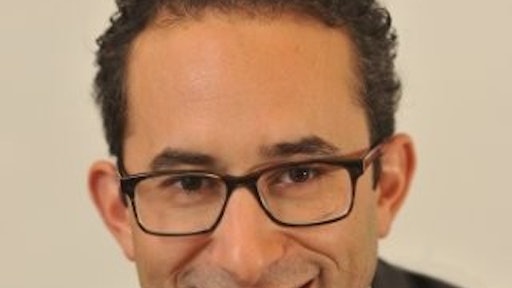
Most organizations are closely tracking how technology and data are changing the nature of work and jobs in supply chain – and rightly so. Many supply chain employees spend approximately 40 percent of their time on manual and redundant tasks, according to a recent survey by the Institute for Robotic Process Automation and Artificial Intelligence. With savings from technologies like robotic process automation (RPA) on average of 30-50 percent per FTE employee, technology is a smart move – but it’s not the only move.
The future of work in supply chain is being shaped across three dimensions.
- What work is essentially human? Technologies like cognitive, AI computing and robotics (both physical and software) are creating new opportunities for human and machine collaboration and empowering critical human capabilities.
- Who can do the work? Rethinking an organization’s talent mix to include on-balance sheet employees, freelancers, “as-a-service” work and open talent models will enable new ways to maximize the value and contributions of human capital.
- Where should the work be done? Virtual teams, augmented and virtual reality technology, location of skills and optimized physical spaces all provide opportunities for greater efficiency and collaboration.
Focusing only on technology misses the bigger opportunities from the future of work. Leaders focused on optimizing and automating tasks only see half the picture. The more compelling question is, how can we invent fundamentally more valuable ways of working the supply chain?
Small moves can set big things in motion. Here are some tips to consider:
Rethink the work, not just the job
With the impact of technology, the focus of all jobs will shift away from routine tasks. In the supply chain industry, every position is being impacted, including upper management and executives. Work in supply chain is often about efficient, consistent execution, and those are exactly the tasks most likely to be automated.
Rethinking work is about inventing new ways for people to generate value in the supply chain. If organizations focus on process optimization alone – without rethinking work – they may find their supply chains facing a discovery and creativity gap. Optimized for efficiency rather than discovery and experimentation, problem solving and troubleshooting skills will likely lag. It is a challenge to balance the efficiencies gained through automation and AI.
Machines can do great work, but for the near future, the best bet for differentiation is by combining technology with human ingenuity, empathy and creativity.
Leverage where and who, not just what
Many supply chains have solely focused on automation, given the potential gains in this area, but it can’t end there.
The talent shortage in supply chain already exists and is getting worse as the skills needed have become more complex. This situation is exacerbated by the difficulties of getting key talent in the same location as supply chain infrastructure. Leaders need to look at “who can do the work” and “where should the work be done” in concert with what the work is.
As we move closer to an open talent economy, talent will no longer have to live on the balance sheet. Organizations will be able to leverage diverse talent models to solve specific problems. Freelancers and gig workers can provide flexible labor, while “as-a-service” and borrowed talent provides access to scarce skills. To address the challenges of finding and building analytics talent, for example, many companies access analytics and data scientists “as-a-service” in an agency model similar to how they access marketing talent.
Combining the flexibility of who can do the work with changes in where work can be done magnifies the benefits. Technologies such as sensors, internet of things, and augmented reality/virtual reality provide access to data and resources that create improvement opportunities and the ability to locate talent anywhere – where you can capitalize on low cost or high skill talent markets and on shared, centralized resource pools. This effect is especially significant in higher-order jobs that often don’t require physical proximity to the supply chain infrastructure, such as process engineering, maintenance and quality control jobs are all targets.
Build the human skills you will need
The retooling and maintenance required in the human part of supply chain is one of the biggest misses organizations make after implementing other improvements. Data and technology fall flat when people don’t know what to do with it. When the focus is on driving cost savings from technology investments, dealing with added costs for training is often a welcome discussion.
Skills become irrelevant in a much shorter time now. Ongoing, continuous training is needed— and not just in technical skills. People need to learn how to keep learning. Flexibility, troubleshooting and adapting to changing conditions are key skills. As organizations rethink the work, they need to build models that encourage continuous learning, improve individual mobility and foster a growth mindset in every employee.
From the beginning, organizations should plan to roll the first wave of savings back into training budgets. Don’t rely on traditional approaches or Learning and Development team – supply chain needs to keep this one in supply chain. Instead, build training that builds supply chain value. Pick a single front line work environment that is pivotal to performance, and charge workers there with a purposeful goal or question. Using a systematic approach, create the space for them to experiment. Track key performance metrics, particularly those related to value delivered rather than just cost of delivering and iterate as you learn. Training needs and what is required to close them will fall naturally from that work.
One of today’s major issues, which extends beyond business to impact both economics and public policy, is that we must rethink work and help people cultivate the capabilities required to succeed in this new kind of work. Until employers are able to help people strengthen agility and passion, there will continue to be a discovery gap with risks of falling prey to the efficiency trap.